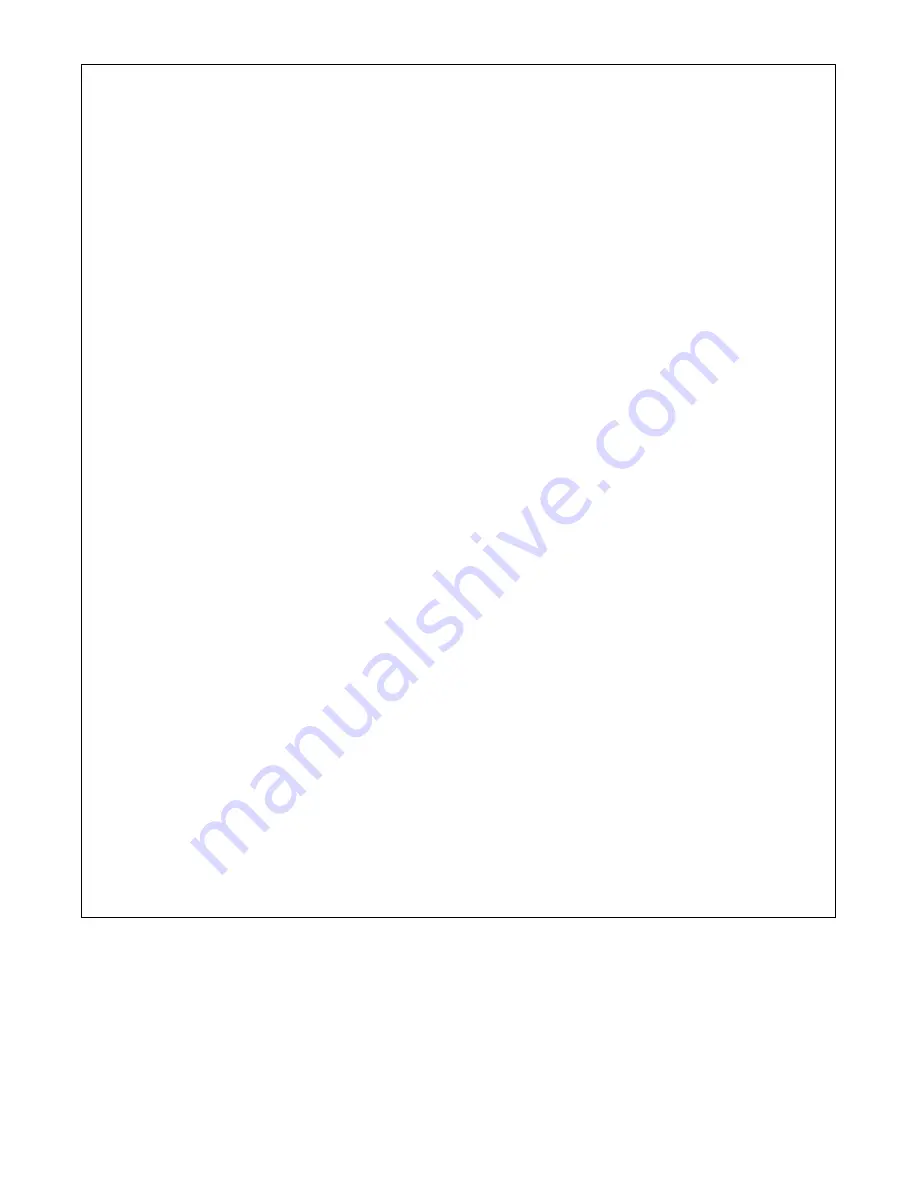
TM-257 220 Page 36
XMT 450 CC/CV
Theory Of Operation Components
1
Primary Input Power
Three-phase AC primary power
2
Filter Board PC7
Provides EMI filtering.
3
Input Contactor W1
Connects three−phase line power to input
rectifier SR1 upon completion of the
pre-charge cycle.
4
Power Switch S1
Used to pre-charge DC bus capacitors C3,
C4, C5, and C6 on power up. Provides con-
nection to control transformer T2.
5
Interconnect Printed Circuit Board
PC2
Provides electrical connections for SR1,
PM1, PM2, C3, C4, C5, C6, L1, L3, and L4.
Contains pre-charge and bus discharge res-
istors along with snubber components for
the IGBT modules.
6
Input Inductor L1
Limits RMS current in bus capacitors C3,
C4, C5, and C6 and input rectifier SR1.
7
Input capacitors C3, C4, C5, and C6.
Stores energy and filters the DC bus for in-
verter switching circuits.
8
DI/DT Inductor L3
Limits the reverse recovery current in
anti-parallel diodes within IGBT module
PM1.
9
DI/DT Inductor L4
Limits the reverse recovery current in
anti-parallel diodes within IGBT module
PM2.
10 Input Rectifier SR1
Converts three-phase AC power to full wave
rectified DC power.
11 IGBT Module PM1
Converts the DC buss into high frequency
AC power.
12 IGBT Gate Printed Circuit Board PC4
Circuit board is soldered to IGBT module
PM1 to provide interconnection of gate
pulses from inverter control board PC1.
13 IGBT Module PM2
Converts the DC buss into high frequency
AC power.
14 IGBT Gate Printed Circuit Board PC5
Circuit board is soldered to IGBT module
PM2 to provide interconnection of gate
pulses from inverter control board PC1.
15 Current Transformer CT1
Provides primary current feedback to invert-
er control board PC1 from main transformer
T1 primary to control circuit timing.
16 Control Transformer T2
Supplies unit with all required AC control
power.
17 Supplementary Protector CB1
Provides overload protection for 115 VAC
receptacle RC2.
18 115 VAC Receptacle RC2
Supplies power for optional cooler.
19 Inverter Control Board PC1
•
Receives reference command signal from
operator interface board PC3
•
Provides gating signals to IGBT modules
PM1 and PM2
•
Receives primary current feedback signal
from current transformer CT1
•
Receives DC bus voltage feedback from
interconnect board PC2
•
Receives weld current feedback signal
from current transformer HD1
•
Supplies control power to operator inter-
face board PC3
•
Energizes input contactor W1 upon com-
pletion of pre-charge cycle
•
Provides interface between primary and
secondary heatsink thermistors and in-
verter control board PC3
20 Supplementary Protector CB2
Provides overload protection for 24 VAC
wire feeder supply.
21 Optional Gas Solenoid GS1
Provides on/off flow of shielding gas to TIG
torch.
22 Fan Motor FM1
Provides cooling of heat generating com-
ponents within the wind-tunnel.
23 Fan Motor FM2
Provides internal cooling of components.
24 Secondary Heatsink Thermistor RT1
Provides thermal monitoring of secondary
heatsink.
25 Primary Heatsink Thermistor RT2
Provides thermal monitoring of primary
heatsink.
26 Operator Interface Board PC3
•
Provides user control of necessary weld
functions as well as general control of the
power source
•
Provides reference command signal to in-
verter control board PC1
•
Contains weld control process
•
Receives weld voltage feedback signal
from weld output terminals
•
Monitors heatsink temperatures
27 Remote 14-Pin Receptacle RC50
Provides connection for accessory equip-
ment.
28 Voltmeter
Displays preset voltage or actual voltage
while welding.
29 Arc Control
Provides adjustment of weld characteristics.
Allows for control of DIG in Stick process, or
inductance in MIG process.
30 Ammeter
Displays preset amperage or actual weld
current while welding.
31 Voltage/Amperage Adjust Control
Sets desired welding voltage or amperage
depending on selected process.
32 Process Selector Control
Selects desired welding process.
33 Weld Process Control
Controls weld output by adjusting command
signal to inverter control board PC1 by com-
paring the weld preset level to welding
voltage and/or current.
34 Tank Capacitors C1, C2
Creates a series resonant tank circuit along
with main transformer T1 and DIDT induct-
ors L3 and L4.
35 Main Transformer T1
T1 is energized by the on/off switching ac-
tion of IGBT modules PM1 and PM2. Con-
verts high voltage/low current primary power
into low voltage/high current weld power.
Creates resonant tank circuit along with tank
capacitors C1 and C2.
36 Output Diodes D1, D2, D3, D4
Rectifies the output of main transformer T1
to provide DC weld output.
37 Stabilizer Z1
Limits output ripple current to produce a
smooth welding arc.
38 Current Transducer HD1
Provides weld current feedback to inverter
control board PC1.
39 Negative Weld Output Terminal
Provides weld output connection to the elec-
trode of the weld circuit.
40 Positive Weld Output Terminal
Provides weld output connection to the
workpiece of the weld circuit.
Содержание XMT 450 CC
Страница 4: ......
Страница 55: ...Always check unit before applying power see Section 10 1 TM 257 220 Page 51 XMT 450 CC CV Notes...
Страница 59: ...Always check unit before applying power see Section 10 1 TM 257 220 Page 55 XMT 450 CC CV Notes...
Страница 68: ...TM 257 220 Page 64 XMT 450 CC CV Notes...
Страница 71: ...TM 257 220 Page 67 XMT 450 CC CV 256 909 A...
Страница 73: ...TM 257 220 Page 69 XMT 450 CC CV 256 916 C...
Страница 75: ...TM 257 220 Page 71 XMT 450 CC CV 256 916 C...
Страница 76: ...TM 257 220 Page 72 XMT 450 CC CV Notes...
Страница 83: ...Notes...