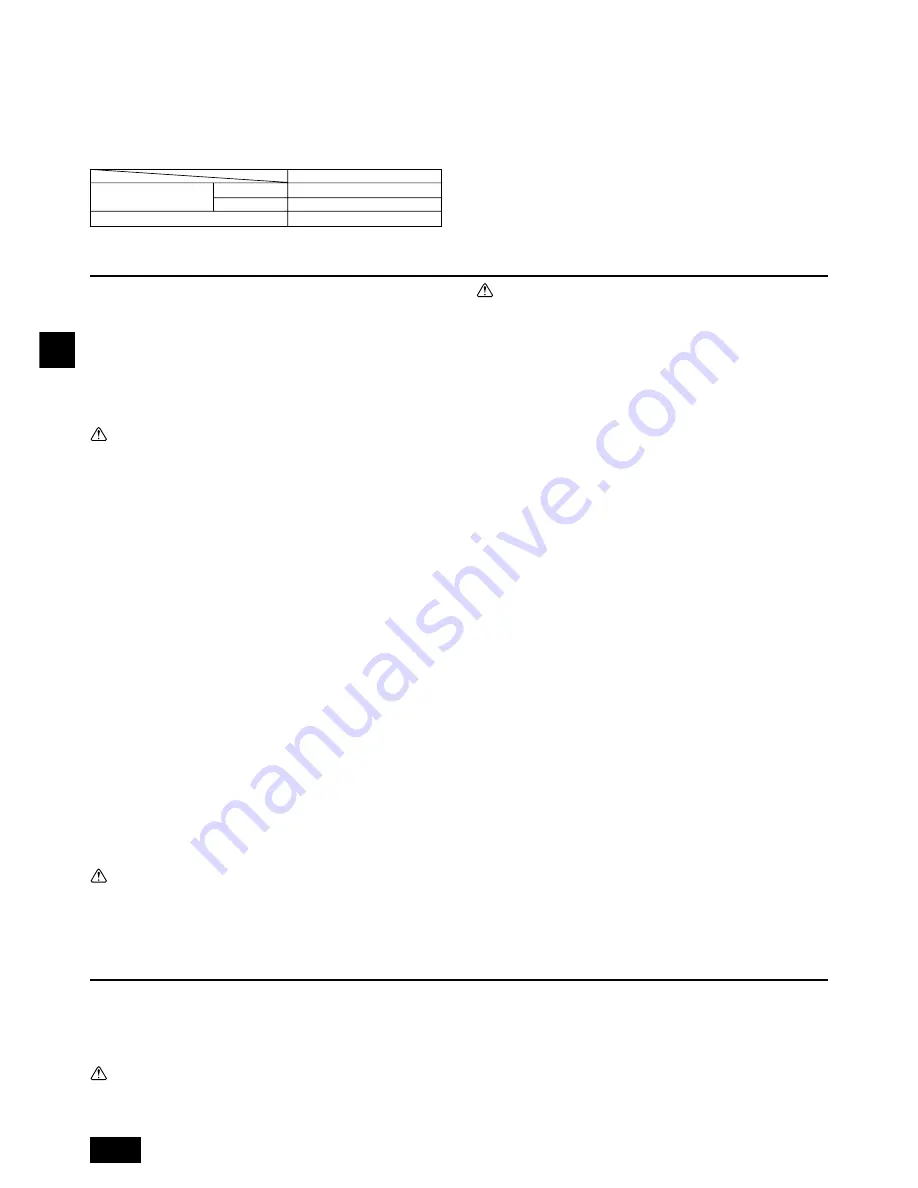
8
GB
D
F
E
I
NL
P
GR
RU
TR
CZ
SV
HG
PO
Caution:
•
Use refrigerant piping made of C1220 (Cu-DHP) phosphorus deoxidized
copper as specified in the JIS H3300 “Copper and copper alloy seamless
pipes and tubes”. In addition, be sure that the inner and outer surfaces of
the pipes are clean and free of hazardous sulphur, oxides, dust/dirt, shav-
ing particles, oils, moisture, or any other contaminant.
•
Never use existing refrigerant piping.
- The large amount of chlorine in conventional refrigerant and refrigerator oil
in the existing piping will cause the new refrigerant to deteriorate.
•
Store the piping to be used during installation indoors and keep both
ends of the piping sealed until just before brazing.
- If dust, dirt, or water gets into the refrigerant cycle, the oil will deteriorate and
the compressor may fail.
•
Use Suniso 4GS or 3GS (small amount) refrigerator oil to coat the flare
and flange connection part. (For models using R22)
•
Use ester oil, ether oil or alkylbenzene (small amount) as the refrigerator
oil to coat flares and flange connections. (For models using R410A or
R407C)
- The refrigerant used in the unit is highly hygroscopic and mixes with water
and will degrade the refrigerator oil.
8.2. Drain piping work
1.
Ensure that the drain piping is downward (pitch of more than 1/100) to the
outdoor (discharge) side. Do not provide any trap or irregularity on the way.
(
1
)
2. Ensure that any cross-wise drain piping is less than 20 m (excluding the differ-
ence of elevation). If the drain piping is long, provide metal braces to prevent it
from waving. Never provide any air vent pipe. Otherwise drain may be ejected.
3. Use a hard vinyl chloride pipe VP-25 (with an external diameter of 32 mm) for
drain piping.
4. Ensure that collected pipes are 10 cm lower than the unit body’s drain port as
shown in
2
.
5.
Do not provide any odor trap at the drain discharge port.
6. Put the end of the drain piping in a position where no odor is generated.
7. Do not put the end of the drain piping in any drain where ionic gases are
generated.
[Fig. 8.2.1] (P.3)
A
Downward slope 1/100 or more
B
Connection dia. R1 external thread
C
Indoor unit
D
Collective piping
E
Maximize this length to approx. 10 cm
9. Duct work
•
When connecting ducts, insert a canvas duct between the main body and the
duct.
•
Use non-combustible duct components.
•
Install sufficient thermal insulation to prevent condensation forming on outlet
duct flanges and outlet ducts.
Caution:
•
The noise from the intake will increase dramatically if intake
A
A
A
A
A
is fitted
directly beneath the main body. Intake
A
A
A
A
A
should therefore be installed as
far away from the main body as possible.
Particular care is required when using it with bottom inlet specifications.
•
To connect the air conditioner main body and the duct for potential equali-
zation.
•
Keep the distance between the inlet grille and the fan over 850 mm.
If it is less than 850 mm, install a safety guard not to touch the fan.
[Fig. 9.0.1] (P.3)
A
Air inlet
B
Air outlet
C
Access door
D
Ceiling surface
E
Canvas duct
F
Connect common reference potential wire between duct-work to air conditioner.
G
Air filter
H
Inlet grille
8. Connecting refrigerant pipes and drain pipes
8.1. Refrigerant piping work
This piping work must be done in accordance with the installation manuals for both
outdoor unit and BC controller (simultaneous cooling and heating series R2).
•
Series R2 is designed to operate in a system that the refrigerant pipe from an
outdoor unit is received by BC controller and branches at the BC controller to
connect between indoor units.
•
For constraints on pipe length and allowable difference of elevation, refer to
the outdoor unit manual.
•
The method of pipe connection is brazing connection.
Caution:
•
Install the refrigerant piping for the indoor unit in accordance with the
following.
1.
Cut the tip of the indoor unit piping, remove the gas, and then remove the
brazed cap.
[Fig. 8.1.1] (P.3)
A
Cut here
B
Remove brazed cap
2. Pull out the thermal insulation on the site refrigerant piping, braze the unit
piping, and replace the insulation in its original position.
Wrap the piping with insulating tape.
Note:
•
Pay strict attention when wrapping the copper piping since wrapping the
piping may cause condensation instead of preventing it.
*
Before brazing the refrigerant piping,
always wrap the piping on the main
body, and the thermal insulation piping, with damp cloths to prevent heat
shrinkage and burning the thermal insulation tubing.
Take care to ensure
that the flame does not come into contact with the main body itself.
[Fig. 8.1.2] (P.3)
A
Thermal insulation
B
Pull out insulation
C
Wrap with damp cloth
D
Return to original position
E
Ensure that there is no gap here
F
Wrap with insulating tape
Cautions On Refrigerant Piping
s
s
s
s
s
Be sure to use non-oxidative brazing for brazing to ensure that no for-
eign matter or moisture enter into the pipe.
s
s
s
s
s
Be sure to apply refrigerating machine oil over the flare connection seat-
ing surface and tighten the connection using a double spanner.
s
s
s
s
s
Provide a metal brace to support the refrigerant pipe so that no load is
imparted to the indoor unit end pipe. This metal brace should be pro-
vided 50 cm away from the indoor unit’s flare connection.
Warning:
When installing and moving the unit, do not charge it with refrigerant other
than the refrigerant specified on the unit.
- Mixing of a different refrigerant, air, etc. may cause the refrigerant cycle to mal-
function and result in severe damage.
2
If the unit is used on the highest story of a building and under conditions of
high temperature and humidity, it is necessary to use pipe size and insulating
material’s thickness more than those given in the table above.
3
If there are customer’s specifications, simply follow them.
7.1. Refrigerant pipe and drain pipe specifi-
cations
Item
Model
20·25·32
Liquid pipe
ø 6.35
Gas pipe
ø 12.7
Drain pipe
R1 (External thread)
Refrigerant pipe
(Brazing connection)
7.2. Refrigerant pipe, drain pipe and filling
port
[Fig. 7.2.1] (P.2)
A
Refrigerant pipe (liquid pipe): HP
B
Refrigerant pipe (gas pipe): LP
C
Drain pipe