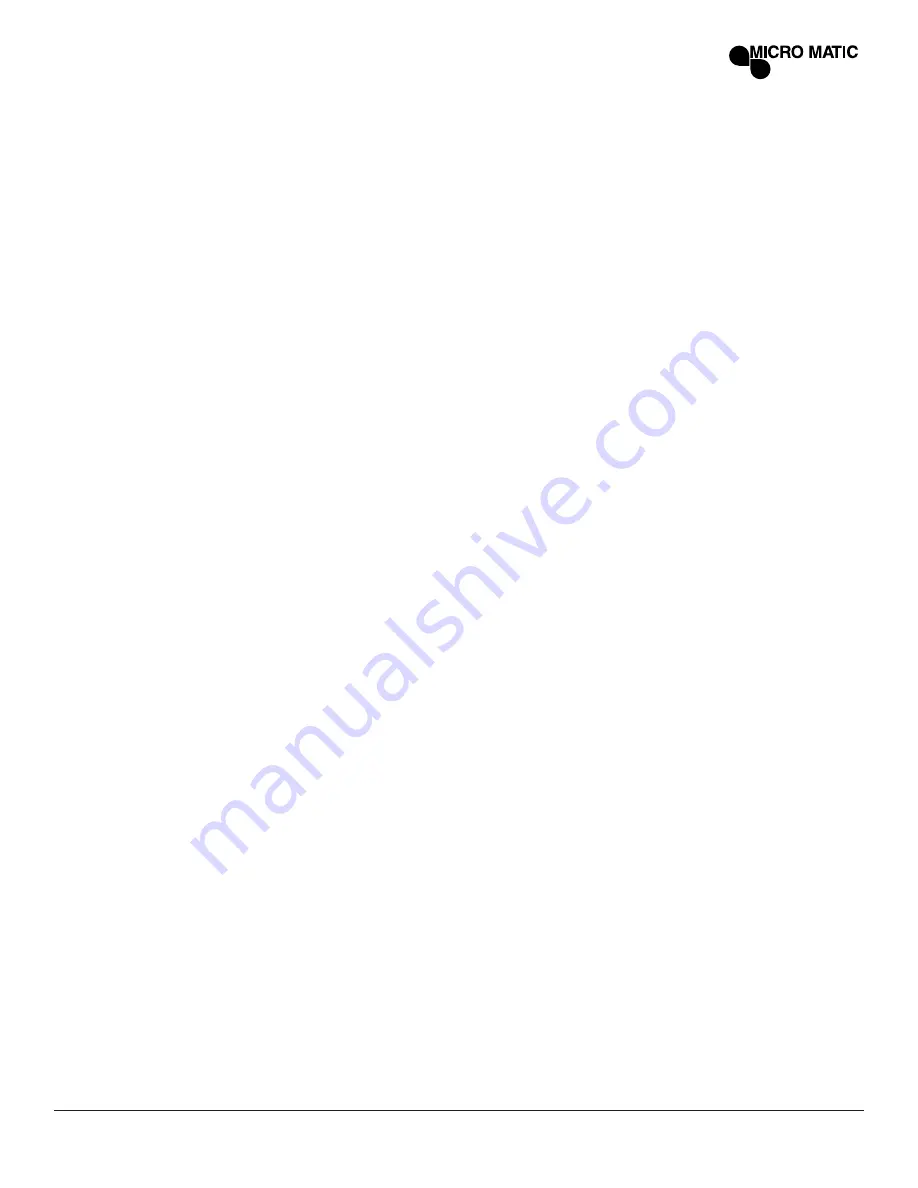
MICROMATIC.COM | 866-327-4159
REMOTE POWER PACK SERVICE MANUAL
|
7
CONDENSING UNIT INSTALLATION STEPS
NOTICE - INSTALLATION AND SERVICE OF THE REFRIGERATION AND ELECTRICAL COMPONENTS
MUST BE PERFORMED BY A REFRIGERATION MECHANIC OR LICENSED ELECTRICIAN.
DANGER – EQUIPMENT MUST BE PROPERLY GROUNDED. IMPROPER OR FAULTY HOOK-UP OF
ELECTRICAL COMPONENTS OF THE REFRIGERATION UNITS CAN RESULT IN SEVERE INJURY OR
DEATH. ALL ELECTRICAL WIRING HOOK-UPS MUST BE DONE IN ACCORDANCE WITH ALL APPLI-
CABLE LOCAL, REGIONAL, OR NATIONAL STANDARDS.
The condensing unit should be located at a minimum of 18” between the face of the coil (air intake)
and a wall or other vertical obstruction and have 24” clearance on the sides and air exhaust of the unit.
If mounted indoors, room should be provided with fans designed to move 1000 CFM of air per ton of
refrigeration.
ELECTRICAL – Electrical power supply must match the condensing unit power requirements indicat-
ed on the unit data plate. All field wiring should be done in a professional manner, in accordance with
all governing codes. Double check all wiring connections, including factory terminals, before startup of
condensing unit.
REFRIGERANT PIPING – The condensing unit must remain sealed until piping is complete and final
connections are ready to be made. Use only refrigeration grade copper tubing (ACR), Type “L”, bright
annealed, dehydrated, and properly sealed against contamination. Take caution to keep refrigeration
tubing clean and dry prior to installation.
Suction lines should slope down ½” for each 10 feet of horizontal run towards the compressor. If
any portion of the suction line rises above the exit elevation of the evaporator (bath), p-type oil traps
should be located at the base of each suction riser for proper oil return to the compressor. A properly
sized filter drier and sight glass must be brazed onto the liquid side of the system downstream of the
receiver.
When brazing, dry nitrogen MUST be passed through the lines at low pressure to prevent scaling and
oxidation inside the tubing and fittings. All flux must be removed from joints after brazing.
Fifteen percent silver brazing wire should be used on all copper to copper connections and 45% silver
brazing wire on all dissimilar metal connections.
If pressure control and fan cycle control have not been connected to the appropriate ports on the ser-
vice valves, make those connections now. Make sure the pressure control settings are appropriate for
the refrigerant being used.