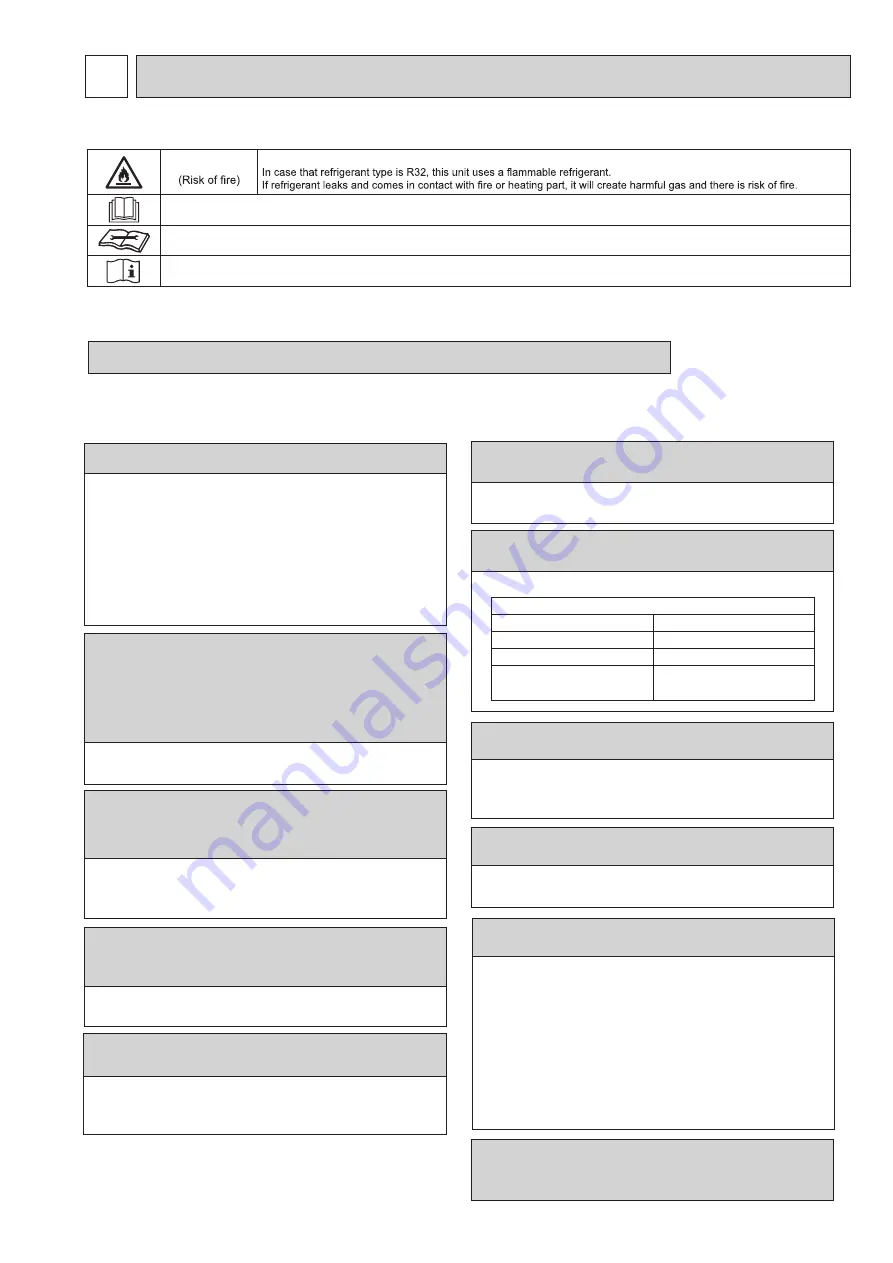
3
OCH522
SAFETY PRECAUTION
2
Cautions for units utilizing refrigerant R32/R410A
2-2. CAUTIONS RELATED TO NEW REFRIGERANT
2-1. ALWAYS OBSERVE FOR SAFETY
Before obtaining access to terminal, all supply circuits must be disconnected.
Use new refrigerant pipes.
Store the piping indoors, and keep both ends of
the piping sealed until just before brazing.
(Leave elbow joints, etc. in their packaging.)
In case of using the existing pipes for R22, be careful with
the following.
· Be sure to clean the pipes and make sure that the insides
of the pipes are clean.
· Change flare nut to the one provided with this product.
Use a newly flared pipe.
· Avoid using thin pipes.
· In case of reconnecting the refrigerant pipes after
detaching, make the flared part of pipe re-fabricated.
Charge refrigerant from liquid phase of gas
cylinder.
If the refrigerant is charged from gas phase, composition
change may occur in refrigerant and the efficiency will be
lowered.
Use a vacuum pump with a reverse flow check
valve.
Vacuum pump oil may flow back into refrigerant cycle and
that can cause deterioration of refrigerant oil, etc.
Use the following tools specifically designed for
use with R32/R410A refrigerant.
The following tools are necessary to use R32/R410A refrigerant.
Handle tools with care.
If dirt, dust or moisture enters into refrigerant cycle, that can
cause deterioration of refrigerant oil or malfunction of com-
pressor.
Do not use a charging cylinder.
If a charging cylinder is used, the composition of refrigera-
nt will change and the efficiency will be lowered.
Flare tool
Electronic refrigerant
charging scale
Vacuum pump adaptor
Size adjustment gauge
Gauge manifold
Torque wrench
Gas leak detector
Charge hose
Tools for R32/R410A
Contamination inside refrigerant piping can cause deterio-
ration of refrigerant oil, etc.
If dirt, dust or moisture enters into refrigerant cycle, that can
cause deterioration of refrigerant oil or malfunction of com-
pressor.
If large amount of mineral oil enters, that can cause deterio-
ration of refrigerant oil, etc.
Ventilate the room if refrigerant leaks during
operation. If refrigerant comes into contact with
a flame, poisonous gases will be released.
Make sure that the inside and outside of refrige-
rant piping is clean and it has no contaminants
such as sulfur, oxides, dirt, shaving particles, etc,
which are hazard to refrigerant cycle.
In addition, use pipes with specified thickness.
Never use any refrigerant other than that specified.
Doing so may cause a burst, an explosion, or fire when the
unit is being used, serviced, or disposed of.
Correct refrigerant is specified on name plate of outdoor
unit.
If other refrigerant (R22, etc.) is used, chlorine in refrige-
rant can cause deterioration of refrigerant oil, etc.
We will not be held responsible for mechanical failure,
system malfunction, unit breakdown or accidents caused
by failure to follow the instructions.
Use the specified refrigerant only.
The refrigerant oil applied to flare and flange
connections must be ester oil, ether oil or
alkylbenzene oil in a small amount.
MEANINGS OF SYMBOLS DISPLAYED ON THE UNIT
WARNING
This mark is for R32 refrigerant only. Refrigerant type is written on nameplate of outdoor unit.
Read the OPERATION MANUAL carefully before operation.
Service personnel are required to carefully read the OPERATION MANUAL and INSTALLATION MANUAL before operation.
Further information is available in the OPERATION MANUAL, INSTALLATION MANUAL, and the like.
Содержание MR. SLIM SLZ Series
Страница 39: ...39 OCH522 ...