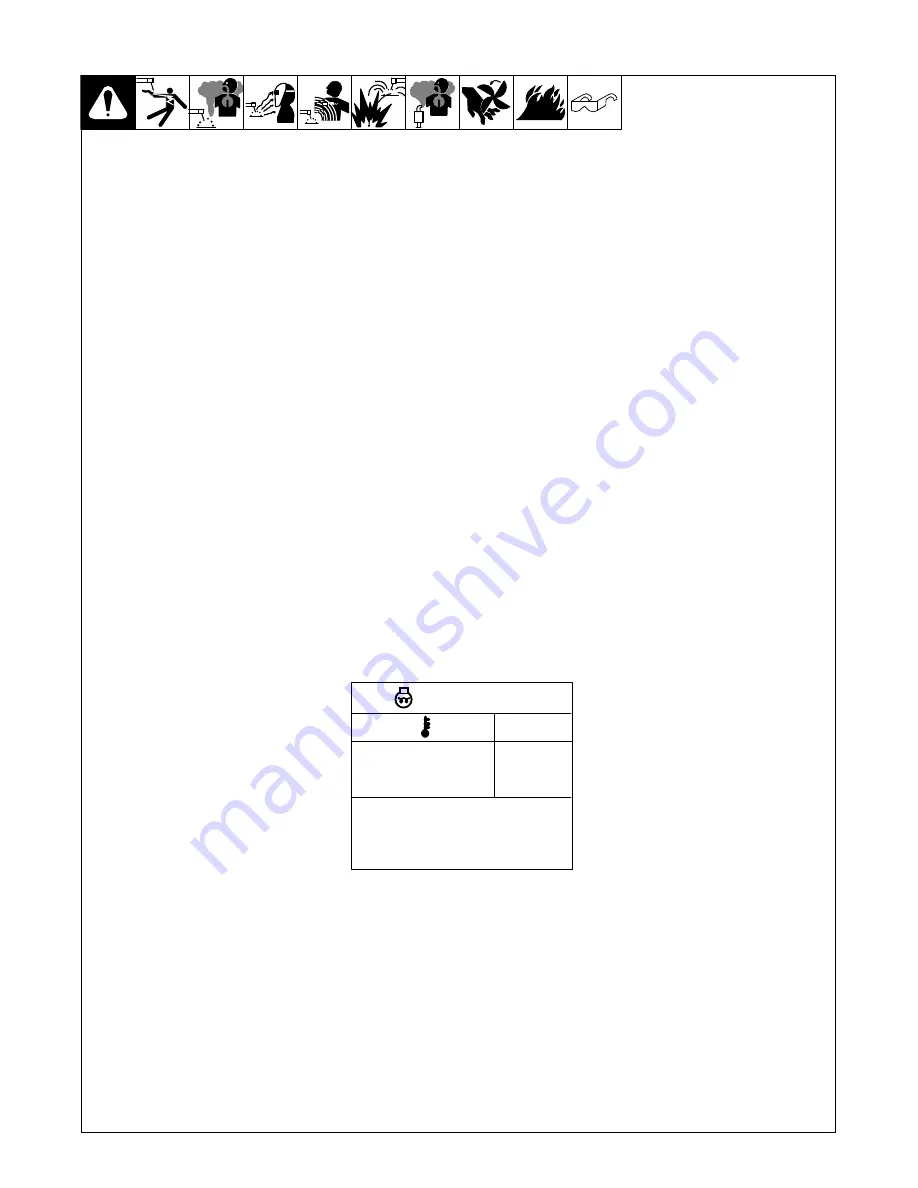
Complete Parts List available at www.MillerWelds.com
OM-258900 Page 31
6-2. Description Of Front Panel Controls (See Section 6-1)
1
Process/Contactor Switch
See Section 6-3 for Process/Contactor
switch information.
2 And 3 Displays
Displays can show weld process information
(voltage and amperage) or maintenance in-
formation (hourmeter, oil change count-
down, or rpm).
Meter Weld Functions
: In Wire modes, Volt-
meter displays preset weld voltage when not
welding. Meters display actual voltage and
amperage when welding and for five sec-
onds after welding has stopped.
In Stick and TIG modes, Voltmeter reads ON
and Ammeter displays preset amperage
when not welding. Meters display actual volt-
age and amperage when welding and for five
seconds after welding has stopped.
Meter Engine Maintenance Functions:
See inset from maintenance label.
For oil change interval, if negative hours are
indicated, CHNG OIL appears on the dis-
plays when the unit is started.
4
Voltage/Amperage Control
Use control to select weld voltage or
amperage. Control may be adjusted while
welding.
With Process/Contactor switch in any Stick
or TIG setting, use control to adjust amper-
age. With Process/Contactor switch in any
Wire position, use control to adjust voltage.
When a remote voltage/amperage control is
connected to Remote receptacle RC4, con-
trol sets the maximum amperage in Stick and
TIG modes, but has no effect in MIG modes.
5
Arc Control
See Section 6-3 for Arc Control information.
Control is not functional when one of the fol-
lowing modes is selected:
TIG
Gouge
Flux-Core
6
Fuel Level Indicator
With Engine running or Engine Control
switch in Run or Auto Speed position, LED’s
indicate fuel left in tank.
7
Glow Plug Switch
If necessary, push switch down before start-
up to activate glow plug. See glow plug table
above for operating information.
8
Engine Control Switch
Use switch to start engine, select speed, and
stop engine. In Auto Speed position, engine
runs at appropriate speed according to load
(see Section 6-3). In Run position, engine
runs at 3600 RPM.
Use switch in combination with meters to de-
termine total engine hours and hours until
next recommended oil change (see items 2
and 3 earlier in this section).
To Start:
Use glow plug switch if necessary
(see item 7 and glow plug table). Turn engine
control switch to Start. Release engine
control switch when engine starts.
If the engine does not start, let the en-
gine come to a complete stop before at-
tempting restart.
To Stop
: turn Engine Control switch to Off
position.
9
Remote Receptacle RC4
Use receptacle to connect remote control or
wire feeder.
When a remote voltage/amperage control is
connected to the Remote receptacle, the
Auto Sense Remote feature automatically
switches voltage/amperage control to the re-
mote control (see Sections 5-9 and 6-6).
With remote voltage/amperage control con-
nected, weld output in CC mode is determ-
ined by a combination of front panel and re-
mote control voltage/amperage settings. In
CV mode, weld output is controlled through
remote control only.
If no remote voltage/amperage control is
connected to the Remote receptacle, the
front panel Voltage/Amperage control ad-
justs voltage and amperage.
t
0 seconds
10 seconds
Glow Plug Time
Below 32
°
F (0
°
C)
68 to 32
°
F (20 to 0
°
C)
Above 68
°
F (20
°
C)
Do not use glow plugs longer than
20 seconds.
Do not use ether or other starting
fluids to start engine. Using start-
ing fluids voids warranty.
5 seconds
Содержание Trailblazer 325 Diesel
Страница 18: ...OM 258900 Page 14...
Страница 33: ...Complete Parts List available at www MillerWelds com OM 258900 Page 29 Notes...
Страница 47: ...Complete Parts List available at www MillerWelds com OM 258900 Page 43 259 872 258 899 C...
Страница 53: ...Complete Parts List available at www MillerWelds com OM 258900 Page 49 Notes...
Страница 54: ...OM 258900 Page 50 SECTION 10 ELECTRICAL DIAGRAMS Figure 10 1 Circuit Diagram For Welder Generator...
Страница 55: ...OM 258900 Page 51 258849 E...