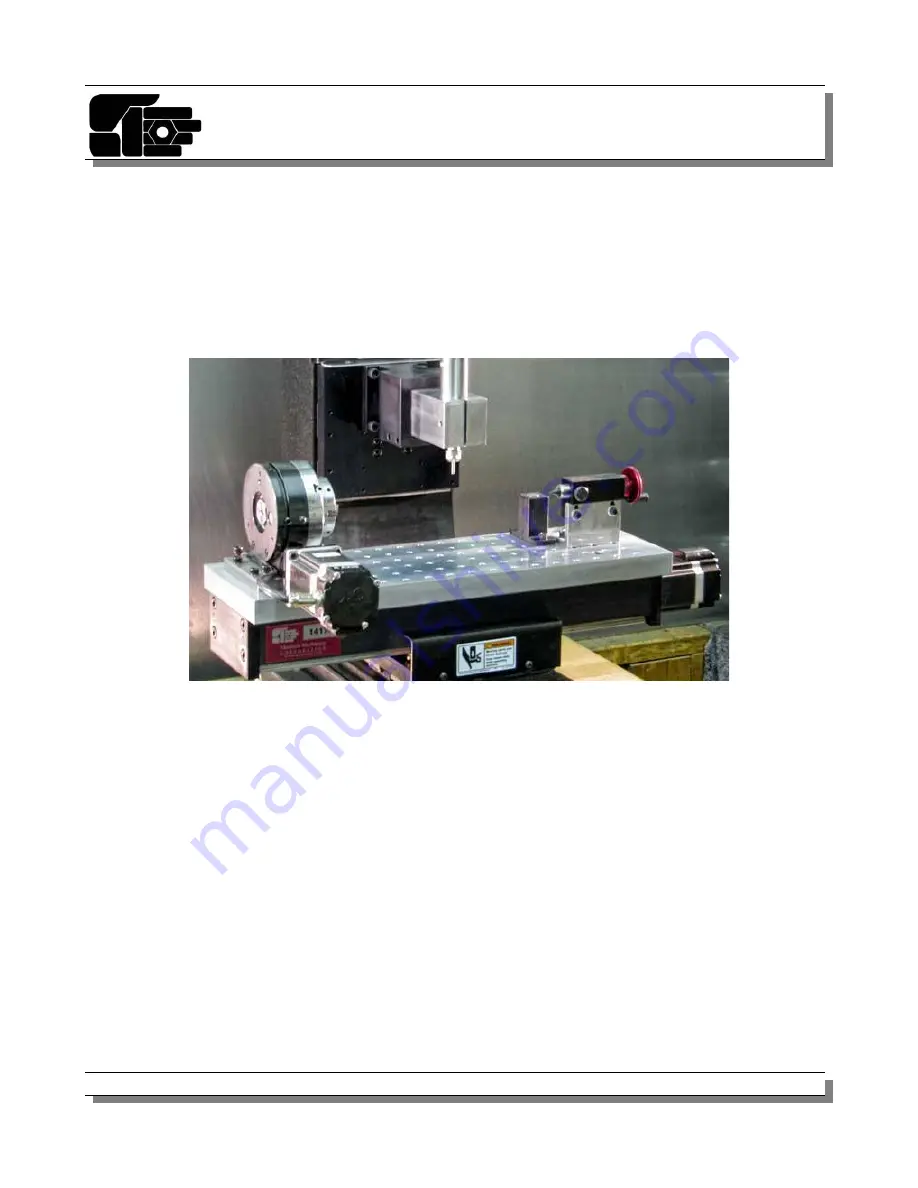
MINITECH
CNC Mini-Mill User's Guide
Rotary Table and Tailstock
The rotary table and chuck are the 4th axis of the machine referred to as the A-axis. This part
is used for cutting round objects or indexing. There are three alignments to be made to the
4th axis. It is normally mounted vertically on the left or right of the table parallel to the x axis.
There are other orientations of the A axis which are useful, but the setup process for other
configurations is similar and should be obvious if you can make it through this one.
Run Out
The properties of concern are the concentricity of the rotary table and chuck, and the
parallelness to the X axis. Setup the rotary table, chuck, and indicator with a straight round
bar as shown in figure 20. To measure concentricity of the rotary setup make sure the round
bar is properly fixed in the chuck. Rotate the A-axis 360 degrees, and note the change on the
dial test indicator at the chuck and about an inch away from the chuck. The run out on the
pictured setup was about 0.002” at about two inches out. If your run out is larger than you
required part tolerances contact the manufacturer and this can possibly be adjusted.
© 2012 Minitech Machinery Corp. 25
Rotary Table and Tailstock
Содержание Mini-Mill Series
Страница 24: ...MINITECH CNC Mini Mill User s Guide 2012 Minitech Machinery Corp 24 Figure 15 Figure 16 Figure 17 ...
Страница 33: ...MINITECH CNC Mini Mill User s Guide Drawings of the Machine Components 2012 Minitech Machinery Corp 33 ...
Страница 34: ...MINITECH CNC Mini Mill User s Guide Drawings of the Machine Components 2012 Minitech Machinery Corp 34 ...