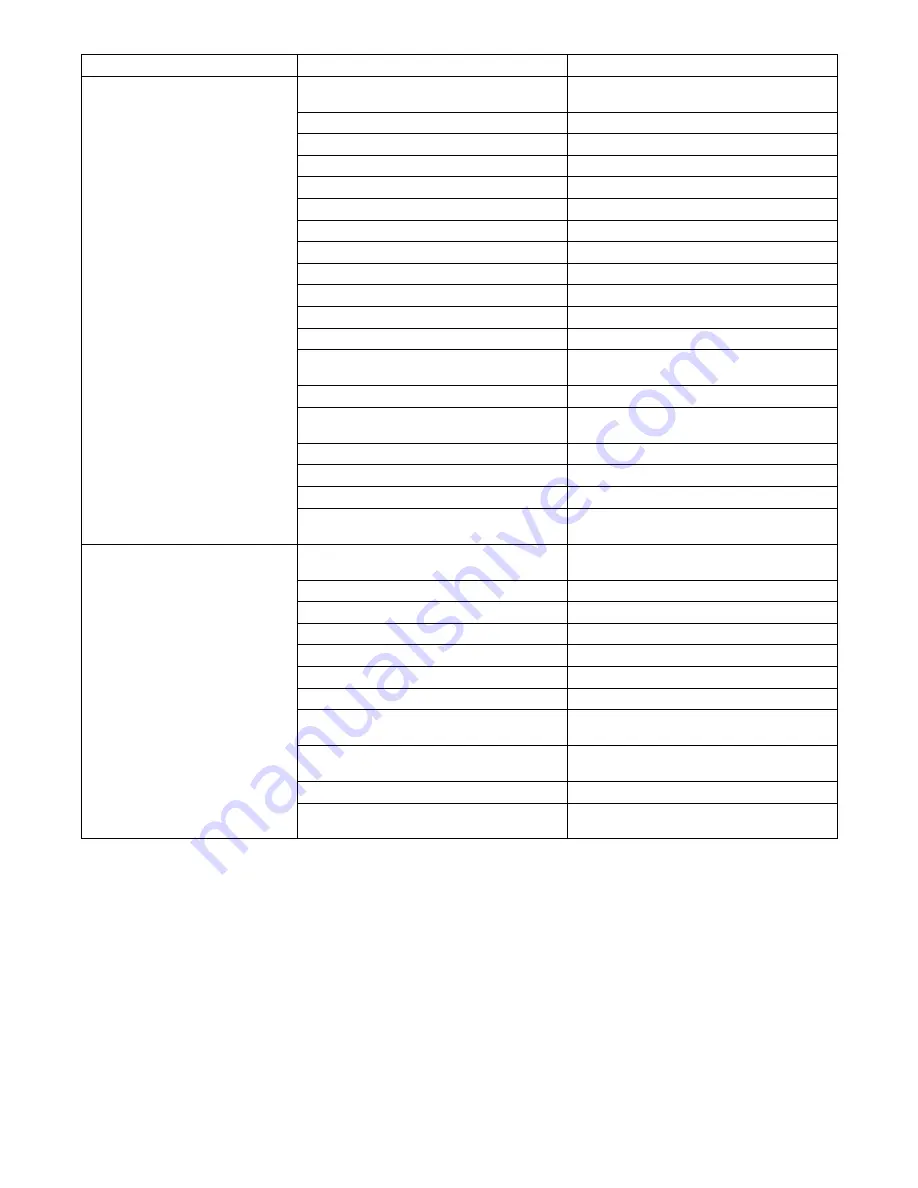
OM-257 798 Page 31
Trouble
Remedy
Probable Cause
Porosity in weld.
Dirty base metal, heavy oxides, mill scale, oil, etc. Clean base metal by brushing, grinding or use
chemical cleansing before welding.
Regulator/flowmeter faulty.
Adjust or replace regulator/flowmeter.
Gas cylinder valve closed.
Open gas cylinder valve.
Gas regulator diaphragm defective.
Replace regulator.
Flowmeter cracked or broken.
Repair or replace flowmeter.
Gas hose disconnected or leaking.
Connect or replace gas hose.
Too much or too little gas flow.
Adjust for proper gas flow.
Moisture in shielding gas.
Replace gas cylinder or supply.
Wrong gas for wire type or transfer mode.
Use correct shielding gas.
Feeder gas solenoid faulty.
Replace solenoid.
Gun or outlet cable leaking.
Repair or replace faulty parts.
Wire feed speed setting too high.
Reduce wire feed speed.
Contact tip extends too far out of nozzle.
Adjust or replace parts (max distance should not
exceed 1/8 in (3.2 mm).
Nozzle to work distance too large.
Reduce nozzle to work distance.
Incorrect gun or torch angle.
Set proper gun angle (porosity or dirty welds mean
gun angle is too large).
Nozzle restriction.
Clean off spatter or remove restriction.
Breeze or drafts in weld zone.
Shield weld zone from drafts.
Low shielding gas cylinder pressure.
Replace gas cylinder.
Gas leak at gun to feeder connection.
Properly install gun or replace O-rings at gun
connector.
Excessive spatter.
Voltage set too high.
Reduce voltage setting (reduce trim or arc adjust
for pulse welding).
Incorrect gun or torch angle.
Set proper gun angle.
Too much or too little gas flow.
Adjust for proper gas flow.
Wrong gas for wire type or transfer mode.
Use correct shielding gas.
Wrong electrode wire type or size.
Use proper electrode wire.
Wrong inductance setting.
Adjust inductance.
Electrode wire dirty or old.
Replace with new electrode wire.
Oily or dirty base metal.
Clean base metal by brushing, grinding or use
chemical cleansing before welding.
Excessive wire stick-out or nozzle to work distance
too great.
Adjust wire stick-out or reduce nozzle to work
distance.
Wrong transfer mode.
Set proper transfer mode.
Travel speed too slow.
Increase travel speed so that arc is on leading edge
of weld puddle.
Содержание Continuum 350
Страница 17: ...OM 257 798 Page 13 Notes...
Страница 27: ...OM 257 798 Page 23 Notes...
Страница 45: ...OM 257 798 Page 41 Notes...
Страница 47: ...OM 257 798 Page 43 264 238 B...
Страница 48: ...OM 257 798 Page 44 Figure 10 2 Circuit Diagram For Continuum 350 Model Page 2 of 2...
Страница 49: ...OM 257 798 Page 45 264 238 B...
Страница 50: ...OM 257 798 Page 46 Figure 10 3 Circuit Diagram For Contiuum 500 Model Page 1 of 2...
Страница 51: ...OM 257 798 Page 47 265 841 B...
Страница 52: ...OM 257 798 Page 48 Figure 10 4 Circuit Diagram For Continuum 500 Model Page 2 of 2...
Страница 53: ...OM 257 798 Page 49 265 841 B...
Страница 62: ...OM 257 798 Page 58 Notes...