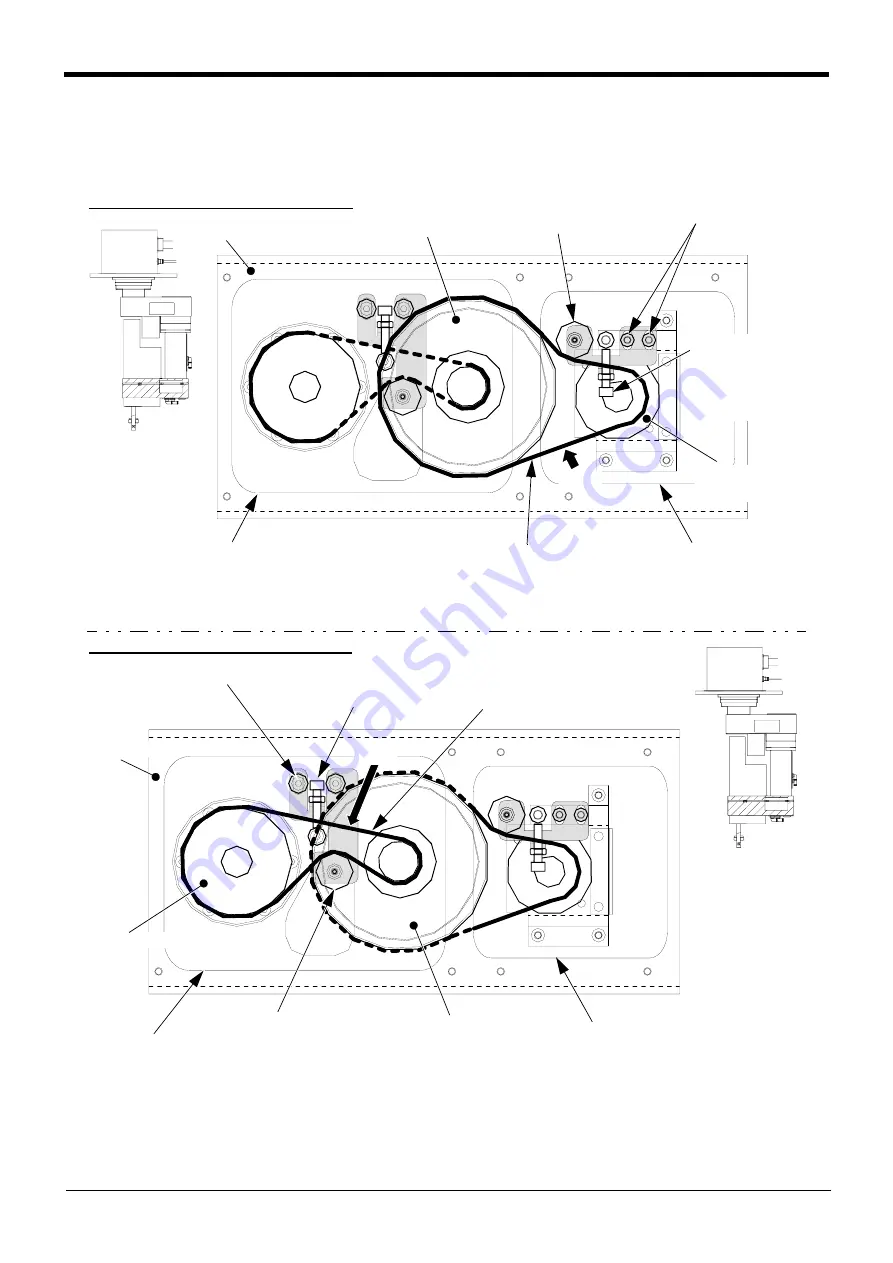
5-72
Maintenance and inspection procedures
5Maintenance and Inspection
(5) Inspection and maintenance of J4 axis timing belt
The reference figure at inspection and adjustment of the timing belt is shown in
.
There are the two belts of the motor side and the shaft side, in the J4 axis. Perform inspection and adjustment of
two belts simultaneously.
Fig.5-7 : Inspection, maintenance and cleaning of J4 axis timing belt
Note) The figure shows the timing belt structure section (motor side) inside the No.2 arm.
Remove and confirm the No.2 arm cover and the belt pulley cover J4.
The belt can be pushed and adjusted by removing the No.2 arm cover.
Idler
<2> Timing belt
<4> Timing
pulley
No.2 arm
No.2 arm cover section
Idler
<2> Timing belt
<A>
<5> Timing pulley
<4> Timing pulley
No.2 arm
No.2 arm cover section
Note) The figure shows the timing belt structure section (shaft side) inside the No.2 arm.
Remove and confirm the No.2 arm cover and the belt pulley cover J4.
Belt pulley cover J4 side
Belt pulley cover J4 side
<A>
Motor side (
Inside figure of No.2 arm
)
Shaft side (
Bottom view of No.2 arm
)
<3>Tension
adjustment
screw
With the fixing
nut
<1> Idler fixing screw
(two places)
<1> Idler fixing screw
(two places)
<5> Timing pulley
<3>Tension adjustment
screw
With the fixing nut
Содержание MELFA RH-3SDHR3512C
Страница 2: ......
Страница 112: ...Appendix 102 Configuration flag 6Appendix...
Страница 113: ......