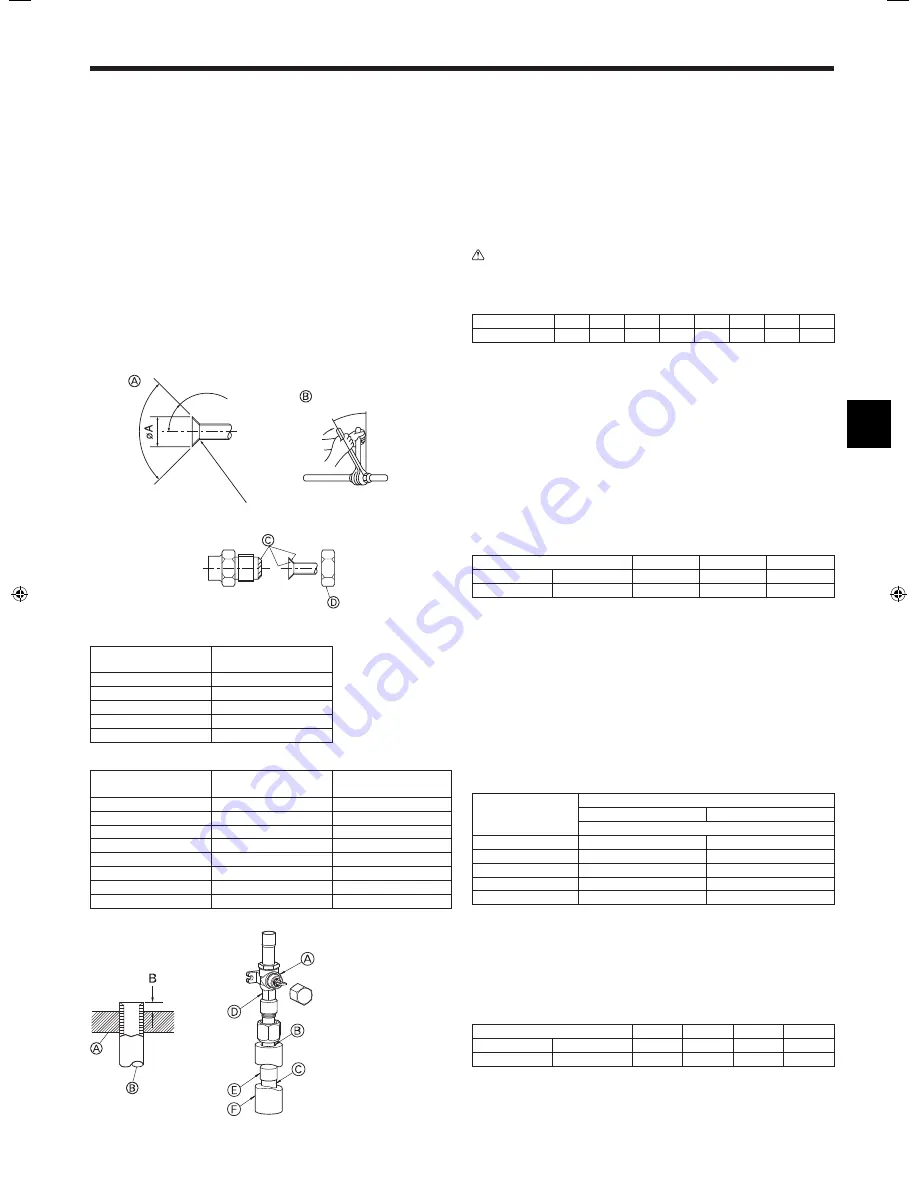
4. Installing the refrigerant piping
4.1. Precautions for devices that use R410A refrigerant
• Refer to page 3 for precautions not included below on using air condition-
ers with R410A refrigerant.
• Use ester oil, ether oil, alkylbenzene oil (small amount) as the refrigeration
oil applied to the flared sections.
• Use C1220 copper phosphorus, for copper and copper alloy seamless
pipes, to connect the refrigerant pipes. Use refrigerant pipes with the thick-
nesses specified in the table to the below. Make sure the insides of the
pipes are clean and do not contain any harmful contaminants such as sul-
furic compounds, oxidants, debris, or dust.
Always apply no-oxidation brazing when brazing the pipes, otherwise, the
compressor will the damaged.
Warning:
When installing or moving the air conditioner, use only the specified refriger-
ant (R410A) to charge the refrigerant lines. Do not mix it with any other re-
frigerant and do not allow air to remain in the lines. Air enclosed in the lines
can cause pressure peaks resulting in a rupture and other hazards.
Pipe size (mm)
ø6.35 ø9.52 ø12.7 ø15.88 ø19.05 ø22.2 ø25.4 ø28.58
Thickness (mm)
0.8
0.8
0.8
1.0
1.0
1.0
1.0
1.0
•
Do not use pipes thinner than those specified above.
4.2. Connecting pipes
• When commercially available copper pipes are used, wrap liquid and gas pipes
with commercially available insulation materials (heat-resistant to 100°C or more,
thickness of 12 mm or more).
• The indoor parts of the drain pipe should be wrapped with polyethylene foam
insulation materials (specific gravity of 0.03, thickness of 9 mm or more).
• Apply thin layer of refrigerant oil to pipe and joint seating surface before tighten-
ing flare nut.
A
(Fig. 4-1)
• Use two wrenches to tighten piping connections.
B
(Fig. 4-1)
• Use leak detector or soapy water to check for gas leaks after connections are
completed.
• Apply refrigerating machine oil over the entire flare seat surface.
C
(Fig. 4-1)
• Use the flare nuts for the following pipe size.
D
(Fig. 4-1)
RP50
RP60, 71
RP100-140
Gas side
Pipe size (mm)
ø12.7
ø15.88
ø15.88
Liquid side
Pipe size (mm)
ø6.35
ø9.52
ø9.52
• When bending the pipes, be careful not to break them. Bend radii of 100 mm to
150 mm are sufficient.
• Make sure the pipes do not contact the compressor. Abnormal noise or vibration
may result.
1
Pipes must be connected starting from the indoor unit.
Flare nuts must be tightened with a torque wrench.
2
Flare the liquid pipes and gas pipes and apply a thin layer of refrigeration oil
(Applied on site).
• When usual pipe sealing is used, refer to Table 1 for flaring of R410A refrigerant
pipes.
The size adjustment gauge can be used to confirm B measurements.
Table 1 (Fig. 4-2)
Copper pipe O.D.
(mm)
B (mm)
Flare tool for R410A
Flare tool for R22·R407C
Clutch type
ø6.35 (1/4")
0 - 0.5
1.0 - 1.5
ø9.52 (3/8")
0 - 0.5
1.0 - 1.5
ø12.7 (1/2")
0 - 0.5
1.0 - 1.5
ø15.88 (5/8")
0 - 0.5
1.0 - 1.5
ø19.05 (3/4")
0 - 0.5
1.0 - 1.5
3
Use the following procedure for connecting the gas-side piping. (Fig. 4-3)
1 Braze the
E
Joint pipe provided to the outdoor unit using locally procured braz-
ing materials and
C
Local piping without oxygen.
2 Connect the
E
Joint pipe to the gas-side Stop valve.
Use two wrenches to tighten the flare nut.
* If order is reversed, refrigerant leak occurs because of the part damaging by brazing fire.
• For PEA-RP200, 250, 400, 500GA
The method of pipe connection is brazing connection.
PEA-200 PEA-250 PEA-400 PEA-500
Gas side
Pipe size (mm)
ø25.4
ø25.4
ø25.4
ø25.4
Liquid side
Pipe size (mm)
ø9.52
ø12.7
ø9.52
ø12.7
A
(Fig. 4-1)
Copper pipe O.D.
(mm)
Flare dimensions
øA dimensions (mm)
ø6.35
8.7 - 9.1
ø9.52
12.8 - 13.2
ø12.7
16.2 - 16.6
ø15.88
19.3 - 19.7
ø19.05
23.6 - 24.0
B
(Fig. 4-1)
Copper pipe O.D.
(mm)
Flare nut O.D.
(mm)
Tightening torque
(N·m)
ø6.35
17
14 - 18
ø6.35
22
34 - 42
ø9.52
22
34 - 42
ø12.7
26
49 - 61
ø12.7
29
68 - 82
ø15.88
29
68 - 82
ø15.88
36
100 - 120
ø19.05
36
100 - 120
A
Flare cutting dimensions
B
Flare nut tightening torque
A
Die
B
Copper pipe
A
Stop valve (gas-side)
B
Seal section
C
Local piping
D
Double spanner section
E
Joint pipe
F
Pipe cover
Fig. 4-1
Fig. 4-2
Fig. 4-3
45° ± 2°
90°
±
0.5°
R0.4
~ R0.8
BH79D068H02_en.indd 5
8/24/2007 2:25:13 PM