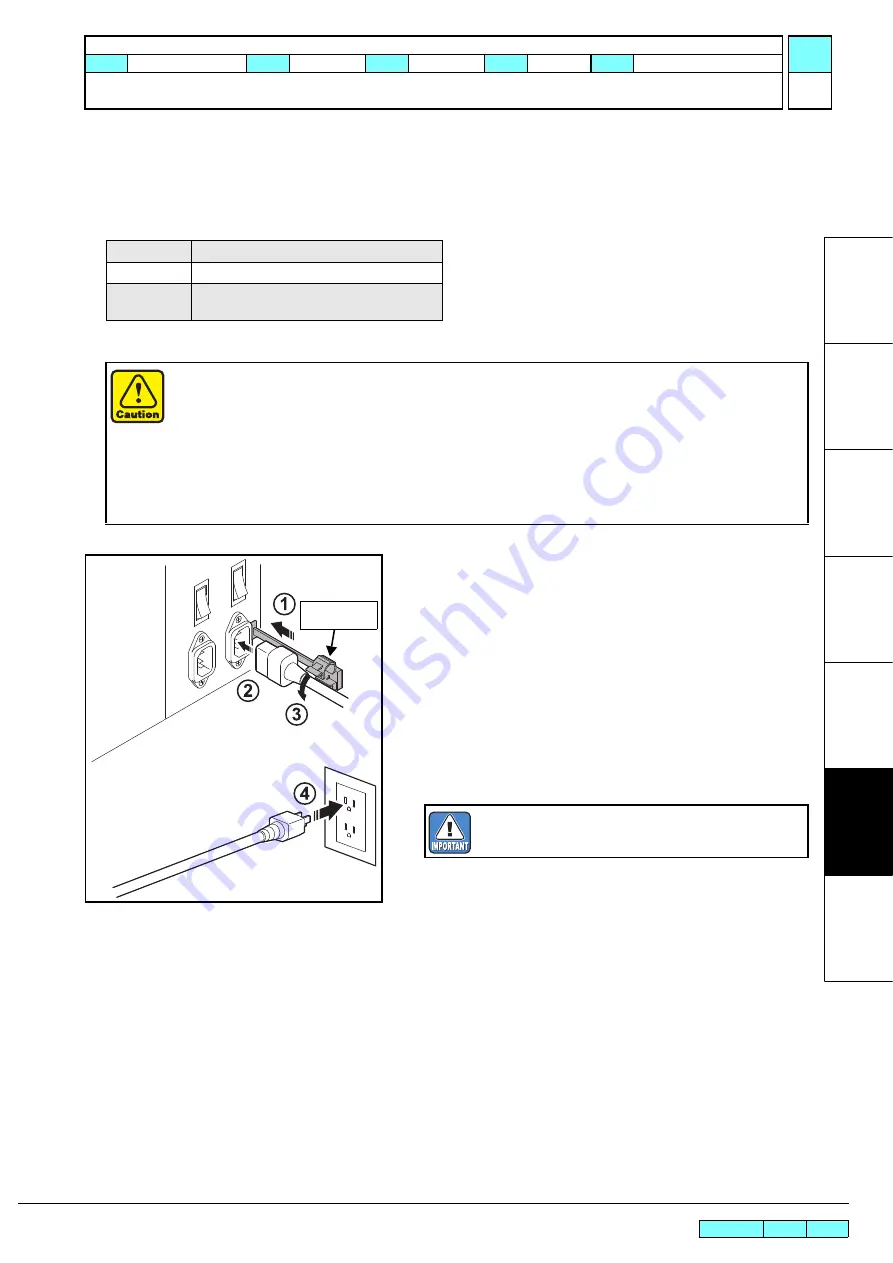
© 2014 MIMAKI ENGINEERING CO.,LTD.
6.2
P.3
R.1.1
INSTALLATION GUIDE > Power Supply Related > Connecting the Power Cable
Model
JV400-130/160LX
Issued
2011.02.15 Revised 2013.01.20 F/W ver.
Remark
1.1
6.2 Connecting the Power Cable
Outline
This device connects to the included two power cables.
If you do not use the included power cables, use cable that match your region.
Connect the power cables into a power outlet with the following specifications.
1. Insert the
power cable clamp
into the power supply box.
2. Insert the
power cable
into the inlet of this device.
3. Lock the power cable.
Run the power cable through the clamp, and lock the clamp
until it clicks.
4. Insert the
power plug
into a plug socket.
Voltage
AC100 to 120V, AC220 to 240V
Frequency
50/60Hz ± 1Hz
Capacity
15A or more (AC100 to 120V ± 10%) x 2 lines
10A or more (AC220 to 240V ± 10%) x 2 lines
Always connect the cables to a power outlet near the device so that the cables can be easily removed.
When plugging the cables into the power outlets, connect the cable into outlets on a separate circuit
from other devices. Because of the large power consumption, the power supply breaker may be
tripped.
Power supply cables should be connected to an earthed outlet. Otherwise, there is a risk of electrical
shock or of damaging the device.
When connecting the power cables, ensure that the power switch of the device is off.
Always connect the same voltage power supply to the inlet1 and inlet2.
Power cable
clamp
Insert into the socket of separate power line, respec-
tively.
Содержание JV400-130LX
Страница 49: ......
Страница 50: ...D500698 22 30042014 2013 MIMAKI ENGINEERING CO LTD KF FW 2 50...