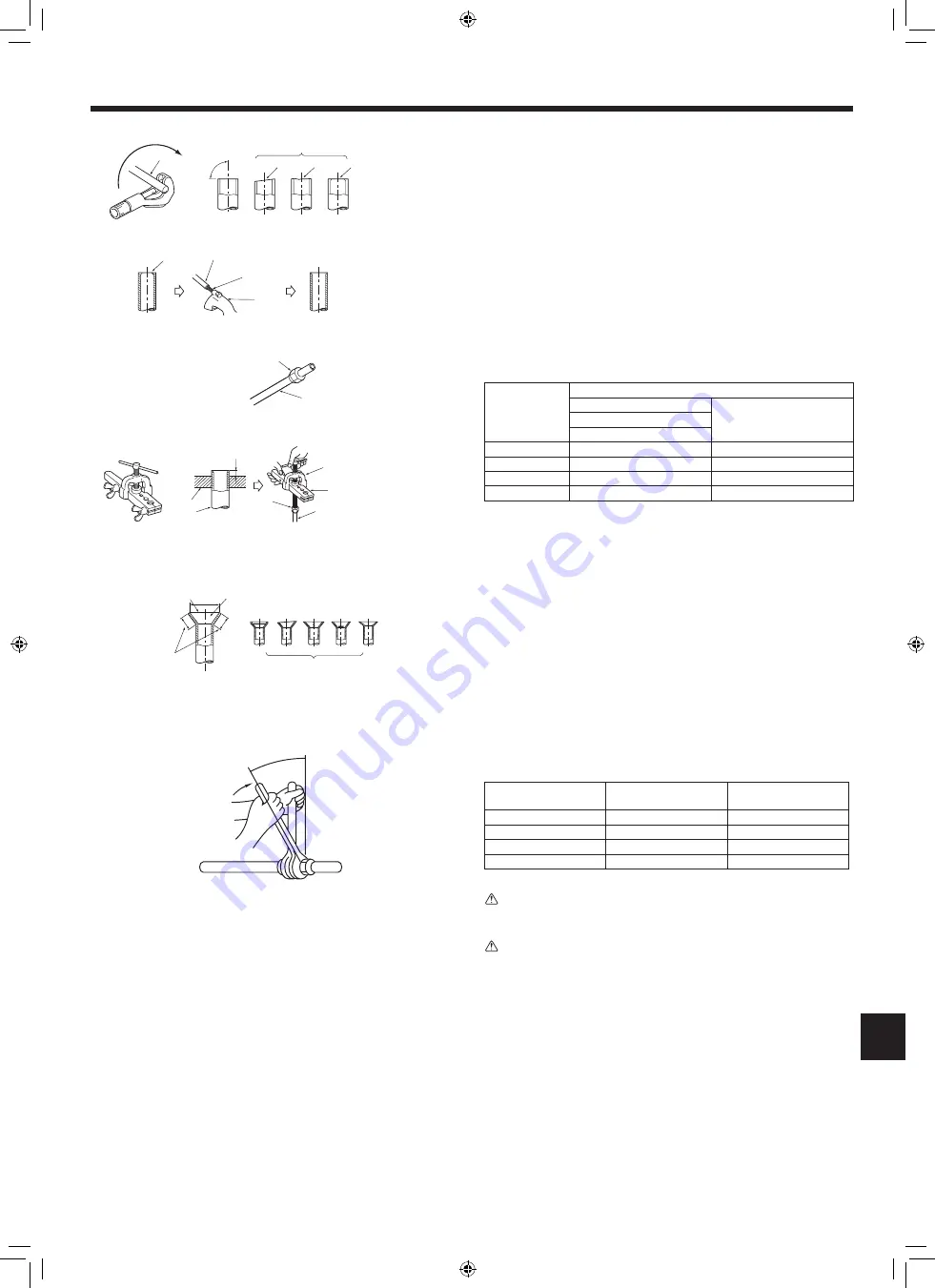
19
a
d
c
b
e
f
90°
d
c
b
a
b
a
a
b
e
b
c
d
c
A
Fig. 5-3
5. Refrigerant piping work
5.2.5. Check (Fig. 5-7)
• Compare the flared work with a figure in right side hand.
• If flare is noted to be defective, cut off the flared section and do flaring work again.
a
Smooth all around
f
Scratch on flared plane
b
Inside is shining without any scratches
g
Cracked
c
Even length all around
h
Uneven
d
Too much
i
Bad examples
e
Tilted
• Apply a thin coat of refrigeration oil on the seat surface of pipe. (Fig. 5-8)
• For connection first align the center, then tighten the first 3 to 4 turns of flare nut.
• Use tightening torque table below as a guideline for indoor unit side union joint
section, and tighten using two wrenches. Excessive tightening damages the flare
section.
Copper pipe O.D.
(mm)
Flare nut O.D.
(mm)
Tightening torque
(N·m)
ø6.35
17
14 - 18
ø9.52
22
34 - 42
ø12.7
26
49 - 61
ø15.88
29
68 - 82
Warning:
When installing the unit, securely connect the refrigerant pipes before starting
the compressor.
Warning:
Be careful of flying flare nut! (Internally pressurized)
Remove the flare nut as follows:
1. Loosen the nut until you hear a hissing noise.
2. Do not remove the nut until the gas has been completely released (i.e., hiss
-
ing noise stops).
3. Check that the gas has been completely released, and then remove the nut.
Fig. 5-7
Fig. 5-4
Fig. 5-5
Fig. 5-6
a
Copper tubes
b
Good
c
No good
d
Tilted
e
Uneven
f
Burred
a
Burr
b
Copper tube/pipe
c
Spare reamer
d
Pipe cutter
a
Flare nut
b
Copper tube
a
Flaring tool
b
Die
c
Copper tube
d
Flare nut
e
Yoke
Fig. 5-8
c
b
a
d
e
f
g
h
i
B
5.2. Flaring work
• Main cause of gas leakage is defect in flaring work.
Carry out correct flaring work in the following procedure.
5.2.1. Pipe cutting (Fig. 5-3)
• Using a pipe cutter cut the copper tube correctly.
5.2.2. Burrs removal (Fig. 5-4)
• Completely remove all burrs from the cut cross section of pipe/tube.
• Put the end of the copper tube/pipe to downward direction as you remove burrs in
order to avoid burrs drop in the tubing.
5.2.3. Putting nut on (Fig. 5-5)
• Remove flare nuts attached to indoor and outdoor unit, then put them on pipe/tube
having completed burr removal.
(not possible to put them on after flaring work)
5.2.4. Flaring work (Fig. 5-6)
• Carry out flaring work using flaring tool as shown at the right.
Pipe diameter
(mm)
Dimension
A (mm)
B
+0
(mm)
-0.4
When the tool for R32 is used
Clutch type
6.35
0 - 0.5
9.1
9.52
0 - 0.5
13.2
12.7
0 - 0.5
16.6
15.88
0 - 0.5
19.7
Firmly hold copper tube in a die in the dimension shown in the table at above.
VH79A008H01_En.indd 19
2018/10/05 10:12:11