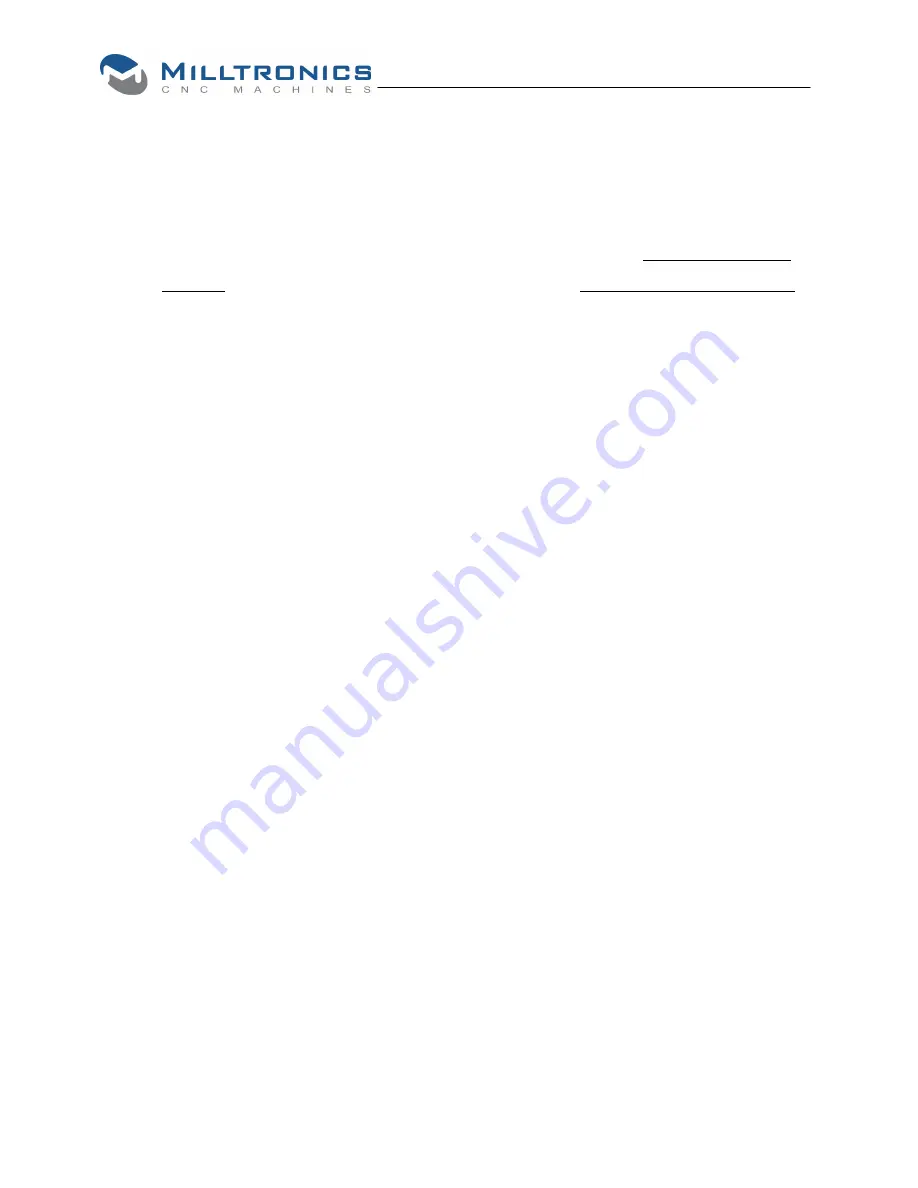
31
Chapter 5 - Failure Modes, Detection and Prevention
Minimizing Wear and Tear
•
The effects of everyday wear and tear may be minimized by good maintenance
practice. Items high on the maintenance list include keeping the machine clean,
providing clean dry compressed air with the correct oil drip into the air stream,
and continuous application of the correct way oil through the automatic oiler.
•
Machine failure is most likely to be caused by everyday wear and tear.
•
The effects of everyday wear and tear may be minimized by good installation
practice, including a flat and stable foundation and clean input power at the
correct voltage with a good ground.
•
Please refer to Chapter 4 of this manual for installation guidelines.
•
Please refer to Chapter 6 of this manual for a periodic maintenance checklist.
Clearing Faults in Electrical Components
•
A wide variety of failure modes caused by electrical component faults are
possible for the machine. An accidental crash between tool and workpiece, even
if it does not do mechanical damage, will likely cause an axis drive fault, putting
the machine into emergency stop mode. Even without a crash, a drive fault
might be caused by machining conditions, where the machine is asked to deliver
more than its rated power for a prolonged period. The machine can operate
outside its ratings for a short period, but eventually under these conditions a drive
will overload. In these and other failure modes caused by electrical components,
cycling power is the best way to clear the fault.
•
Press the red EMERGENCY STOP button to de-energize the drives (if the
machine is not already in emergency stop mode), then turn off power to the
machine using the main switch on the door of the electrical cabinet at the rear of
the machine. Wait a minute. Turn the power to the machine back on. Wait for
the CNC software to boot up. Enable and home the machine.
•
When an electrical component needs to be replaced, follow the guidelines in this
manual describing safe maintenance practice.