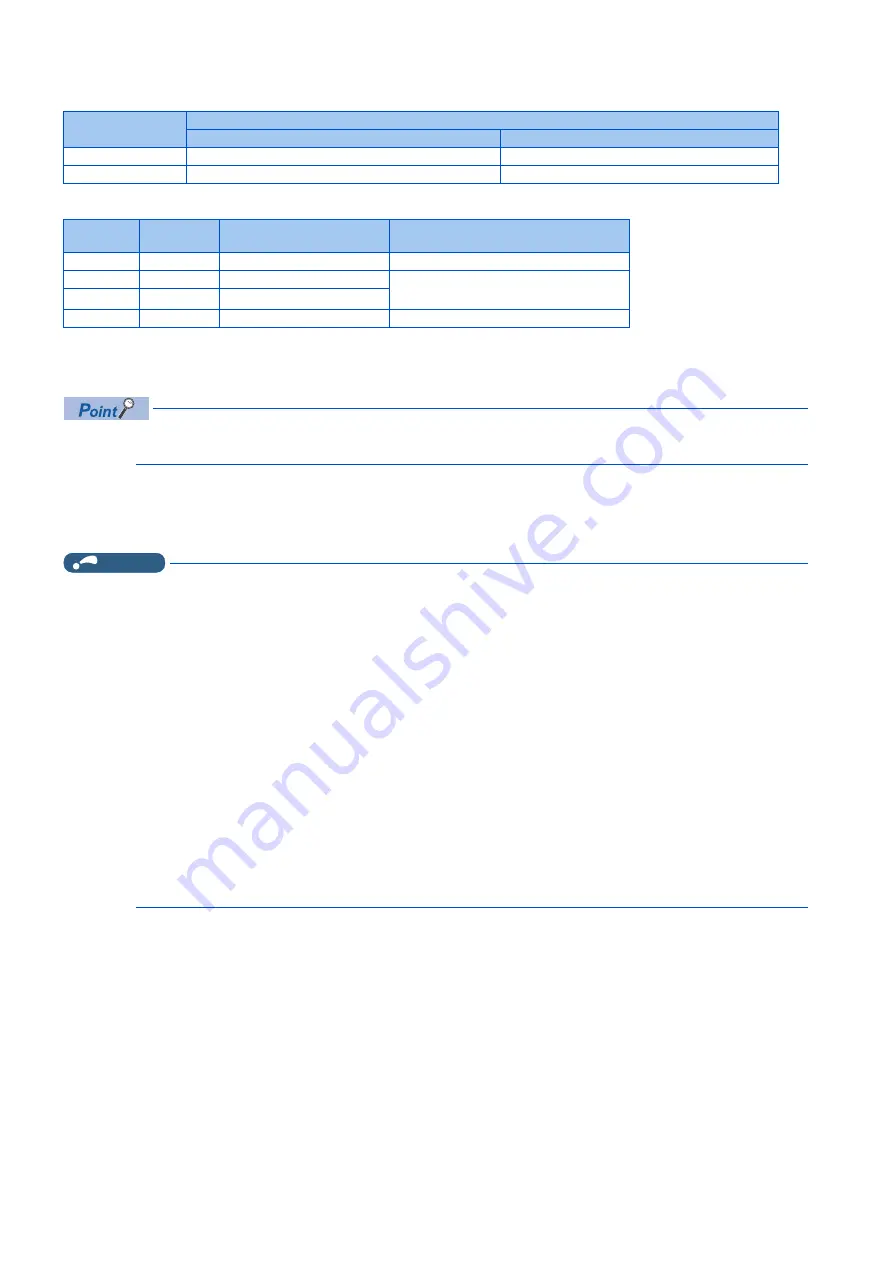
358
14. (C) Motor Constant Parameters
14.3 Offline auto tuning for a PM motor (motor constant tuning)
*1
Set
Pr.71 Applied motor
according to the motor to be used. According to the
Pr.71
setting, the range of the motor constant parameter setting
values and units can be changed. (For other setting values of
Pr.71
, refer to
• For tuning accuracy improvement, set the following parameters when the motor constants are known in advance.
*1
The setting is valid only when a value other than "9999" is set in both
Pr.707 (Pr.744)
and
Pr.724 (Pr.745)
.
Performing tuning
• Before performing tuning, check the monitor display of the operation panel if the inverter is in the state ready for tuning. The
motor starts by turning ON the start command while tuning is unavailable.
• In the PU operation mode, press the RUN key on the operation panel.
In the External operation, turn ON the start command (STF signal or STR signal). Tuning starts.
NOTE
• Satisfy the required inverter start conditions to start offline auto tuning. For example, stop the input of the MRS signal.
• To force tuning to end, use the MRS or RES signal or the STOP/RESET key on the operation panel. (Turning OFF the start
signal (STF signal or STR signal) also ends tuning.)
• During offline auto tuning, only the following I/O signals are valid (initial value).
Input terminals <effective signals>: MRS, RES, STF, STR, S1, and S2
Output terminals: RUN, FM, AM, ABC, and SO
• When the rotation speed and the output frequency are selected for terminals FM and AM, the progress status of offline auto
tuning is output in 15 steps from FM and AM (in the standard model).
• Do not perform ON/OFF switching of the Second function selection (RT) signal during offline auto tuning. Auto tuning will not
be performed properly.
• A motor with 14 or more poles cannot be tuned.
• Since the Inverter running (RUN) signal turns ON when tuning is started, pay close attention especially when a sequence which
releases a mechanical brake by the RUN signal has been designed.
• When executing offline auto tuning, input the operation command after switching ON the main circuit power (R/L1, S/L2, T/L3)
of the inverter.
• While
Pr.79 Operation mode selection
= "7", turn ON the PU operation external interlock (X12) signal for tuning in the PU
operation mode.
• Setting offline auto tuning (
Pr.96
= "1") will make pre-excitation invalid.
Motor
Pr.71 setting
Motor constant parameter
Ω
, mH, and A unit setting
Motor constant parameter internal data setting
IPM motor
8090
8093
SPM motor
9090
9093
First motor
Pr.
Second
motor Pr.
Name
Setting
702
743
Maximum motor frequency
Maximum motor frequency (Hz)
707
744
Motor inertia (integer)
Jm =
Pr.707
× 10^(
-Pr.724
) (kg·m
2
)
724
745
Motor inertia (exponent)
725
746
Motor protection current level
Maximum current level of the motor (%)
Содержание FR-E800
Страница 17: ...16 1 Introduction 1 3 Related manuals MEMO ...
Страница 51: ...50 2 Basic Operation 2 8 I O terminal function assignment MEMO ...
Страница 89: ...88 3 Parameters 3 4 Parameter list by function group number MEMO ...
Страница 135: ...134 5 Speed Control 5 9 Troubleshooting in the speed control MEMO ...
Страница 153: ...152 6 Torque Control 6 7 Troubleshooting in torque control MEMO ...
Страница 195: ...194 8 E Environment Setting Parameters 8 18 Current average value monitor signal MEMO ...
Страница 237: ...236 10 D Operation Command and Frequency Command 10 6 Operation by multi speed setting MEMO ...
Страница 339: ...338 13 T Multi Function Input Terminal Parameters 13 9 Start signal operation selection MEMO ...
Страница 455: ...454 16 G Control Parameters 16 13 Speed smoothing control MEMO ...
Страница 481: ...480 18 Appendix 18 4 Parameters functions and instruction codes under different control methods MEMO ...