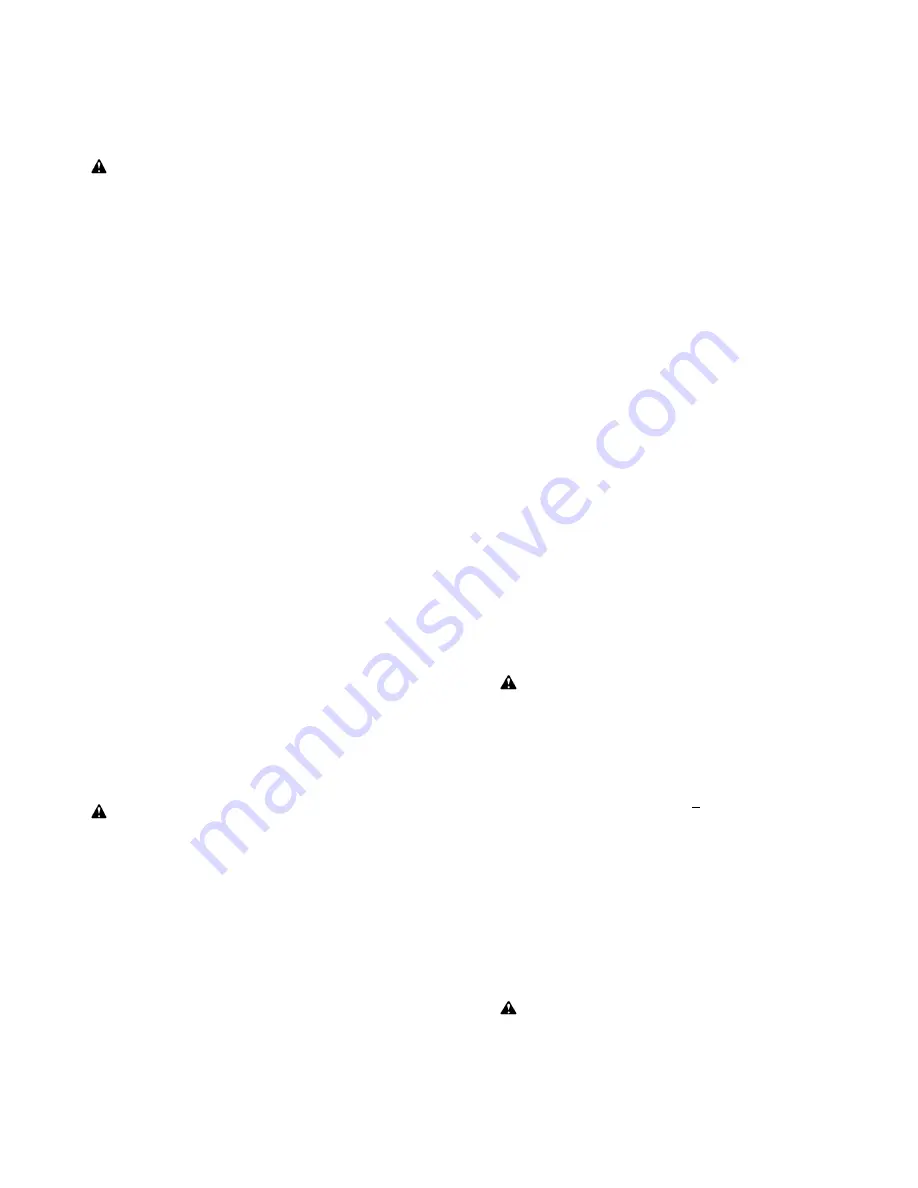
-7-
■
Check for high or low pilot gas pressure. Pilot gas pressure
tap is located in tee fitting in pilot gas line near bottom of back
plate. If over 7.0" W.C. with burner on, the size of pilot flame
should be reduced to increase heat on the thermocouple. Pilot
gas adjustment screw (needle valve) is located on the inlet end
of combination gas valve body and is factory set full open.
Remove plug for access and turn clockwise to reduce flow
(pressure).
CAUTION: If there is more than a 1.0"W.C. differential
between STANDBY inlet pressure when all appliances are
OFF, and the inlet pressure when the burner and all other
appliances are ON, a 1Ú8 inch Maxitrol RV12 (or equal)
pressure regulator must be installed in the pilot gas line.
With the adjustment screw wide open, set the pilot flame
gas pressure at 4.0"W.C. for NATURAL gas, 8.0"W.C. for
PROPANE.
■
Examine the thermocouple. If there is any serious corrosion
or loss of metal at the tip, replace the thermocouple.
■
The efficiency of the thermocouple and pilotstat safety
control of the combination valve can be determined by timing
the safety shut-off. With power to the burner shut off and with
the combustion chamber cool, allow the pilot to operate at
least five minutes. Then turn off the pilot and time the period
until a click is heard from the pilotstat safety control in the
Combination Valve. If less than 30 seconds or exceeds 3
minutes, the thermocouple, pilot flame adjustment or the
pilotstat safety control is faulty and the entire Combination
Valve must be replaced.
■
An accurate check of the thermocouple and pilot flame
adjustment can be made with a millivoltmeter. The
thermocouple, when heated by the pilot, should develop at
least 15 millivolts minimum to 25 millivolts maximum open
circuit (thermocouple disconnected from pilotstat safety control
of combination valve). If millivolt reading is above maximum,
readjust pilot gas input slightly to reduce voltage. Check
results with blower motor on and off.
■
Tests to isolate thermocouple and/or pilotstat safety control
problems can be conducted under closed circuit conditions
(thermocouple connected to valve through an
adaptor
that
provides for connecting the millivoltmeter). If the thermocouple
does not develop at least 7 millivolts when the pilot flame is
properly adjusted, it is defective. If the valve does not hold in
with 7 millivolts, the pilotstat safety control section is defective
and entire valve must be replaced.
■
If the thermocouple develops 15 millivolts minimum open
circuit and 7 millivolts minimum closed circuit but drop out
timing is under 30 seconds or exceeds 3 minutes, the pilotstat
safety control section is defective and entire valve must be
replaced.
WARNING: When reassembling burner, make sure
that the manifold slide plate is positioned in its holder and
that the main spud is inserted into the end of nozzle (see
Figures 5 and 6).
X
BLOWER SHELF ASSEMBLY
The shelf assembly including the blower and motor, motor
relay, low voltage transformer and terminal board can be
withdrawn as a unit after the back plate is removed and
external wiring is disconnected.
■
Cleaning of the blower wheel is usually the only service
required. Need for cleaning is indicated if the air inlet slots in
the burner housing show an accumulation of dust and lint, or if
the character of the flame -- long, hazy and yellow (sooty) --
indicates a deficiency of air. Motor air cooling vents should
also be cleaned at this time.
■
If the motor must be replaced, remove the blower wheel
first and remove the retainer clips at the rubber motor
grommets, pull the motor out of keyhole brackets. Remount
in reverse order noting that brass flanges of rubber motor
mounts are located against motor. Do not omit the three
clips. Position blower wheel on motor shaft to provide 1/8
inch clearance between blower inlet opening and blower
wheel ring.
■
Shelf gaskets are installed on the inside of the back cover
and inside of the front of the burner cabinet. Be sure they are
in place when reinstalling the shelf assembly, otherwise
blower air will be lost and combustion could be affected.
XI
COMBINATION GAS VALVE
The 24 volt combination valve serves five functions:
1. Main manual and pilot gas shut-off,
2. Manifold gas pressure regulation,
3. Pilot gas input adjustment,
4. Automatic electric main gas valve; single seated on
Model E20B, double seated (redundant) on E20BP
Models, and
5. Pilotstat safety control.
A pilot filter is also included.
■
For manual control the manual gas cock knob is turned full
ON
or full
OFF
. The dial has to be depressed to be turned in
one direction, but it depends on the manufacturer of the valve
whether it is in the
ON
or
OFF
position.
■
Refer to Section IX for pilot adjustment.
■
The combination valve gas pressure regulator has an outlet
pressure setting range of 2.0" to 4.0" W.C. and is factory set
for 2.0" W.C. Manifold gas pressure tap is located on the
outlet end of the combination gas valve body.
■
If pressure adjustment is required for setting capacity,
remove regulator cap for access to slotted adjustment screw.
Turning of adjustment screw counterclockwise reduces
pressure; clockwise increases pressure. Do not adjust past
point where no change in pressure is noted.
NOTE:
Pressure setting can only be made with burner run-
ning and gas on.
CAUTION: If gas supply pressure is below its
specified range during adjustment, an overfire condition
could result when pressure returns to normal, particularly
if the regulator adjustment screw is bottomed out. AL-
WAYS confirm that at least the minimum rated gas pres-
sure is being supplied to the burner during regulator ad-
justments, and NEVER bottom out regulator screw.
■
If the pressure regulator fails to maintain a constant
manifold gas pressure 0.1" W.C., with an inlet
pressure within the specified 5"-14" W.C., the regulator
section of the valve is defective and entire valve must be
replaced.
■
The pilotstat safety control may be suspect if frequent "pilot
outages" occur. Refer to Section IX to isolate the problem.
■
If, on a call for heat, the main burner fails to operate even
though the pilot is burning and the motor is running, failure of
the electric valve operator(s) may be indicated. Refer to the
TROUBLE CHART for further information.
■
If leakage through the valve occurs on standby, as
evidenced by the presence of any flame other than pilot, the
entire valve must be replaced.
CAUTION: If the combination valve has been moved
or replaced, soap bubble test for leaks with the burner
running.