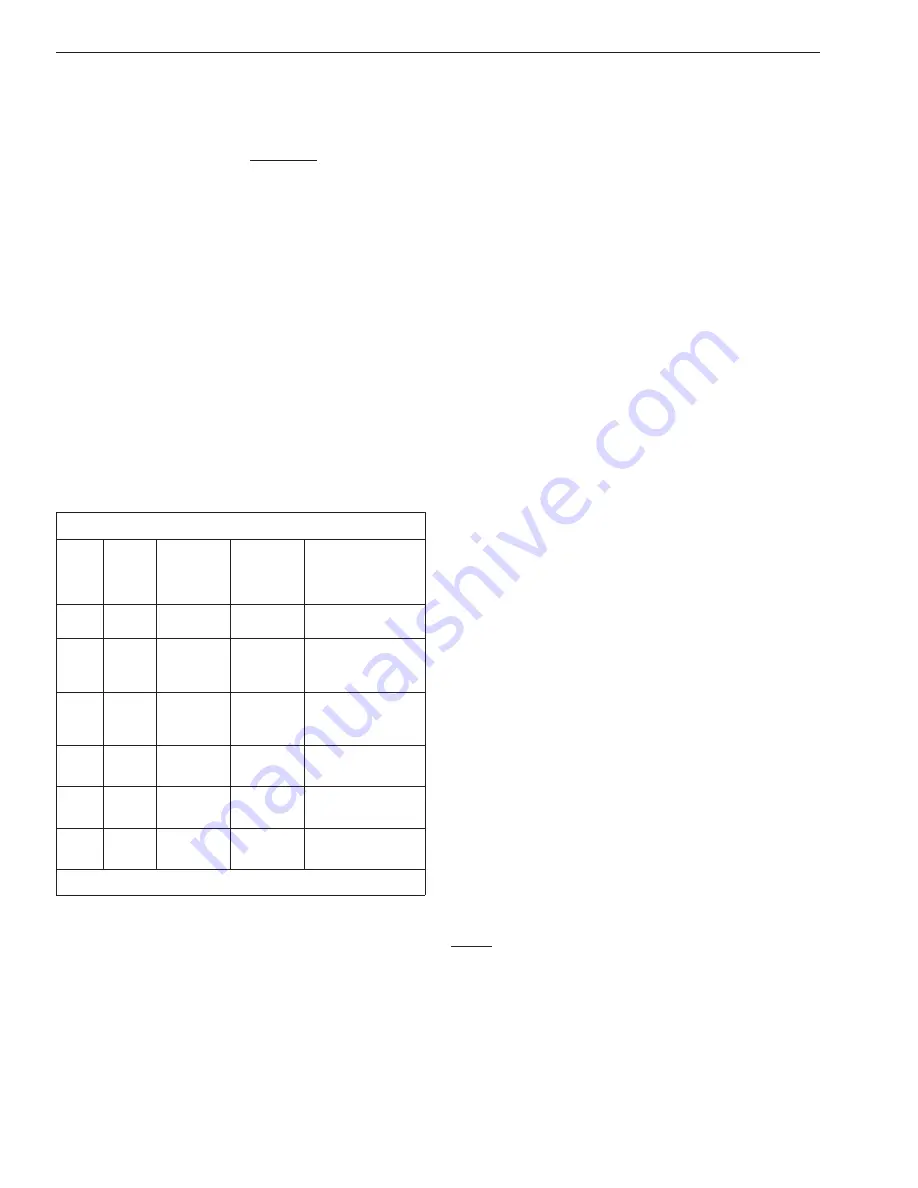
3. Mount the actuator to the valve following the directions
in the AMI (Actuator Mounting Instructions) or valve IMO.
4. Connect a regulated air supply to the 3/8” NPT fitting
in the diaphragm casing (15). *QP6 has a 3/4” NPT
air supply connection. CAUTION: The maximum
operating pressure is 100 psi (6.9 BAR).
5. Adjust the stop screws (19) by releasing the jam
nut (23) and turning. Stops can only be adjusted
when driver arm (3) is off the stop screws being
adjusted. (Maximum rotation adjustment ±5°.) Be sure
to retighten jam nut (23).
2.1
Operation
The operating pressure, output torque and drive type
is determined by the actuator designation. Maximum
operating pressure is 100 psi (6.9 BAR). (See Table 2)
Actuator designation example: QP4C/34 is a series QP4
spring diaphragm actuator that has a 60 psi (4.1 BAR)
spring, an end of stroke output torque of 200 FT•LBS (272
N•m) and uses a 34mm spline to drive the valve.
Before operating make sure all tapped holes in the body
which are not being used are resealed with plastic caps.
TABLE 2
Actu-
ator
Series
Spring
Version
Operating
Pressure In
psl (BAR)
End of
Spring
Stroke
Torque In
FT•LBS (N•m)
Drive Type
QP1
C
60 (4.1)
25 (34)
14 - 14mm Spline
M - 9/16” Square
QP2
A
B
C
D
20* (1.4)
40 (2.8)
60 (4.1)
80 (5.5)
11 (15)
38 (52)
57 (77)
74 (100)
14 - 14 mm Spline
18 - 18 mm Spline
25 - 25 mm Spline
M - 9/16” Square
QP3
A
B
C
D
20* (1.4)
40 (2.8)
60 (4.1)
80 (5.5)
26 (35)
76 (103)
114 (155)
146 (198)
18 - 18 mm Spline
25 - 25mm Spline
34 - 34 mm Spline
M - 3/4” Square
QP4
B
C
D
40 (2.8)
60 (4.1)
80 (5.5)
153 (207)
229 (310)
294 (399)
25 - 25 mm Spline
34 - 34 mm Spline
M - 1” Square
QP5
B
C
D
40 (2.8)
60 (4.1)
80 (5.5)
305 (414)
458 (621)
587 (796)
34 - 34 mm Spline
M - 1” Square
QP6
B
C
D
40 (2.8)
60 (4.1)
80 (5.5)
527 (716)
818 (1112)
1076 (1463)
45 - 45 mm Spline
* For Direct Control Applications
3.
MAINTENANCE
Before working on a
Quadra-Powr
II actuator, note that all
fasteners except socket head shoulder screw (8) are metric.
Although Metso’s
Jamesbury
actuators are designed to work
under severe conditions, proper preventative maintenance
can significantly help to prevent unplanned downtime and
in real terms reduce the total cost of ownership. Metso
recommends inspecting actuators at least every five (5)
years. The inspection and maintenance frequency depends
on the actual application and process condition. Standard
replacement of “soft” parts in
Quadra-Powr
II actuators
consists of items numbered 6, 14, 31, 62 and 64. See REPAIR
KITS/SPARE PARTS Section.
1. When replacing the diaphragm use caution and be sure
the air supply is disconnected. Back off nuts (29) from
the hex head screws (25) or (27),holding the diaphragm
casing and spring housing together until the nuts are
flush with the hex head screw ends.Do not remove the
nuts completely from the hex head screws. If tension
still exists on the hex head screws, then the spring
package is not properly contained. Stop disassembly:
retighten nuts and return the actuator to the factory. If
the spring package proves to be intact remove the nuts
(29) and remove the hex head screws (25) or (27).
2. Lift off diaphragm casing (15) and diaphragm (14).
3. Inspect the inside of both the diaphragm casing (15) and
the spring housing (32) for any rough spots or foreign
matter which may cause abrasion to the diaphragm.
Check the plastic guide buttons (64) inserted to the
diaphragm retainer. Replace the ones which have been
worn out.
4. Place the new diaphragm (14) on the diaphragm
retainer (10). Place the diaphragm casing (15) on the
spring housing (32) and line up all the holes. Do not
pinch or stretch the diaphragm.
5. Insert hex head screws (25) or (27) in all holes. Do not
force the hex head screws through the diaphragm. Install
nuts (29) on screws and tighten uniformly using the
standard practice of tightening diametrically opposite
bolts in sequence with the torque requirements from
(Table 3).
3.1
Disassembly
When disassembly of the actuator is required for maintenance,
remove the actuator to a clean well lit area. Handling of the
actuator is accomplished by using two (2) M10 eye-nuts
screwed on to the two hex head screws (25), that are facing
the opposite direction of the other fasteners holding the
diaphragm casing (15), and spring housing (32) and lifting the
actuator by the eye-nuts, not the 3/8” NPT or 3/4” NPT in the
diaphragm casing (15). For the QP6 use four M10 eye-nuts.
Prior to disassembling the actuator, obtain the following
tools: two (2) M10 wrenches,preferably one being a ratchet,
one (1) hex (Allen) wrench, 3mm for QP1, 5mm for QP2, 3
and 4, 6mm for QP5, 10mm for QP6, one (1) screwdriver,
one (1) plastic faced mallet.
NOTE: When disassembling the QP6 DO NOT remove the
socket shoulder screw (8) AND the diaphragm casing (15)
at the same time. Either the socket shoulder screw (8) or
the diaphragm casing (15) must be in place while working
on the other.
1. Remove the cover (5) by removing six socket cap
screws (21) on QP1 - 5, eight socket cap screws on
the QP6. If the cover cannot be removed, tap it with
a plastic hammer to break the adhesion of the paint
between the body and cover joint.
IMO 11/17
4
IMO-031 EN
Содержание Quadra-Powr II
Страница 10: ...IMO 11 17 10 IMO 031 EN ...
Страница 11: ...IMO 11 17 IMO 031 EN 11 ...