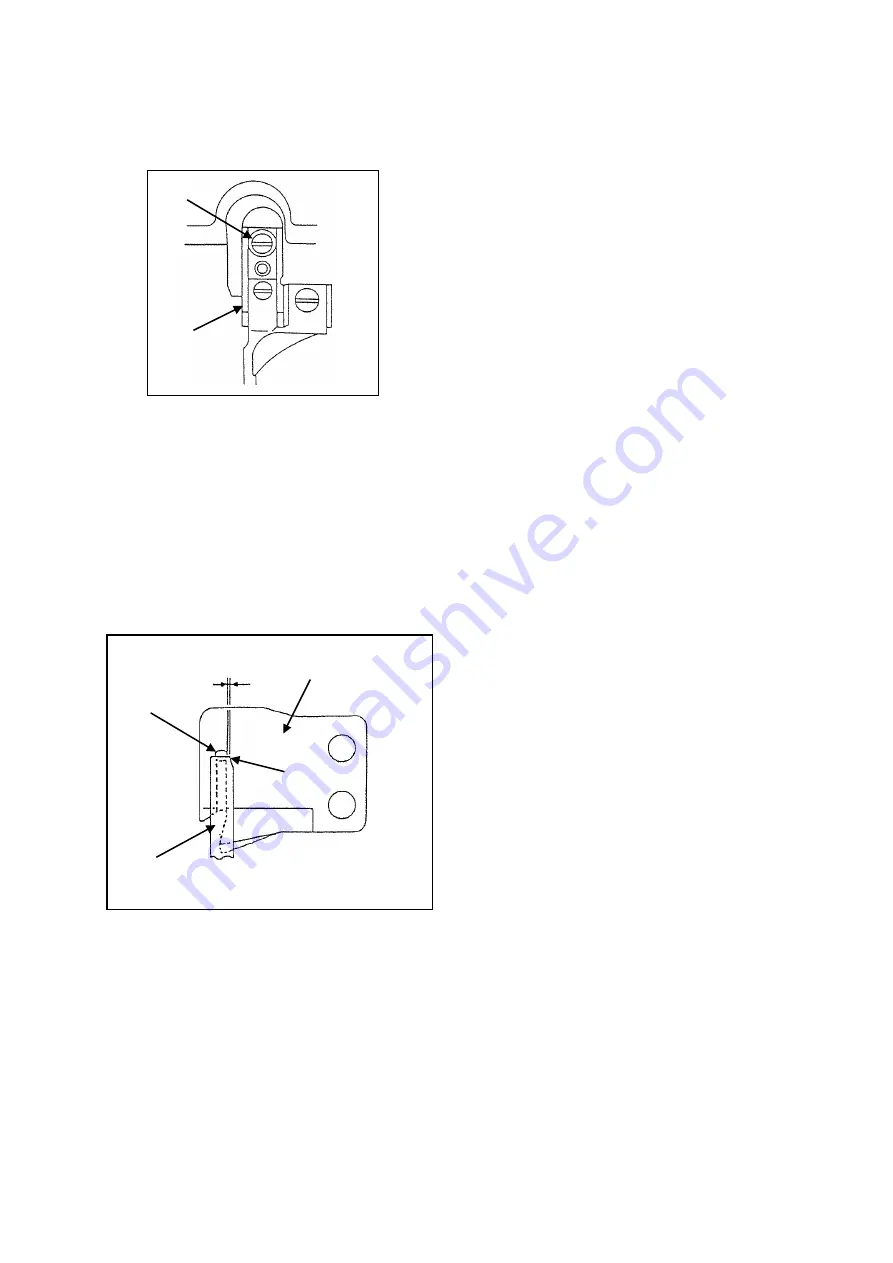
- 47 -
(2) Knife mounting unit
Under the condition that the rotating hook and the hook positioner are removed, attach the knife
mounting unit (No.1) with the set screw (No.2).
7-5-2.2 Mutual relation among the movable and stationary knife edge
(1) Rotate the movable knife (No.1) by hand when it is engaged with the stationary knife (No.2), there is
0.3mm space between the movable and stationary knife edges. This is standard condition.
(2) If this space is too wide, it causes a thread tail from the needle to be pulled out after the automatic
thread trimming. If it is too narrow, it causes the failure of the trimming. For avoiding these incidents,
adjust this space precisely.
(3) For this adjustment, suitably move the knife bracket or the knife mounting unit mentioned at above
7-5-2.1.
<1>: Movable knife
<2>: Stationary knife
<3>: Movable knife edge
<4>: Stationary knife edge
<1>: Knife mounting unit
<2>: Set screw
<1>
<2>
<1>
<2>
<3>
<4>
0.3mm
Содержание PLK-J2516R-YU
Страница 1: ...INDUSTRIAL SEWING MACHINE MODEL PLK J2516R YU TECHNICAL MANUAL SEWING MACHINE HEAD A180E803P02 ...
Страница 68: ......
Страница 70: ...Stand part 1 Thickness 2mm Stand part 2 Thickness 2mm ...
Страница 72: ...Printed in Japan ...