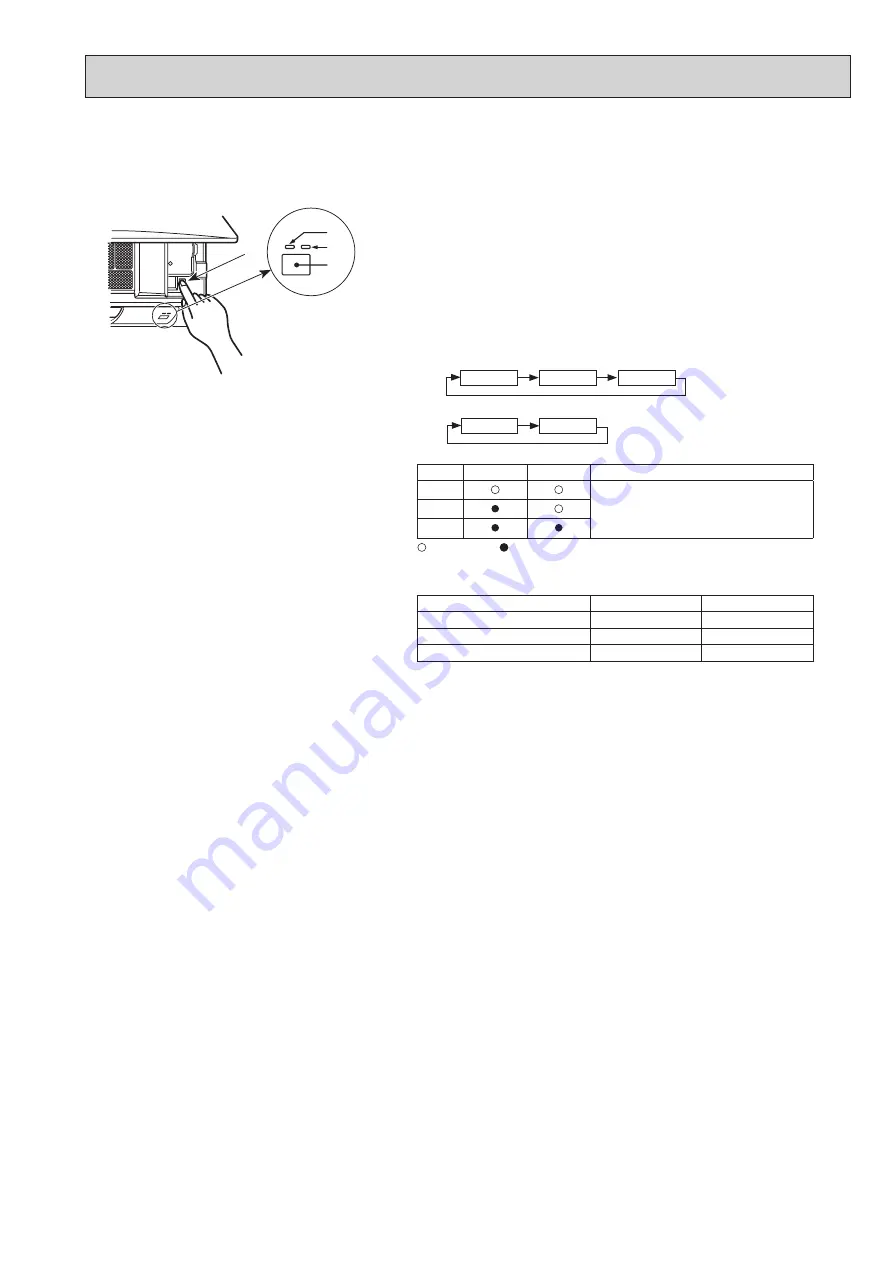
27
9-5. EMERGENCY OPERATION
9-5-1. When wireless remote controller troubles or its battery is exhausted
9-5-2. When wired remote controller or indoor unit microprocessor troubles
When the remote controller cannot be used
A
DEFROST/STAND BY lamp (ORANGE)
B
Operation lamp (GREEN)
C
Emergency operation switch (cooling/heating)
D
Receiver
[Heat pump type]
[Cooling Only type]
Operation Monitor Display
GREEN
ORANGE
STOP
COOL
HEAT
Turning off
Lighting
Details of emergency mode are as shown below.
Operation Mod
Set Temperature
Fan Speed
COOL
HEAT
24°C
24°C
High
High
Airflow Direction Up and Down
Horizontal
Cooling
Heating
Stop
Cooling
Stop
•
Each press of the emergency operation switch will toggle the operation mode.
•
Check “COOL/HEAT” with the operation monitor display. (The display will
appear orange for 5 seconds after pressing the emergency operation switch.)
Downward
When the batteries of the remote controller run out or the remote controller
malfunctions, the emergency operation can be done using the emergency
buttons.
The orange lamp follows the switch operation
as indicated at the left for 5 seconds, and
then it will return to the normal display.
B
A
D
C
1. When the wired remote control or the indoor unit microprocessor has failed, but all other components work properly,
if you set the switch (SWE) on the indoor controller board ON, the indoor unit will begin Emergency Operation.
When Emergency Operation is activated, the indoor unit operates as follows:
(1) Indoor fan is running at high speed. (2) Drain pump is operating.
Note on the wireless remote control:
When the remote control does not function, it is possible to activate Emergency Operation by using the indoor unit Emergency Operation switch.
However, if the indoor unit microcomputer has failed, it is necessary to proceed with points 2 and 3 below as in the
case of the wired remote control.
2. When you activate Emergency Operation of the cooling or heating, you have to set the switch (SWE) on the indoor
controller board and activate Emergency Operation of the outdoor unit.
For details on how to activate Emergency Operation of the outdoor unit, refer to the outdoor unit wiring diagram.
3. Before you activate Emergency Operation, check the following points:
(1) Emergency Operation cannot be activated when:
• the outdoor unit malfunctions. • the indoor fan malfunctions.
• it has detected the malfunction of drain pump during self-diagnosing.
(2) Emergency Operation becomes continuous only by switching the power source on/off.
ON/OFF on the remote control or temperature control, etc. does not function.
(3) Avoid operating for a long time when the outdoor unit begins defrosting while Emergency Operation of the heating
is activated, because it will start to blow cold air.
(4) Emergency cooling should be limited to 10 hours maximum (The indoor unit heat exchanger may freeze).
(5) After Emergency Operation has been deactivated, set the switches, etc. to their original positions.
(6) Movement of the vanes does not work in Emergency Operation, therefore you have to slowly set them manually
to the appropriate position.
OCH661