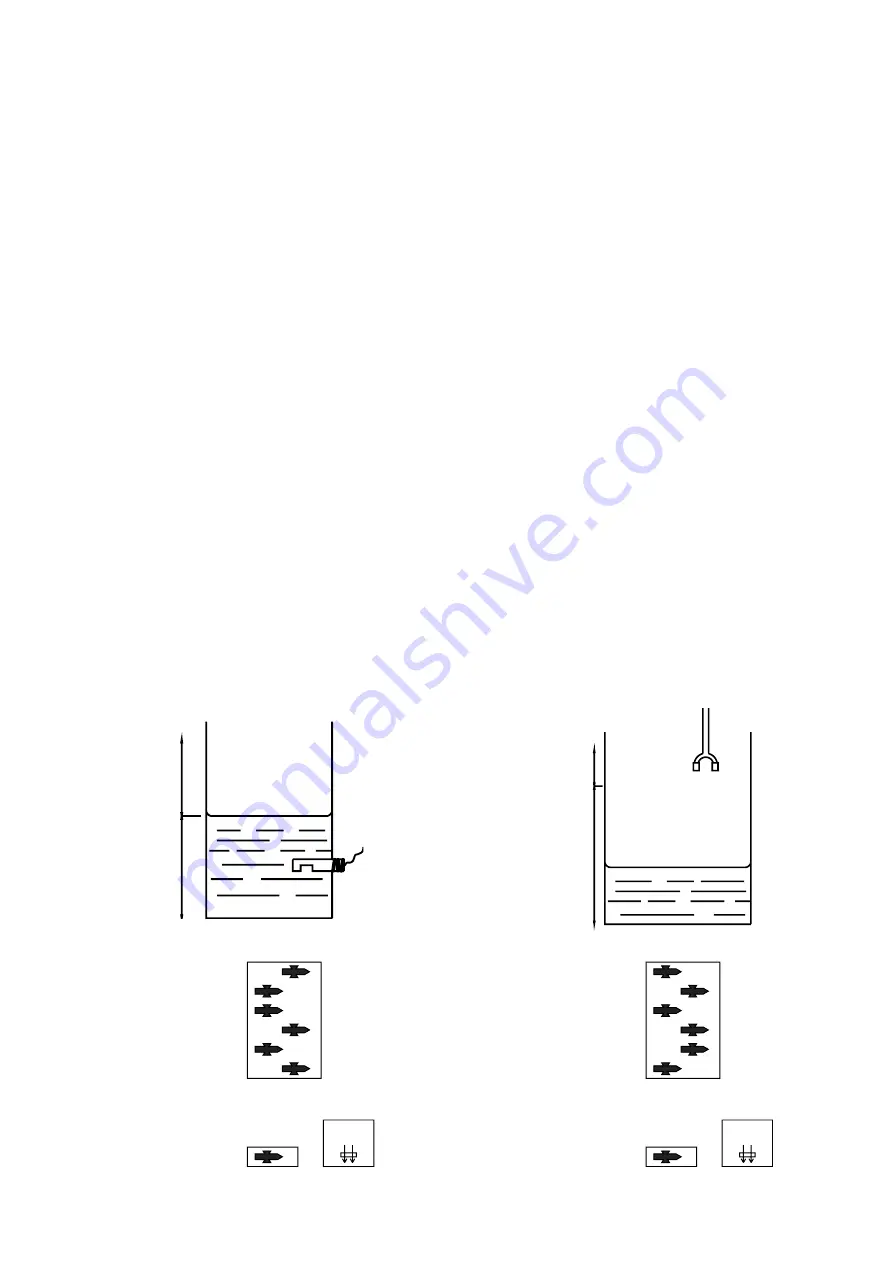
Fig. 8
in the normal condition. The example uses 1 MHz
sensors and 2 seconds delay before alarm, to prevent
wave action produced by stirrers triggering the alarm.
Gain adjustment:
(i) With sensor dry, reduce time delays to 2 seconds for
simpler adjustment. Set gain switch to “LO” and reduce
pot to “MIN”. Red LED will illuminate - this is the “false
wet”. Rotate the gain potentiometer clockwise slowly
until the green LED illuminates: note the setting (X).
(ii) Increase the gain setting X + 3 if it is necessary
to switch to the “HI” gain range, re-check for a “false
wet” position on the “HI” range, or assume an overlap
between “LO” and “HI” of 2 divisions of gain.
(iii) Check that the sensor when immersed in water
gives an alarm output. Recheck in the liquid to be
monitored.
(iv) Reset the time delays as needed.
Special site conditions:
In the above application the time delay can be used to
prevent high level alarms caused by splashing of the
sensor, by setting the green switch to “Delay to NE”.
Avoiding severe splashing or condensation effects may
require a slight increase in the gain setting to X + 4. To
detect splashing or for use on light oils the gain can be
reduced to X + 2.
3.3 Pump control and latching alarms
The output relay of the MCU200 can be latched into
the de-energised state. This latch is achieved by short
circuiting the two terminals of the Auxiliary input, labelled
as terminals 3 & 4 on the pc board (see figure 5). The
relay will remain de-energised while the latching short
circuit is applied. Only after this circuit is broken can the
relay re-energise under the control of the sensor.
A latching alarm can therefore be achieved by
connecting one pole of the output relay into the auxiliary
input, through a push to break “reset” button. NC1 and
C1 should be used to create this latch, with NC2, C2 and
NO2 being used for the external alarm circuit.
For a pump control application, switching a pump to
control a liquid between two sensors in a tank, this
auxiliary input can be used to monitor the second sensor.
The control system must be designed as follows:
(i) The pump to be latched “on” must be driven by the
MCU200 output relay.
(ii) The sensor attached directly to the MCU200 must
initiate the pump action to be latched.
(iii) The latched pump action occurs when the MCU200
relay is de-energised.
(iv) The separate sensor must be used to detect the
liquid presence at the switch off point.
(v) The signal from the separate sensor to switch off the
pump must be an open circuit, and is connected to the
auxiliary input in the MCU200.
In this example the number 6 switch (blue) on the
MCU200 would be set to OSC = E, so that when the
lower gap sensor sees air it de-energises the relay
to bring on the pump. With switch number 4 (yellow)
set to E = GREEN, the red LED illuminates when the
pump is running. With “Delay to NE” set at 2 seconds,
the sensor will ignore occasional bubbles or surface
turbulence which could trigger a pump start.
Switch Switchings:
Cable
Checking In
1 MHz
0.5 secs
E = Green
OSC = E
Page 8
Fig. 9
1 MHz
Cable
Checking In
OSC = NE
2 secs
E = Green
Delay to NE
Normal
Green
Normal
Green
Alarm
Red
Alarm
Red