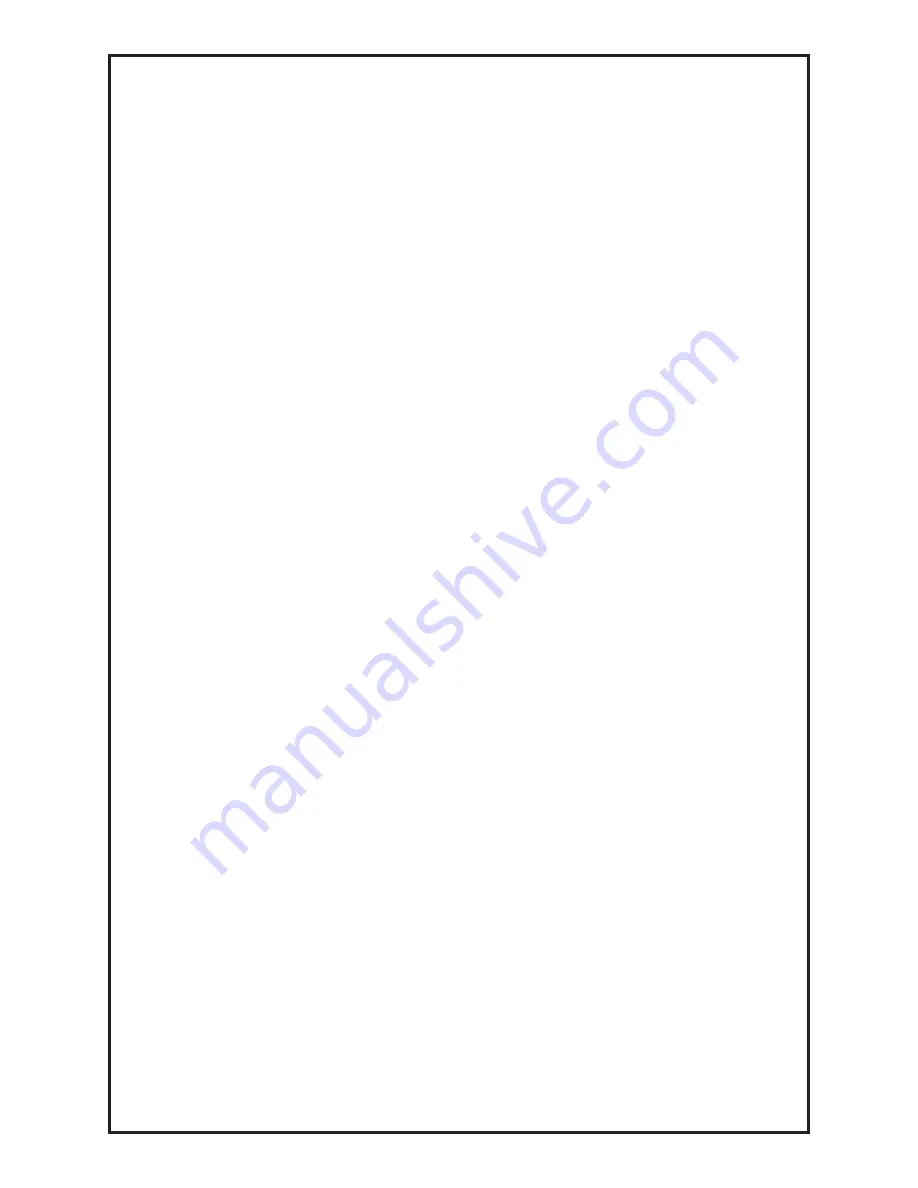
Cobramatic
®
Pro Series Safety
- Page iv
general rules cover many of the most
common situations.
1. Pressure Regulators
Regulator relief valve is designed
to protect only the regulator from
overpressure; it is not intended to
protect any downstream equipment.
Provide such protection with one or
more relief devices.
Never connect a regulator to a cylinder
containing gas other than that for which
the regulator was designed.
Remove faulty regulator from service
immediately for repair (first close
cylinder valve). The following symptoms
indicate a faulty regulator:
Leaks - if gas leaks externally.
Excessive Creep - if delivery pressure
continues to rise with downstream valve
closed.
Faulty Gauge - if gauge pointer does
not move off stop pin when pressurized,
nor returns to stop pin after pressure
release.
Repair. Do NOT attempt repair. Send
faulty regulators for repair to
manufacturer’s designated repair
center, where special techniques and
tools are used by trained personnel.
2. Cylinders
Cylinders must be handled carefully to
prevent leaks and damage to their walls,
valves, or safety devices:
Avoid electrical circuit contact with
cylinders including third rails, electrical
wires, or welding circuits. They can
produced short circuit arcs that may lead
to a serious accident. (See 1-3C)
ICC or DOT marking must be on each
cylinder. It is an assurance of safety
when the cylinder is properly handled.
Identifying gas content. Use only
cylinders with name of gas marked on
them; do not rely on color to identify gas
content. Notify supplier if unmarked.
NEVER DEFACE or alter name,
number, or other markings on a cylinder.
It is illegal and hazardous.
Empties: Keep valves closed, replace
caps securely; mark MT; keep them
separate from FULLS, and return
promptly.
Prohibited use. Never use a cylinder or
its contents for other than its intended
use, NEVER as a support or roller.
Locate or secure cylinders so they
cannot be knocked over.
Passageways and work areas. Keep
cylinders clear of areas where they may
be stuck.
Transporting cylinders. With a crane,
use a secure support such as a platform
or cradle. Do NOT lift cylinders off the
ground by their valves or caps, or by
chains, slings, or magnets.
Do NOT expose cylinders to excessive
heat, sparks, slag, and flame, etc. that
may cause rupture. Do not allow contents
to exceed 55 degrees C (130 degrees F.)
Cool with water spray where such exposure
exists.
Protect cylinders, particularly valves from
bumps, falls, falling objects, and weather.
Replace caps securely when moving
cylinders.
Stuck valve. Do NOT use a hammer or
wrench to open a cylinder valve that cannot
be opened by hand. Notify your supplier.
Mixing gases. NEVER try to mix any gases
in a cylinder.
NEVER refill any cylinder.
Cylinder fittings should never be modified
or exchanged.
3. Hose
Prohibited use. Never use hose other
than that designed for the specified gas. A
general hose identification rule is: red for
fuel gas, green for oxygen, and black for
inert gases.
Use ferrules or clamps designed for the
hose (not ordinary wire or other substitute)
as a binding to connect hoses to fittings.
No copper tubing splices. Use only
standard brass fittings to splice hose.
Avoid long runs to prevent kinks and abuse.
Suspend hose off ground to keep it from
being run over, stepped on, or otherwise
damaged.
Coil excess hose to prevent kinks and
tangles.
Protect hose from damage by sharp edges,
and by sparks, slag, and open flame.
Examine hose regularly for leaks, wear, and
loose connections. Immerse pressured
hose in water; bubbles indicate leaks
Repair leaky or worn hose by cutting area
out and splicing. Do NOT use tape.
4. Proper Connections
Clean cylinder valve outlet of impurities that
may clog orifices and damage seats before
connecting regulator. Except for hydrogen,
crack valve momentarily, pointing outlet
away from people and sources of ignition.
Wipe with a clean, lintless cloth.
Match regulator to cylinder. Before
connecting, check that the regulator label
and cylinder marking agree, and that the
regulator inlet and cylinder outlet match.
NEVER Connect a regulator designed
for a particular gas or gases to a cylinder
containing any other gas.
Tighten connections. When assembling
threaded connections, clean and smooth
seats where necessary. Tighten. If
connection leaks, disassemble, clean, and
retighten, using properly fitting wrench.
Adapters. Use a CGA adapter (available
from your supplier) between cylinder and
regulator, if one is required. Use two
wrenches to tighten adapter marked RIGHT
and LEFT HAND threads.
Regulator outlet (or hose) connections
may be identified by right hand threads for
oxygen and left hand threads (with grooved
hex on nut or shank) for fuel gas.
5. Pressurizing Steps:
Drain regulator of residual gas through
suitable vent before opening cylinder
(or manifold valve) by turning adjusting
screw in (clockwise). Draining prevents
excessive compression heat at high
pressure seat by allowing seat to open
on pressurization. Leave adjusting
screw engaged slightly on single-stage
regulators.
Stand to side of regulator while opening
cylinder valve.
Open cylinder valve slowly so that
regulator pressure increases slowly.
When gauge is pressurized (gauge
reaches regulator maximum) leave
cylinder valve in following position: for
oxygen and inert gases, open fully to
seal stem against possible leak; for fuel
gas, open to less than one turn to permit
quick emergency shut-off.
Use pressure charts (available from
your supplier) for safe and efficient
recommended pressure settings on
regulators.
Check for leaks on first pressurization
and regularly thereafter. Brush with
soap solution. Bubbles indicate leaks.
Clean off soapy water after test; dried
soap is combustible.
E. User Responsibilities
Follow all Safety Rules.
Remove leaky or defective equipment
from service immediately for repair. Read
and follow user manual instructions.
F. Leaving Equipment Unattended
Close gas supply at source and drain
gas.
G. Rope Staging-Support
Rope staging-support should not be
used for welding or cutting operation;
rope may burn.
1-3 ARC WELDING
Comply with precautions in 1-1, 1-2,
and this section. Arc Welding, properly
done, is a safe process, but a careless
operator invites trouble. The equipment
carries high currents at significant
voltages. The arc is very bright and hot.
Sparks fly, fumes rise, ultraviolet and
infrared energy radiates, weldments
are hot, and compressed gases may
be used. The wise operator avoids
unnecessary risks and protects himself
and others from accidents.
A. Burn Protection
Comply with precautions in 1-2.
The welding arc is intense and visibly
bright. Its radiation can damage eyes,
penetrate lightweight clothing, reflect
from light-colored surfaces, and burn
the skin and eyes. Skin burns resemble
acute sunburn; those from gas-shielded
arcs are more severe and painful.
DON’T GET BURNED; COMPLY WITH
PRECAUTIONS.
1. Protective Clothing
Wear long-sleeve clothing in addition to
gloves, hat, and shoes. As necessary,
Содержание Cobramatic Pro 150-008
Страница 2: ......
Страница 30: ...Cobramatic Pro Series Owner s Manual Page 22 Cobramatic Pro Series Block Diagram P N 071 0413...
Страница 31: ...Cobramatic Pro Series Owner s Manual Page 23 Cobramatic Pro Series Main PC Board P N 071 0400...
Страница 32: ...Cobramatic Pro Series Owner s Manual Page 24 Cobramatic Pro Series Main PC Board P N 071 0400...
Страница 33: ...Cobramatic Pro Series Owner s Manual Page 25 Cobramatic Pro Series Gun and Front Panel Connections P N 071 0412...
Страница 37: ...Cobramatic Pro Series Owner s Manual Page 29...
Страница 38: ...Cobramatic Pro Series Owner s Manual Page 30...
Страница 39: ...16882 Armstrong Ave Irvine CA 92606 Tel 949 863 1234 Fax 949 474 1428 www mkproducts com August 1 2010...
Страница 40: ...16882 Armstrong Ave Irvine California 92606 Tel 949 863 1234 Fax 949 474 1428 www mkproducts com...