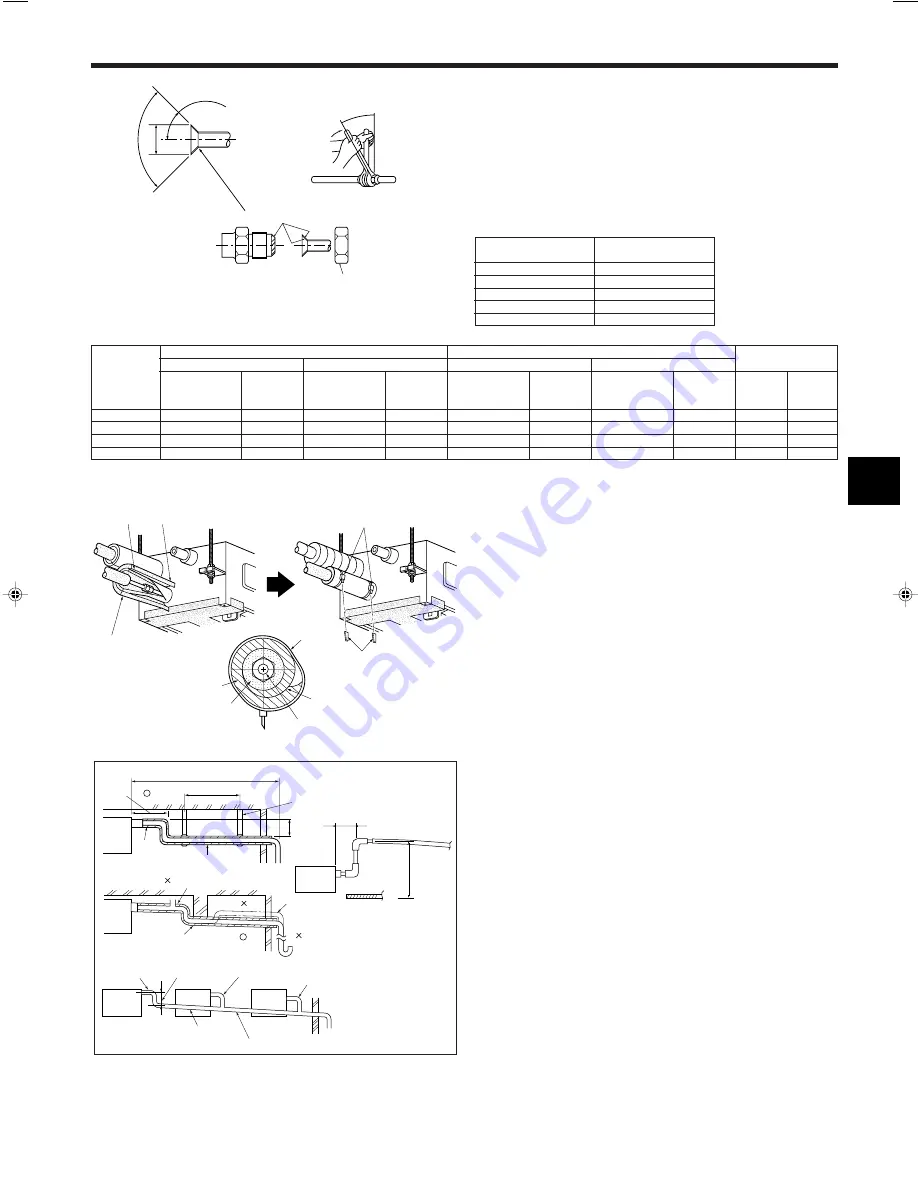
5
3. Refrigerant pipe and drain pipe
3.2. Connecting pipes (Fig. 3-2)
• When commercially available copper pipes are used, wrap liquid and gas pipes
with commercially available insulation materials (heat-resistant to 100 °C or more,
thickness of 12 mm or more).
• The indoor parts of the drain pipe should be wrapped with polyethylene foam insu-
lation materials (specific gravity of 0.03, thickness of 9 mm or more).
• Apply thin layer of refrigerant oil to pipe and joint seating surface before tightening
flare nut.
• Use two wrenches to tighten piping connections.
• Use refrigerant piping insulation provided to insulate indoor unit connections. Insu-
late carefully.
90
°
±
0.5
°
ø
A
R0.4~R0.8
A
45
°±
2
°
B
C
B
Fig. 3-2
Installing procedures (Fig. 3-3)
1. Remove the flare nuts and caps from the indoor unit.
2. Flare-cut the liquid and gas pipes then apply refrigerating machine oil (to be lo-
cally procured) over the flare-cut seat surface.
3. Quickly connect the refrigerant piping.
∗
Remember to tighten the flare nuts with a double spanner.
4. Slide the supplied pipe cover
3
over the gas piping until it is pressed against the
sheet metal inside the unit.
5. Slide the provided pipe cover
3
over the liquid piping until it is pressed against
the sheet metal inside the unit.
6. Tighten the pipe cover
3
at the both ends (15 - 20 mm) with the supplied bands
4
.
A
Gas piping
E
Turn the seam upward.
B
Liquid piping
F
Press the pipe cover against the sheet metal.
C
Band
4
G
Refrigerant piping heat insulating material
D
Pipe cover
3
H
Wrap tightly
I
Cut off excess length of band.
C
H
A
·
B
G
D
F
E
D
C
I
Fig. 3-3
3.3. Drainage piping work (Fig. 3-4)
• Use O. D. ø26 mm PVC TUBE for drain piping and provide 1/100 or more down-
ward slope.
• Be sure to connect the piping joints using adhesive of polyvinyl chloride family.
• Observe the figure for piping work.
• Use attached drain hose to change the pipe extraction direction.
1
Correct piping
2
Wrong piping
A
Insulation (9 mm or more)
B
Downward slope (1/100 or more)
C
Support metal
K
Air bleeder
L
Raised
M
Odor trap
N
Make as little as possible
O
Make as great as possible (approx. 10 cm)
Grouped piping
D
VP-20 (O. D. ø26 PVC TUBE)
E
Make it as large as possible
F
Indoor unit
G
Make the piping size large for grouped pip-
ing.
H
Downward slope (1/100 or more)
I
O. D. ø38 PVC TUBE for grouped piping.
(9 mm or more insulation)
J
Up to 50 cm
B
M
L
K
D
E
D
H
I
G
D
F
F
F
Max. 15cm
J
F
Fig. 3-4
Max. 20m
0.75–1.5m
N
O
A
B
C
A
Flare cutting dimensions
Copper pipe O.D.
Flare dimensions
(mm)
øA dimensions (mm)
ø6.35
8.7 - 9.1
ø9.52
12.8 - 13.2
ø12.7
16.2 - 16.6
ø15.88
19.3 - 19.7
ø19.05
22.9 - 23.3
C
Apply refrigerating machine oil over the entire flare seat surface.
B
Refrigerant pipe sizes & Flare nut tightening torque
* Use the provided flare nut for the following pipes: Liquid pipe of P50, P100 P125, and gas pipe of P50.
1
2
P20/25/32/40
P50
P63/80
P100/125
Flare nut O.D.
Liquid
Gas
pipe
pipe
(mm)
(mm)
17
26
22
29
22
29
22
36
R410A
Liquid pipe
Gas pipe
Tightening
Tightening
Pipe size
torque
Pipe size
torque
(mm)
(N.m)
(mm)
(N.m)
ODø6.35 (1/4”)
14 - 18
ODø12.7 (1/2”)
49 - 61
ODø6.35 (1/4”)
34 - 42
ODø12.7 (1/2”)
68 - 82
ODø9.52 (3/8”)
34 - 42
ODø15.88 (5/8”)
68 - 82
ODø9.52 (3/8”)
34 - 42
ODø15.88 (5/8”)
100 - 120
R407C or R22
Liquid pipe
Gas pipe
Tightening
Tightening
Pipe size
torque
Pipe size
torque
(mm)
(N.m)
(mm)
(N.m)
ODø6.35 (1/4”)
14 - 18
ODø12.7 (1/2”)
49 - 61
ODø9.52 (3/8”)
34 - 42*
ODø15.88 (5/8”)
68 - 82*
ODø9.52 (3/8”)
34 - 42
ODø15.88 (5/8”)
68 - 82
ODø9.52 (3/8”)
34 - 42
ODø19.05 (3/4”)
100 - 120*