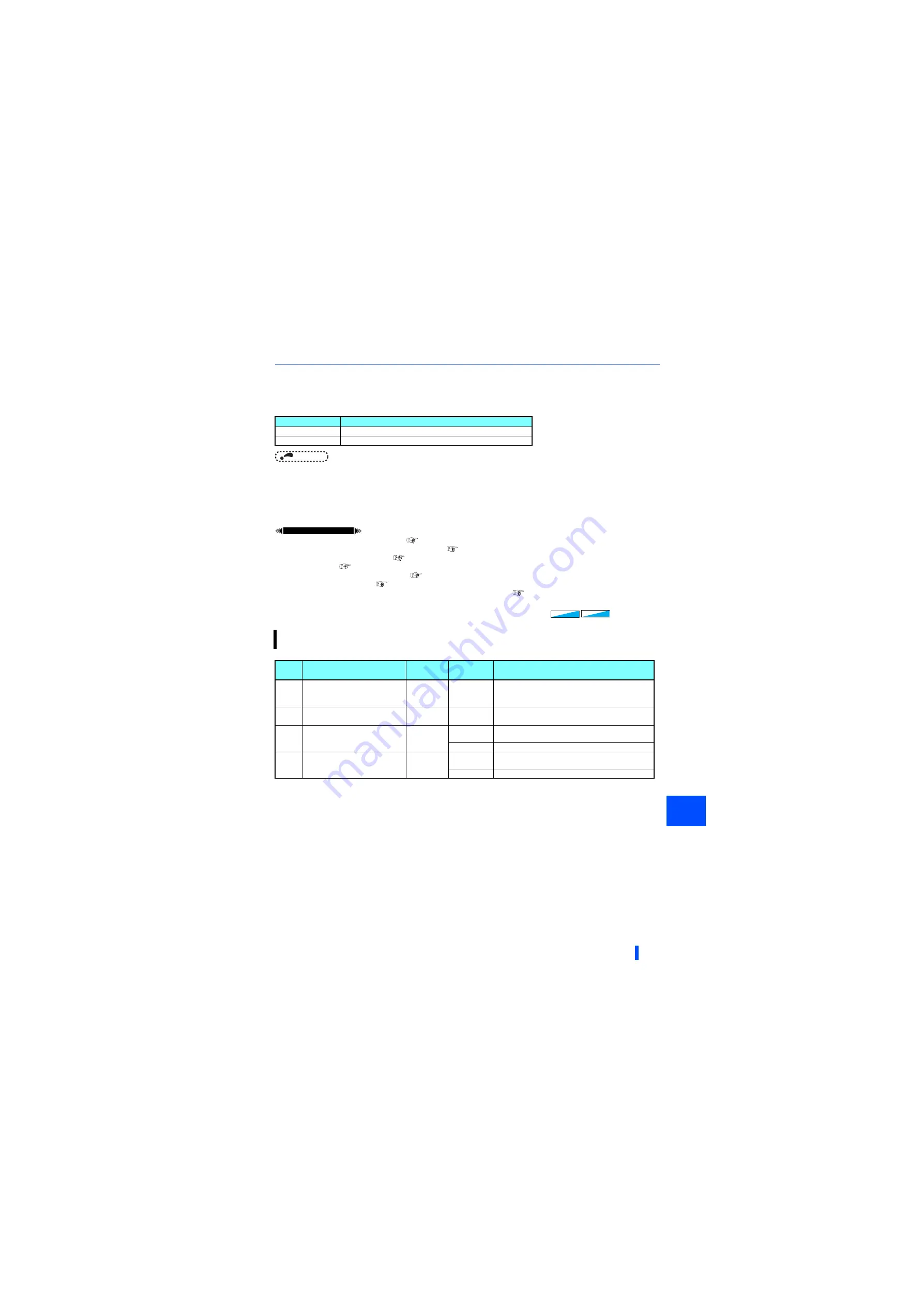
Torque control under Real sensorless vector control and vector control
201
5
Speed limit mode switching by external terminals (Pr.1113="10")
• The speed limit mode can be switch between 3 and 4 using the torque control selection (X93) signal.
• To assign the X93 signal, set "93" in any of
Pr.178 to Pr.189 (Input terminal function selection)
.
NOTE
• During the speed limit operation, SL is displayed on the operation panel and OL signal is output.
• OL signal is assigned to the terminal OL in the initial status. Set "3" in any of
Pr.190 to Pr.196 (Output terminal function
selection)
to assign the OL signal to another terminal. Changing the terminal assignment using
Pr.190 to Pr.196
may affect
the other functions. Set parameters after confirming the function of each terminal.
• Changing the terminal assignment using
Pr.178 to Pr.189 (Input terminal function selection)
may affect the other
functions. Set parameters after confirming the function of each terminal.
???????
Parameters referred to
Pr.1 Maximum frequency, Pr.2 Minimum frequency
Pr.4 to Pr.6, Pr.24 to Pr.27, Pr.232 to Pr.239 (Multi-speed operation)
Pr.7 Acceleration time, Pr.8 Deceleration time
Pr.13 Starting frequency
Pr.190 to Pr.196 (Output terminal function selection)
Pr.868 Terminal 1 function assignment
Pr.125, Pr.126, Pr.902 to Pr.905, Pr.917, Pr.918 (frequency setting voltage (current) bias gain)
5.4.6
Torque control gain adjustment
Current loop proportional (P) gain adjustment (Pr.824)
• The 100% current loop proportional gain is equivalent to 1000 rad/s during Real sensorless vector control, and to 1400 rad/
s during vector control.
• For ordinary adjustment, try to set within the range of 50 to 500%.
• Set the proportional gain for during speed control.
• If setting value is large, changes in current command can be followed well and current fluctuation relative to external
disturbance is smaller. If the setting value is however too large, it becomes unstable and high frequency torque pulse is
produced.
Current control integral time adjustment (Pr.825)
• Set the integral time of current control during torque control.
• Torque response increases if set small; current however becomes unstable if set too small.
• If the setting value is small, it produces current fluctuation toward disturbance, decreasing time until it returns to original
current value.
X93 signal
Speed limit mode
OFF
Mode 3 (torque command=positive,
Pr.1113
=1 or equivalent)
ON
Mode 4 (torque command=negative,
Pr.1113
=2 or equivalent)
Operation is normally stable enough in the initial setting, but some adjustments can be made if abnormal vibration,
noise or overcurrent occur for the motor or machinery.
Pr.
Name
Initial
value
Setting
range
Description
824
G213
Torque control P gain 1
(current loop proportional
gain)
100%
0 to 500%
Sets the current loop proportional gain.
825
G214
Torque control integral time 1
(current loop integral time)
5 ms
0 to 500 ms
Sets current loop integral compensation time.
834
G313
Torque control P gain 2
9999
0 to 500%
Sets the current loop proportional gain when RT signal is
ON.
9999
The
Pr.824
setting is applied to the operation.
835
G314
Torque control integral time 2
9999
0 to 500 ms
Sets the current loop integral compensation time when
RT signal is ON.
9999
The
Pr.825
setting is applied to the operation.
Sensorless
Sensorless
Sensorless
Sensorless
Sensorless
Sensorless
Sensorless
Sensorless
Sensorless Vector
Vector
Vector
Содержание 800 Series
Страница 11: ...MEMO 10 ...
Страница 17: ...MEMO 16 ...
Страница 95: ...MEMO 94 ...
Страница 671: ...MEMO 670 ...
Страница 681: ...MEMO 680 ...