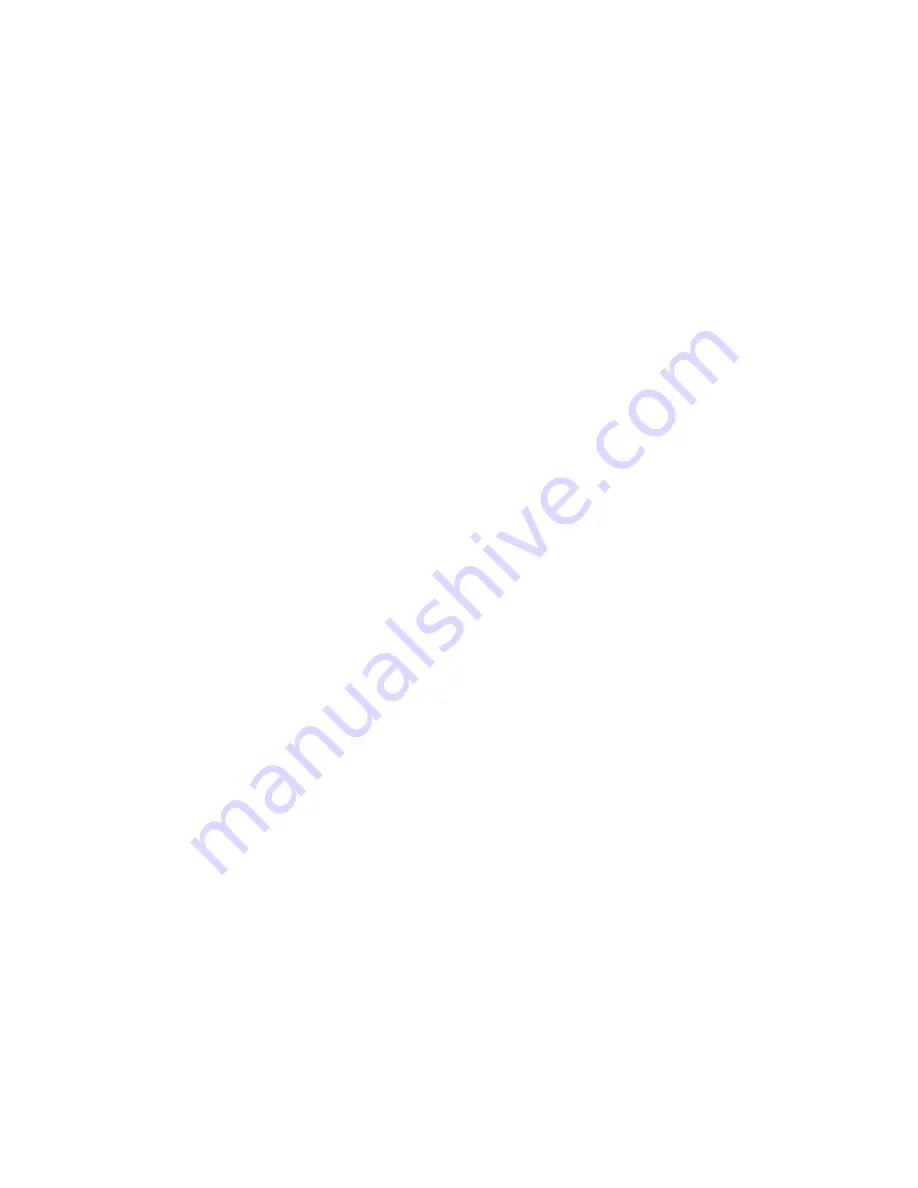
2.0 GENERAL OPERATING INSTRUCTIONS
2.1 ELECTRICAL HOOK-UP INSTRUCTIONS
First determine that available electrical service in your
plant corresponds to the nameplate rating located on welder
housing. Electrical wiring to welder must be of sufficient
size to deliver full ampere load with no appreciable loss
during the weld cycle. The welder will not operate
properly if there is more than a 10% variation in the line
voltage. In general, the welder should be fused with a
slow blow fuse of the 100% duty cycle rating. The minimum
power cable size to the welder can be obtained by using
this same current rating.
Refer to National Electrical Code and local electrical
regulations for adequate power sizes; disconnect methods
and fusing guidelines.
Remember line voltages to the welding machine are
potentially dangerous should the power cords be damaged or
severed. The welding voltages at the welding dies will not
harm an operator since they do not exceed 10 volts.
2.2 SAFETY
PRECAUTIONS
2.2.1 ELECTRICAL
Maintain electrical cables to welder in good repair.
Welders must be grounded and connections securely
tightened. Heat switch must not be changed to a new
position while a weld cycle is in process. Disconnect
electrical service before servicing the welder – high
voltages are located within the base of the welder.
2.2.2 MECHANICAL
Operator while using welder must wear safety glasses. Keep
all safety guards on welders and use properly. Operators
must be instructed on the basic operation of unit to
prevent injury. Check nameplate rating and keep within
material size range for each welder.
2.3 WELDING
DIES
The dies and shoes supplied with the welder will handle
most size and material types within the range of the
welder. For new weld applications consult the factory for
special die and shoe sets.
3
Содержание GP0
Страница 5: ...4 0 BASIC OPERATING PARTS LOCATION 5 ...
Страница 11: ...8 2 CERAMIC FUSION TECHNIQUE 11 ...
Страница 14: ...14 ...
Страница 17: ...13 0 PARTS LIST 17 ...
Страница 18: ...18 ...
Страница 19: ...19 ...