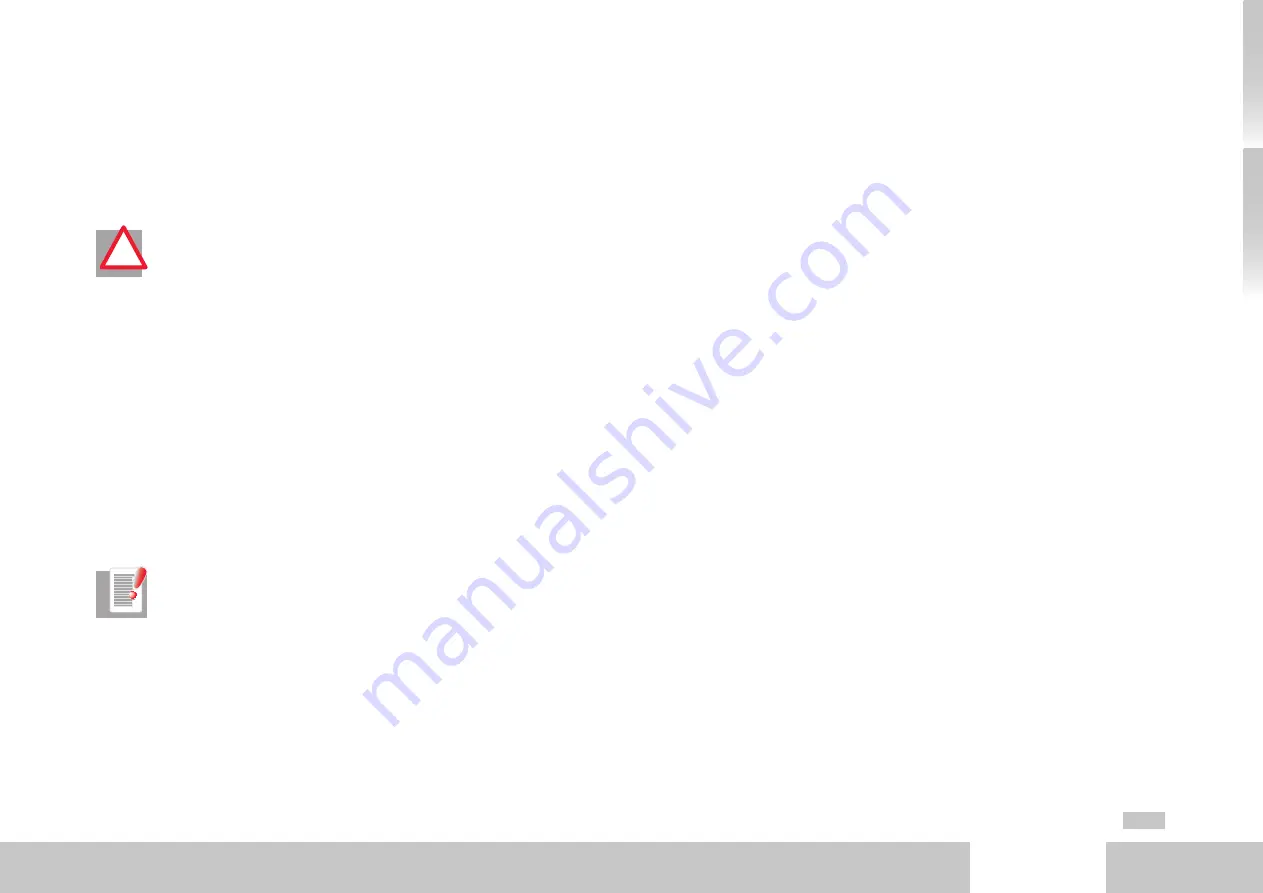
moog
MSD Servo Drive DC-AC Operation Manual
[
]
Mechanical
installation
11
Id.-No.: CA97554-001 Date: 06/2012
2 Mechanical installation
2.1 Notes for installation
!
ATTENTION!
•
During installation
please be sure to avoid ...
− drill chippings, screws or other foreign bodies dropping into the device;
− penetration of damp into the device
•
Switch cabinet
The device is solely intended for installation in a stationary switch cabinet.
The switch cabinet must as a minimum provide IP4x protection. When
using the STO (Safe Torque OFF) safety function, according to
EN ISO 13849-2 the switch cabinet must have IP54 protection or higher.
•
Immediate vicinity
− The servo drives must not be installed in areas where they would be
permanently exposed to vibrations. For more information refer to
tabe B.20 in the appendix.
− The device heats up in operation and at the heat sink may reach
temperatures of up to +100 °C (+212 °F). Pay attention to this in relation
to adjacent components.
NOTE:
For installation of the servo drive within a MSD Servo Drive multi-axis
system, be sure also to refer to the Operation Manual for the power supply
unit or the supplying single-axis servo drives.
The layout and installation of the DC-AC servo drives and the power supply unit is
subject to the following basic rules:
•
Pollution
Maximum pollution severity 2 to EN 60664-1. Further information on
environmental conditions can be found in table B.18 in the appendix.
•
Effective EMC installation
To attain the best result for effective EMC installation you should use a well
grounded chromated or galvanized backing plate. If backing plates are varnished,
remove the coating from the contact area. The devices themselves have an
aluminium rear panel (Size 1 to Size 4) or a rear panel made of aluminized/
galvanized sheet steel (Size 5, Size 6A).
•
Cooling
Cooling air must be able to flow through the device without restriction. For
mounting in switch cabinets with convection (= heat loss is discharged to the
outside via the cabinet walls), always fit an internal air circulation fan.
•
End-to-end mounting and alignment
− Devices with different housing variants (air-cooled and liquid-cooled) can be
installed next to each other in any combination, as devices with liquid-cooled
housings have a spacer on the rear in place of the heat sink. Consequently, it is
possible to connect to devices with air-cooled housings using the ready made-
up DC link cables without additional measures to compensate for differing unit
depth.
− No – minimum clearance between the devices is required. Exceptions to this rule
are the following air-cooled devices of size Size 6A (see Table 2.1). The maximum
distance between the devices is dictated by the supplied ready made-up cables,
and is 1.5 mm (except Size 6A).
− In the case of end-to-end mounting, the DC-AC servo drive must be sorted in
ascending
or
descending order of power.
− A vertical offset of 18.5 mm must be allowed between the top fixing screws for
devices of sizes Size 1 to Size 5 and devices of size B (see Fig. 2.6).
If you need more details on installation please contact the Moog Helpline (see page 50).
Содержание MSD G393-004
Страница 1: ...moog MSD Servo Drive DC AC Operation Manual Multi Axis System DC AC 565 to 770 V DC...
Страница 89: ......