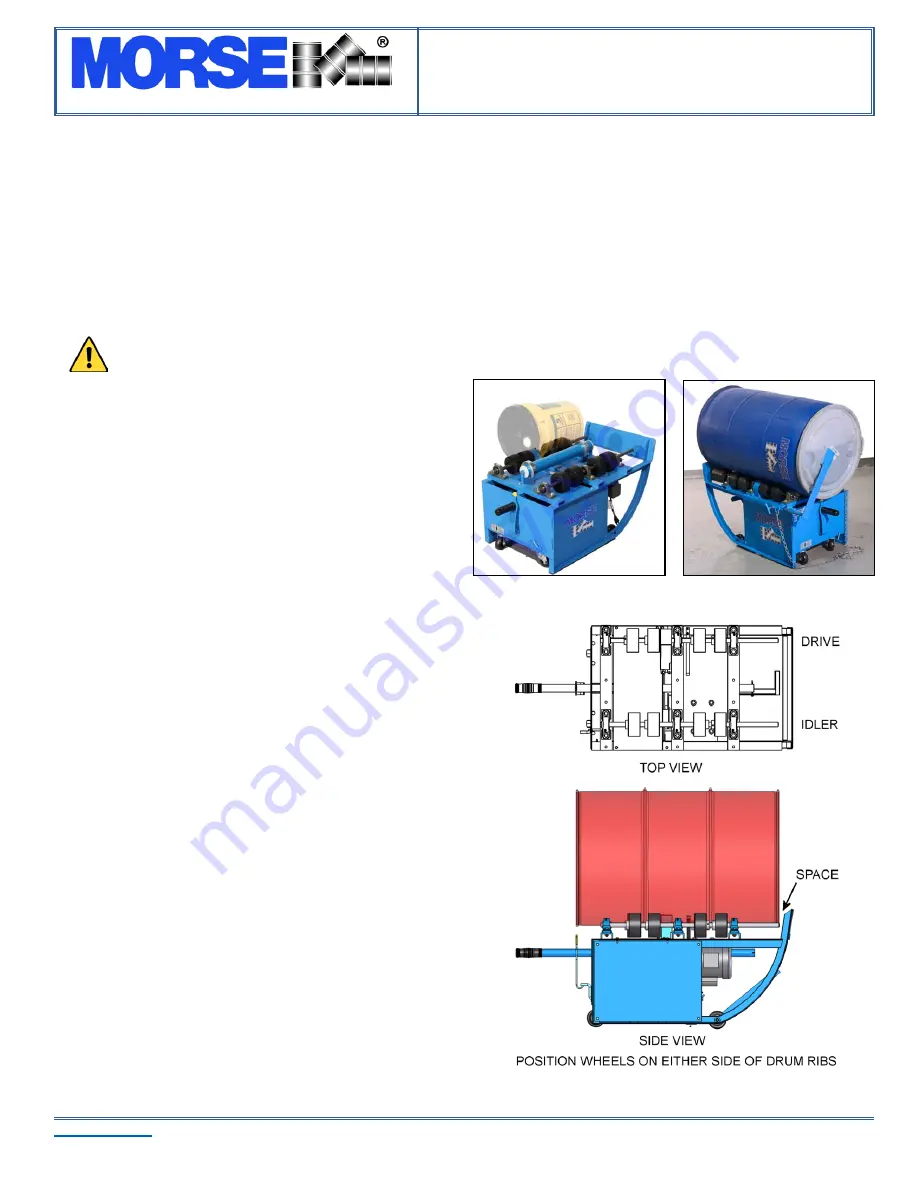
The Specialist In Drum Handling Equipment
201 Series
Portable Drum Rollers
operator’s Manual for Morse 201 Series Portable Drum Rollers
Serial number 286584 to ______
morsedrum.com
Copyright 2019 - Morse Mfg. Co., Inc.
Form OM201 (286584-______)
(Updated 22 Jul, 2020)
3
Machine Description
The 201 Series Drum Rollers are designed to roll a steel drum, 6” to 28” (15.2 to 71.1 cm) in diameter, and up to 37” (94 cm) long.
Fixed speed models roll a 22.5” (57.2 cm) diameter drum at 20 RPM.
•
The 201VS Series has Variable Speed from 15 to 24 RPM. The drum rotation speed is based on a 22.5” (57.2 cm) diameter
•
55-gallon (210 liter) steel drum and a 60 Hz, 1725 RPM motor. The drum rotation speed decreases with a 50 Hz motor.
Capacity:
The maximum liquid load capacity rating is 500 Lb. (227 kg).
•
Dry load capacity is 300 Lb. (136 kg).
•
WARnInG -
DO NOT exceed these ratings. Exceeding these ratings or handling a drum other than those mentioned above
is unsafe and could result in equipment damage,
excessive wear, motor overload and shortened service
life of transmission components.
options
option # 1-5P
•
(top right) - Install this Idler Attachment to roll a
1 to 5 gallon can or pail on a Portable Drum Roller.
A 55-gallon plastic drum can be rotated with the correct POLY
•
option installed.
Order
•
option # PoLY-201
factory installed on your new
201 Series Drum Roller.
Order
•
option # PoLY-201FI
for field installation of POLY
Kit on your existing 201 Series Drum Roller.
Important
Review the Material Safety Data Sheet(s) for the material(s) in
1.
the drum(s) and take all necessary precautions. Safety shoes,
work gloves, hard hat and other personal protective devices are
recommended.
Please read all instructions thoroughly before attempting to
2.
operate your new Morse drum handler.
When loading, unloading, operating, or maintaining your MORSE
3.
drum Roller, always use care and good judgment. Maintain
secure footing and a firm hold. Keep hands and loose clothing
away from all moving parts. Never allow anyone to be below
any part of a raised drum handler or drum. Read operating
instructions and review the pictures in the sales brochure before
operation.
Morse Rollers do not comply with OSHA unless they are installed
4.
in accordance with OSHA subpart O, 1910.212 - “General
requirements for all machines.” Morse Rollers should be installed
in accordance with OSHA requirements for enclosure and
interlock, etc. Power connections and motor controls must comply
with applicable codes.
Prior to initial use, inspect all moving parts. Perform necessary
5.
inspections, operator training, etc.
Figure 1
Option # 1-5P
Option # POLY-201