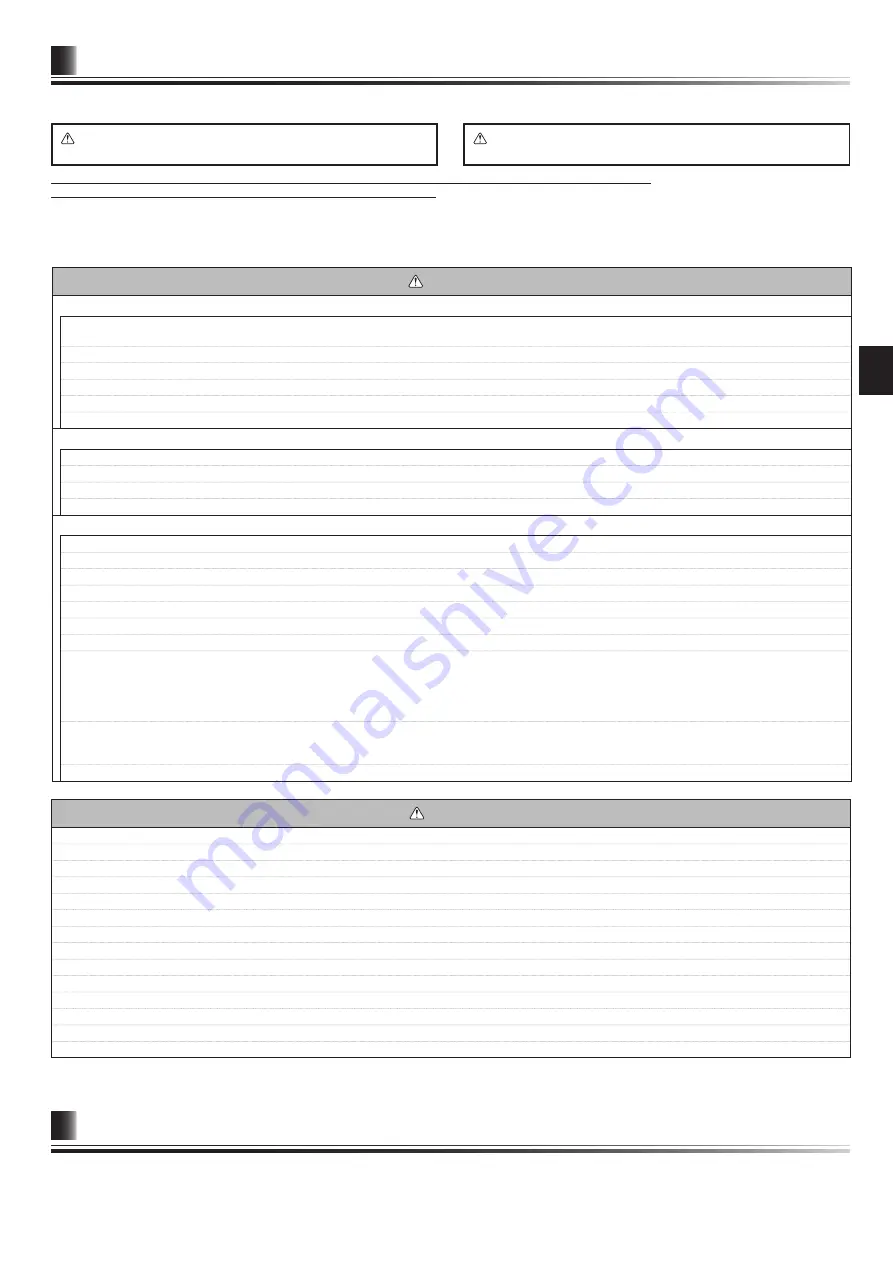
2
Safety Notices
1
en
WARNING
Mechanical
The hydrobox and outdoor units must not be installed, disassembled, relocated, altered or repaired by the user. Ask an authorised installer or technician. If the unit is
installed improperly or modified after installation by the user water leakage, electric shock or fire may result.
The outdoor unit should be securely fixed to a hard level surface capable of bearing its weight.
The hydrobox should be positioned on a hard vertical surface capable of supporting its filled weight to prevent excessive sound or vibration.
Do not position furniture or electrical appliances below the outdoor unit or hydrobox.
The discharge pipework from the emergency/safety devices of the hydrobox should be installed according to local law.
Only use accessories and replacement parts authorised by Mitsubishi Electric ask a qualified technician to fit the parts.
Electrical
All electrical work should be performed by a qualified technician according to local regulations and the instructions given in this manual.
The units must be powered by a dedicated power supply and the correct voltage and circuit breakers must be used.
Wiring should be in accordance with national wiring regulations. Connections must be made securely and without tension on the terminals.
Earth unit correctly.
General
Keep children and pets away from both the hydrobox and outdoor units.
Do not use the hot water produced by the heat pump directly for drinking or cooking. This could cause illness to the user.
Do not stand on the units.
Do not touch switches with wet hands.
Annual maintenance checks on both the hydrobox and the outdoor unit should be conducted by a qualified person.
Do not place containers with liquids on top of the hydrobox. If they leak or spill onto the hydrobox damage to the unit and/or fire could occur.
Do not place any heavy items on top of the hydrobox.
When installing, relocating, or servicing the hydrobox, use only the specified refrigerant (R410A) to charge the refrigerant lines. Do not mix it with any other refrigerant
and do not allow air to remain in the lines. If air is mixed with the refrigerant, then it can be the cause of abnormal high pressure in the refrigerant line, and may result
in an explosion and other hazards.
The use of any refrigerant other than that specified for the system will cause mechanical failure or system malfunction or unit breakdown. In the worst case, this could
lead to a serious impediment to securing product safety.
In heating mode, to avoid the heat emitters being damaged by excessively hot water, set the target flow temperature to a minimum of 2ºC below the maximum allow
-
able temperature of all the heat emitters. For Zone2, set the target flow temperature to a minimum of 5ºC below the maximum allowable flow temperature of all the
heat emitters in Zone2 circuit.
Do not install the unit where combustible gases may leak, be produced, flow, or accumulate. If combustible gas accumulates around the unit, fire or explosion may result.
CAUTION
Use clean water that meets local quality standards on the primary circuit.
The outdoor unit should be installed in an area with sufficient airflow according to the diagrams in the outdoor unit installation manual.
The hydrobox should be located inside to minimise heat loss.
Water pipe-runs on the primary circuit between outdoor and indoor unit should be kept to a minimum to reduce heat loss.
Ensure condensate from outdoor unit is piped away from the base to avoid puddles of water.
Remove as much air as possible from water circuit.
Refrigerant leakage may cause suffocation. Provide ventilation in accordance with EN378-1.
Be sure to wrap insulation around the piping. Direct contact with the bare piping may result in burns or frostbite.
Never put batteries in your mouth for any reason to avoid accidental ingestion.
Battery ingestion may cause choking and/or poisoning.
Install the unit on a rigid structure to prevent excessive sound or vibration during operation.
If power to the hydrobox is to be turned off (or system switched off) for a long time, the water should be drained.
Preventative measures should be taken against water hammer, such as installing a Water Hammer Arrestor on the primary water circuit, as directed by the manufacturer.
In order to prevent condensation on emitters, adjust flow temperature appropriately and also set the lower limit of the flow temperature on site.
As for the handling of refrigerant, refer to the outdoor unit installation manual.
Please read the following safety precautions carefully.
WARNING:
Precautions that must be observed to prevent injuries or death.
CAUTION:
Precautions that must be observed to prevent damage to unit.
This installation manual along with the user manual should be left with the product after installation for future reference.
Mitsubishi Electric is not responsible for the failure of locally-supplied parts.
• Be sure to perform periodical maintenance.
• Be sure to follow your local regulations.
• Be sure to follow the instructions provided in this manual.
The purpose of this installation manual is to instruct competent persons how to
safely and efficiently install and commission the hydrobox system. The target
readers of this manual are competent plumbers and/or refrigeration engineers
Introduction
2
who have attended and passed the requisite Mitsubishi Electric product training
and have appropriate qualifications for installation of an unvented hot water hy
-
drobox specific to their country.