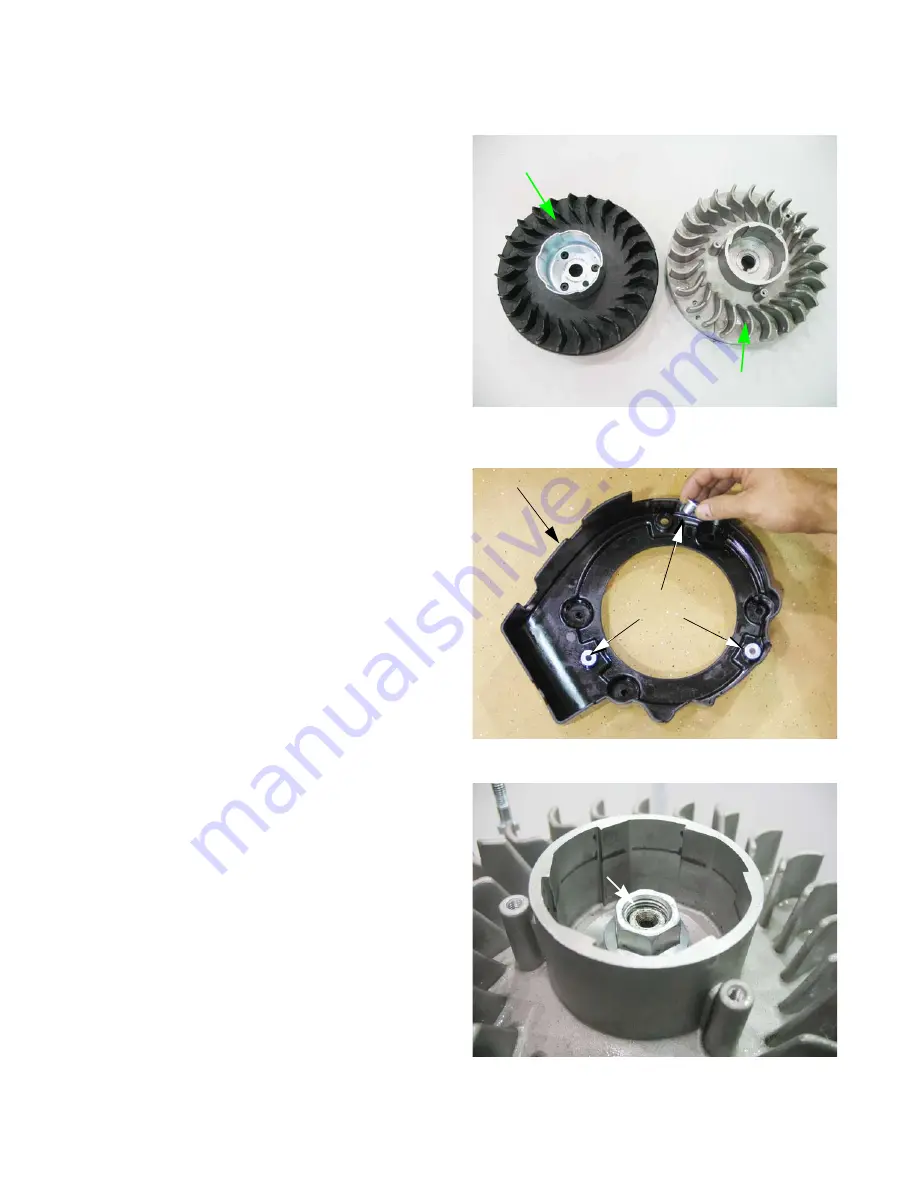
61, 65 and 70 Series Vertical Shaft Engines
96
Flywheel
There are two types of flywheels available for the MTD
engine. An aluminum flywheel and a 3-piece cast iron fly-
wheel. See Figure 7.22.
NOTE:
The procedure for removing the flywheel is
the same for both aluminum and cast iron
flywheels.
To remove the flywheel:
1.
Remove the recoil assembly by following the steps
described in Chapter 6: Starter.
2.
Lift the fan shroud off of the three studs that locate
it. See Figure 7.23.
3.
Loosen the flywheel nut until it is a couple of threads
past the end of the crank shaft using a 19mm
wrench. See Figure 7.24.
Figure 7.22
Cast iron flywheel
Aluminum flywheel
Figure 7.23
Fan shroud
Shoulder
bushings
Shoulder
bushings fit
over studs
Figure 7.24
A couple of threads past
the end of the crank shaft
Содержание 61 series
Страница 2: ......
Страница 6: ...IV...
Страница 22: ...61 65 and 70 Series Vertical Shaft Engines 16...
Страница 34: ...61 65 and 70 Series Vertical Shaft Engines 28...
Страница 42: ...61 65 and 70 Series Vertical Shaft Engines 36...
Страница 78: ...61 65 and 70 Series Vertical Shaft Engines 72...
Страница 90: ...61 65 and 70 Series Vertical Shaft Engines 84...
Страница 114: ...61 65 and 70 Series Vertical Shaft Engines 108...
Страница 141: ......
Страница 142: ...MTD Products Inc Product Training and Education Department FORM NUMBER 769 03354 02 12 2013...