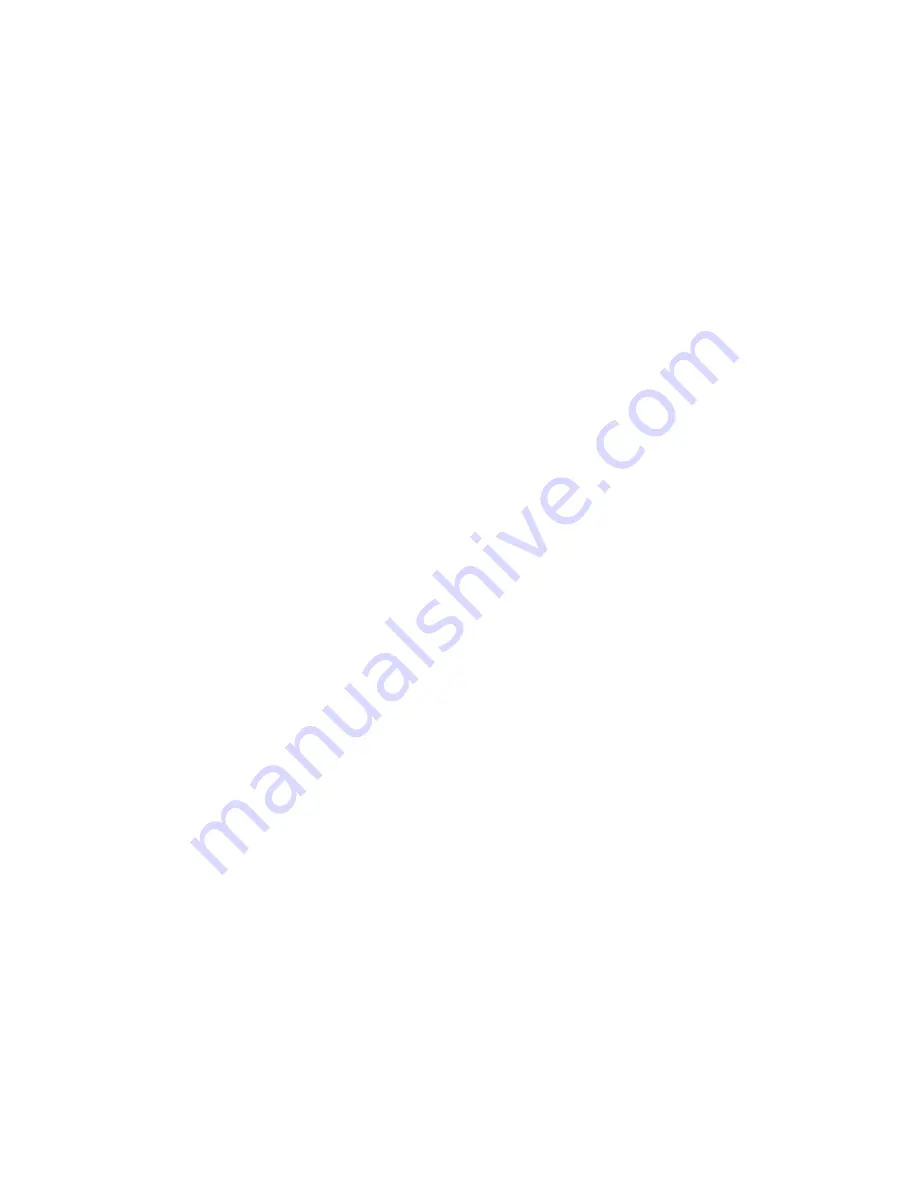
Please note that this kind of tubing is not advised for pressurized aircraft. In this case you would
need to obtain aircraft grade tubing of suitable diameter. You would also have to use hose clamps
to fasten the hose onto the Stratomaster pitot and static ports.
The Flight II allows you to calibrate the airspeed reading. This is done in the “ASI Cal” menu item.
The main reason for this is to be able to remove errors introduced due to the airflow around your
aircraft which may have an effect of your pitot tube pressure.
Rev counter pickup
The above drawing shows a typical connection for a standard “old fashioned” contact breaker
system. Most electronic ignition systems are very similar, the only difference is that the breaker
has been replaced with a semiconductor switching device. Most electronic ignition modules have
an output terminal intended for connection to a rev counter.
This sample circuit suggests a 2200 ohm resistor (2K2) and a 20V zener diode. Note that the
zener diode is a polarized device, install with the band marker as shown. This small circuit should
be installed if older contact breaker ignition systems are used as it is possible for these systems
to generate very high voltages over the contact breaker. This could potentially damage the
instrument if no protection is used. The components can be obtained from any electronics parts
shop and are very inexpensive.
Most other sources of RPM pickup do not require any further protection.
The Flight II RPM input is quite universally usable. For example, it is common to connect a hall-
effect sensor using the +5V line to supply the sensor. A small magnet it then mounted on a shaft
(for example rotor shaft of a helicopter) and the hall effect sensor switches every time the magnet
passes the sensor.
The Flight II needs a typical voltage swing of about 4 to 5.5V minimum to operate and the input is
A/C coupled for easy installation. This means that the voltage signal may have a DC voltage
superimposed without affecting the instrument. For example, if you have a signal that varies in
voltage from 5V to 10V with every pulse, it can be used with the Flight II.
For installations such as with the Rotax DCDI two-stroke engines, the rev counter input is simply
connected to the grey rev counter wire from the engine. These engines produce six pulses per
rev (set this up in the relevant menu item).
Please note that is appears very common that many Rotax engines require a ballast resistor on
the grey rev counter pickup wire. Some of these engines produce a very noisy signal without this
ballast that can result in very unstable RPM readings. We have found a resistor of about 220
ohms to be a good value for most cases. Some engines may need as little as 100 ohms. This
ballast resistor should in some cases also be used for the Rotax 912 engines.
Most engines produce 0.5, 1 or 2 pulses per revolution. This needs to be setup in the “Calib”
menu item.
Please note: The 5V supply line is unprotected and intended only for the supply of hall-
effect, optical or geartooth sensors. Connecting any voltages (such as the 12V supply) to
this line will destroy the instrument.
The 5V line may supply currents of up to 30mA. Should your sensor require greater
currents you must supply it from another source.