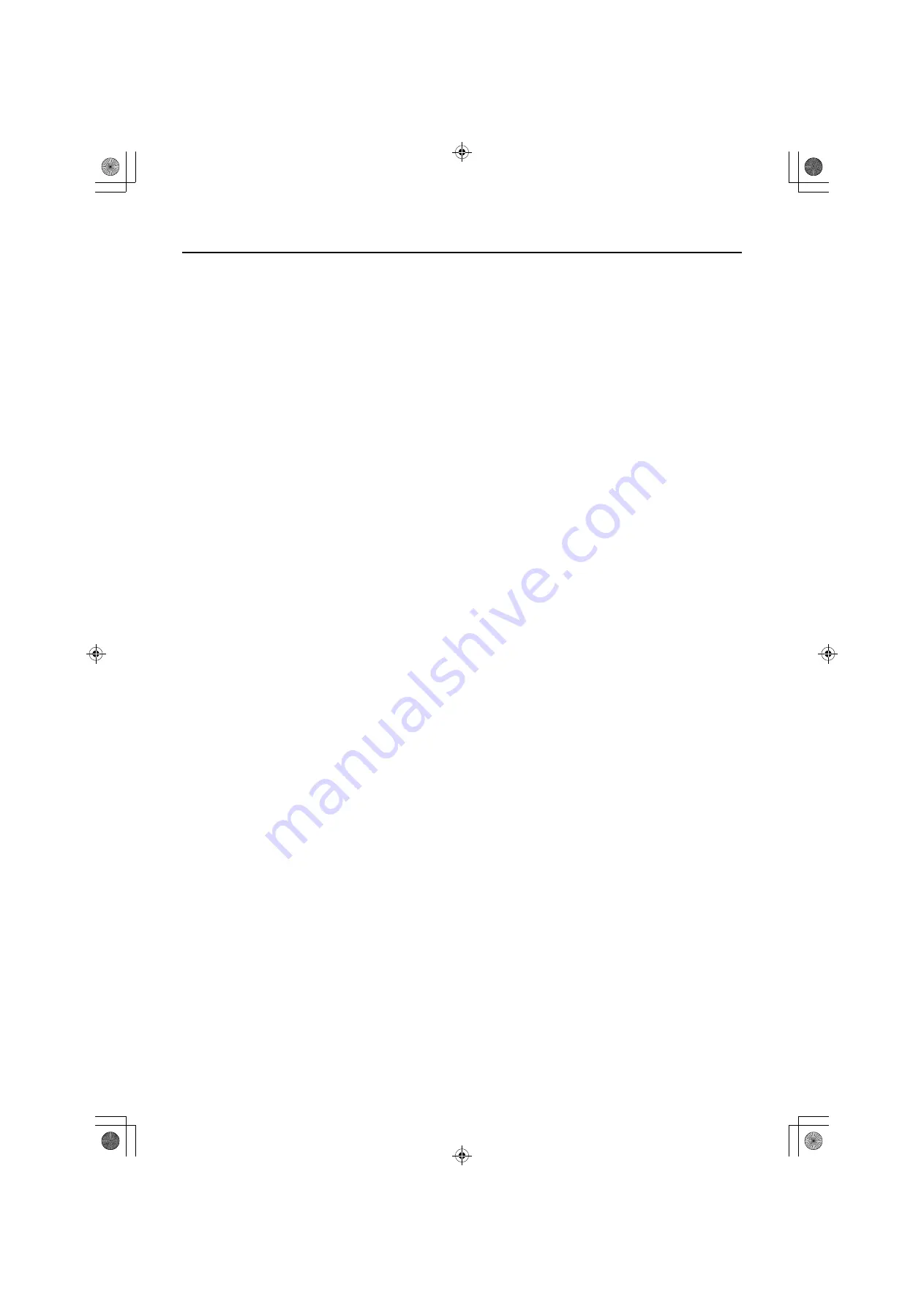
[
I
SAFETY PRECAUTION ]
- 5 -
HWE21010
GB
b) Isolate system electrically.
c) Before attempting the procedure, ensure that:
· mechanical handling equipment is available, if required, for handling refrigerant cylinders;
· all personal protective equipment is available and being used correctly;
· the recovery process is supervised at all times by a competent person;
· recovery equipment and cylinders conform to the appropriate standards.
d) Pump down refrigerant system, if possible.
e) If a vacuum is not possible, make a manifold so that refrigerant can be removed from various parts of the system.
f) Make sure that cylinder is situated on the scales before recovery takes place.
g) Start the recovery machine and operate in accordance with manufacturer’s instructions.
h) Do not overfill cylinders. (No more than 80 % volume liquid charge).
i) Do not exceed the maximum working pressure of the cylinder, even temporarily.
j) When the cylinders have been filled correctly and the process completed, make sure that the cylinders and the
equipment are removed from site promptly and all isolation valves on the equipment are closed off.
k) Recovered refrigerant shall not be charged into another refrigeration system unless it has been cleaned and checked.
(10) Labelling
Equipment shall be labelled stating that it has been de-commissioned and emptied of refrigerant. The label shall be dated
and signed. For appliances containing flammable refrigerants, ensure that there are labels on the equipment stating the
equipment contains flammable refrigerant.
(11) Recovery
When removing refrigerant from a system, either for servicing or decommissioning, it is recommended good practice that
all refrigerants are removed safely. When transferring refrigerant into cylinders, ensure that only appropriate refrigerant
recovery cylinders are employed. Ensure that the correct number of cylinders for holding the total system charge are
available. All cylinders to be used are designated for the recovered refrigerant and labelled for that refrigerant (i.e. special
cylinders for the recovery of refrigerant). Cylinders shall be complete with pressure-relief valve and associated shut-off
valves in good working order. Empty recovery cylinders are evacuated and, if possible, cooled before recovery occurs.
The recovery equipment shall be in good working order with a set of instructions concerning the equipment that is at hand
and shall be suitable for the recovery of all appropriate refrigerants including, when applicable, flammable refrigerants. In
addition, a set of calibrated weighing scales shall be available and in good working order. Hoses shall be complete with
leak-free disconnect couplings and in good condition. Before using the recovery machine, check that it is in satisfactory
working order, has been properly maintained and that any associated electrical components are sealed to prevent ignition
in the event of a refrigerant release. Consult manufacturer if in doubt.
The recovered refrigerant shall be returned to the refrigerant supplier in the correct recovery cylinder, and the relevant
waste transfer note arranged. Do not mix refrigerants in recovery units and especially not in cylinders. If compressors or
compressor oils are to be removed, ensure that they have been evacuated to an acceptable level to make certain that
flammable refrigerant does not remain within the lubricant. The evacuation process shall be carried out prior to returning
the compressor to the suppliers. Only electric heating to the compressor body shall be employed to accelerate this
process. When oil is drained from a system, it shall be carried out safely.
HWE21010.book 5 ページ 2021年6月24日 木曜日 午前9時0分
Содержание SEZ Series
Страница 1: ......
Страница 3: ...HWE21010 GB HWE21010 book 2 ページ 2021年6月24日 木曜日 午前9時0分 ...
Страница 52: ......