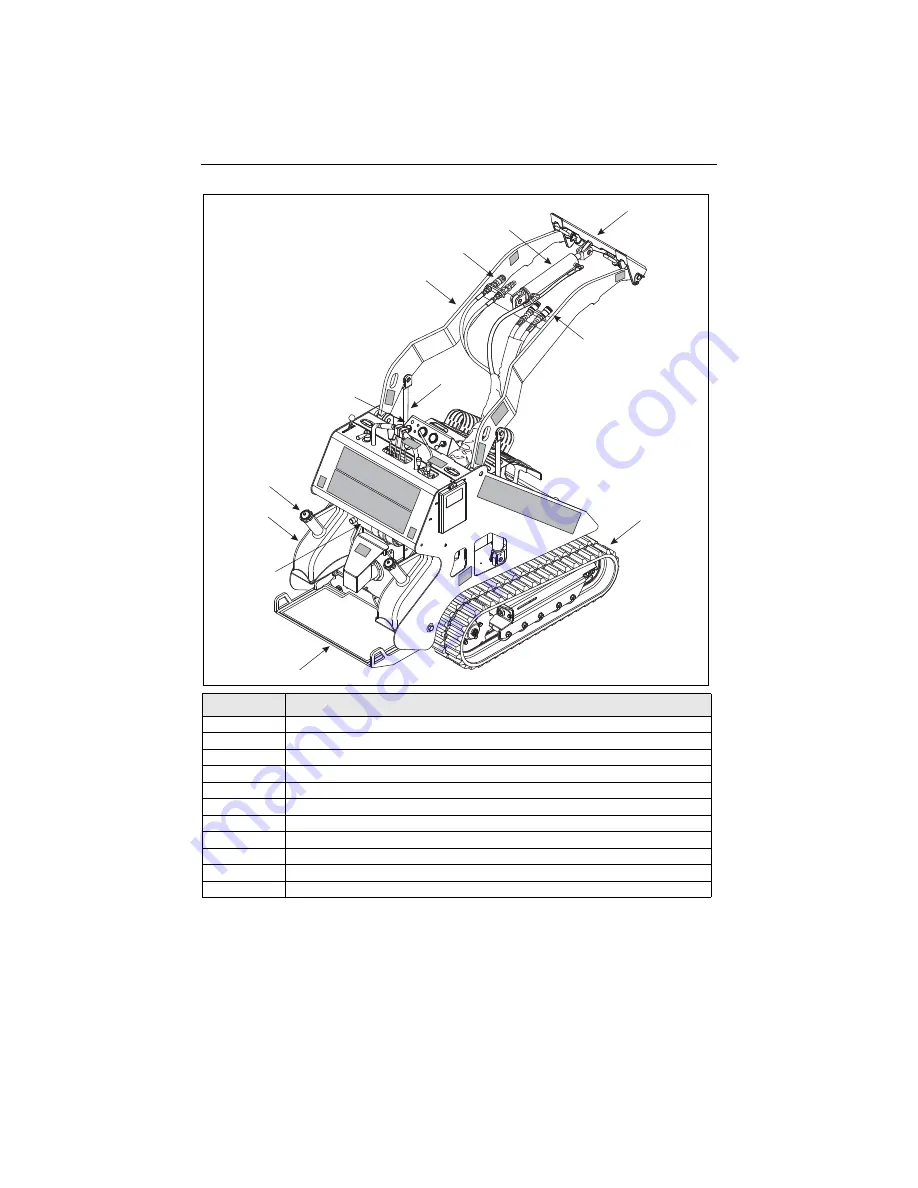
2-2
Operating Controls
Right Rear View
Item No.
Description
1
Attachment mounting plate
2
Attachment hydraulic quick connects
3
Right track assembly
4
Operator's platform
5
Air cleaner assembly
6
Fuel tank
7
Fuel filler cap
8
Engine hour meter
9
Loader arm lift cylinder
10
Loader arms
11
Lift cylinder
1
11
2
10
2
9
8
7
6
5
4
3
2152
Содержание 999-848.01
Страница 6: ...iv Mertz Manufacturing LLC P O Box 150 Ponca City OK 74602 Affix Stamp Here...
Страница 8: ...vi...
Страница 18: ...1 8 Safety Precautions...
Страница 26: ...2 8 Operating Controls...
Страница 54: ...3 28 Pre Start Inspection and Operation...
Страница 86: ...5 4 Troubleshooting...