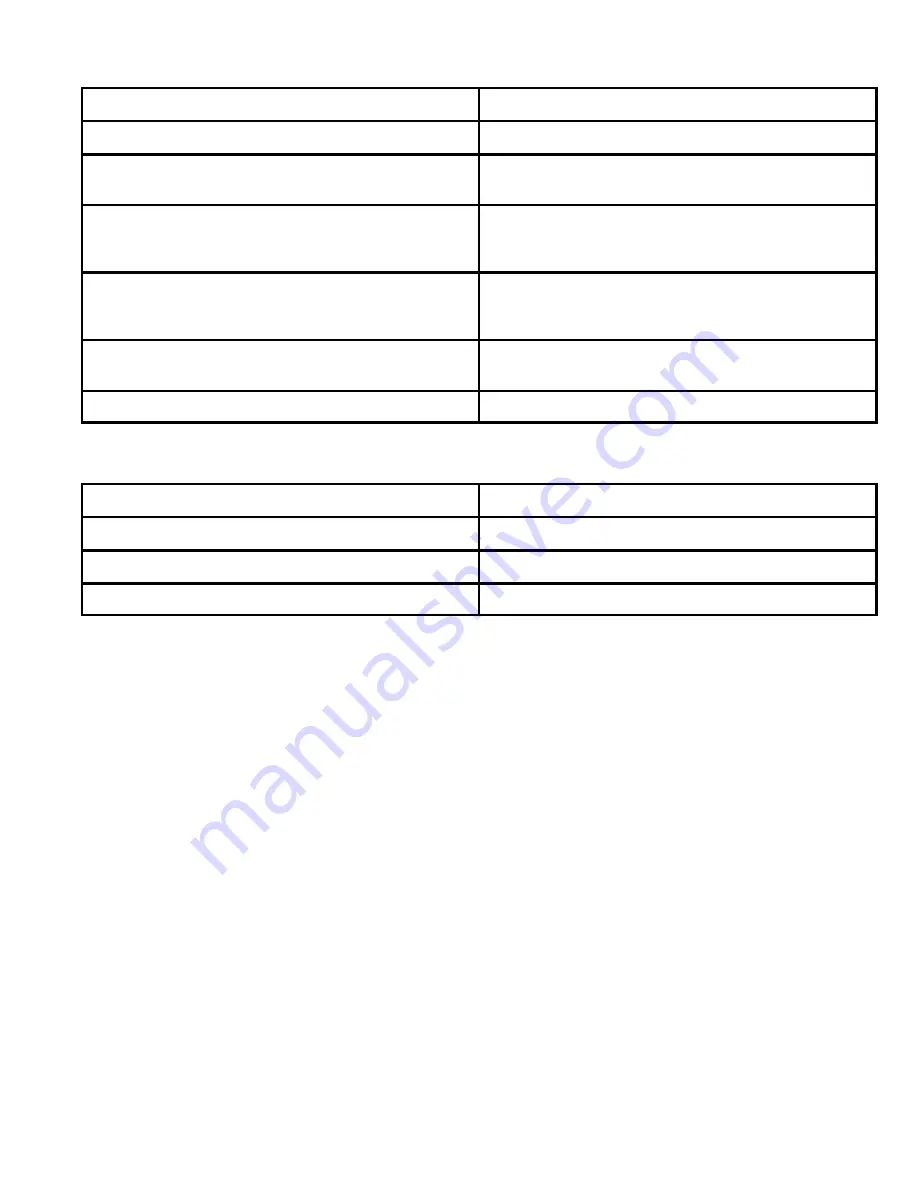
TROUBLESHOOTING - 1C-23
90-823225--1 1096
Low Oil Pressure
Cause
Special Information
Low oil level in crankcase
Defective oil pressure gauge and/or sender
Verify with an automotive test gauge. Refer to
Section 4D for instrument testing.
Thin or diluted oil
Oil broken down; contains water or gas; wrong
viscosity; engine running too hot or too cold;
excessive idling in cold water (condensation)
Oil pump
Relief valve stuck open; pickup tube restricted;
worn parts in oil pump; air leak on suction side of
oil pump or pickup oil tube
Oil leak can be internal or external
Oil passage plugs leaking, cracked or porous
cylinder block
Excessive bearing clearance
Cam bearings, main bearings, rod bearings
High Oil Pressure
Oil too thick
Wrong viscosity, oil full of sludge or tar
Defective oil pressure gauge and/or sender
Verify with an automotive test gauge
Clogged or restricted oil passage
Oil pump relief valve stuck closed
Содержание 305 CID
Страница 7: ...A 1 72000 IMPORTANT INFORMATION GENERAL INFORMATION...
Страница 16: ...B 1 IMPORTANT INFORMATION MAINTENANCE...
Страница 59: ...C 1 IMPORTANT INFORMATION TROUBLESHOOTING...
Страница 92: ...A 2 72975 REMOVAL AND INSTALLATION MCM MODELS ALPHA ONE DRIVES...
Страница 103: ...B 2 70246 REMOVAL AND INSTALLATION MCM MODELS ALPHA ONE DRIVES WITH DRIVESHAFT EXTENSION...
Страница 120: ...2 72580 C REMOVAL AND INSTALLATION MCM MODELS BRAVO DRIVES...
Страница 135: ...D 2 70246 REMOVAL AND INSTALLATION MCM MODELS BRAVO DRIVES WITH DRIVESHAFT EXTENSION...
Страница 154: ...E 2 70648 REMOVAL AND INSTALLATION MIE MODELS VELVET DRIVE TRANSMISSIONS...
Страница 173: ...F 2 25280 REMOVAL AND INSTALLATION MIE MODELS HURTH TRANSMISSIONS...
Страница 189: ...A 3 72615 ENGINE 5 0L 305 CID 5 7L 350 CID...
Страница 192: ...3A 0 ENGINES 90 823225 1 1096...
Страница 266: ...ELECTRICAL SYSTEMS STARTING SYSTEM A 72079 4...
Страница 284: ...STARTING SYSTEM 4A 17 90 823225 1 1096 THIS PAGE IS INTENTIONALLY BLANK...
Страница 308: ...B 4 72722 90 823224 692 4B IGNITION SYSTEM ELECTRICAL SYSTEMS THUNDERBOLT IV AND V IGNITION SYSTEM...
Страница 334: ...C 4 72078 ELECTRICAL SYSTEM CHARGING SYSTEM...
Страница 344: ...CHARGING SYSTEM 4C 9 90 823225 1 1096 THIS PAGE IS INTENTIONALLY BLANK...
Страница 360: ...D 4 72747 ELECTRICAL SYSTEM INSTRUMENTATION...
Страница 380: ...E 4 72761 ELECTRICAL SYSTEM ELECTRICAL KITS...
Страница 393: ...F 4 72938 ELECTRICAL SYSTEMS WIRING DIAGRAMS...
Страница 427: ...A 5 50830 90 823224 692 5A FUEL DELIVERY SYSTEMS AND FUEL PUMPS FUEL SYSTEM FUEL DELIVERY SYSTEMS AND FUEL PUMPS...
Страница 438: ...B 5 72681 FUEL SYSTEM MERCARB 2 BARREL CARBURETOR...
Страница 467: ...C 5 72085 FUEL SYSTEMS ROCHESTER 4 BARREL CARBURETOR...
Страница 497: ...D 5 70389 90 823224 692 5B WEBER 4 BARREL CARBURETOR FUEL SYSTEMS WEBER 4 BARREL CARBURETOR...
Страница 538: ...5 71692 E FUEL SYSTEMS MULTI PORT AND THROTTLE BODY FUEL INJECTION...
Страница 541: ...90 823225 1 1096 5E 0 ELECTRONIC FUEL INJECTION MULTI PORT AND THROTTLE BODY THIS PAGE IS INTENTIONALLY BLANK...
Страница 558: ...ELECTRONIC FUEL INJECTION MULTI PORT AND THROTTLE BODY 5E 17 90 823225 1 1096 THIS PAGE IS INTENTIONALLY BLANK...
Страница 591: ...90 823225 1 1096 5E 50 ELECTRONIC FUEL INJECTION MULTI PORT AND THROTTLE BODY THIS PAGE IS INTENTIONALLY BLANK...
Страница 727: ...F 5 73662 FUEL SYSTEMS BOS SAV EMISSIONS...
Страница 744: ...A 6 22381 COOLING SYSTEM SEAWATER COOLING MODELS...
Страница 773: ...B 6 72987 COOLING SYSTEM CLOSED COOLED MODELS...
Страница 823: ...A 7 72699 EXHAUST SYSTEM GENERAL...
Страница 828: ...THIS PAGE IS INTENTIONALLY BLANK TO ALLOW FOR CORRECTIONS OR ADDITIONS AT A LATER DATE 7A 4 GENERAL 90 823225 1 1096...
Страница 829: ...B 7 72695 EXHAUST SYSTEM MANIFOLDS AND ELBOWS...
Страница 835: ...C 7 70593 EXHAUST SYSTEM RISERS...
Страница 843: ...THIS PAGE IS INTENTIONALLY BLANK TO ALLOW FOR CORRECTIONS OR ADDITIONS AT A LATER DATE RISERS 7C 7 90 823225 1 1096...
Страница 844: ...D 7 72737 EXHAUST SYSTEM COLLECTORS...
Страница 855: ...THIS PAGE IS INTENTIONALLY BLANK TO ALLOW FOR CORRECTIONS OR ADDITIONS AT A LATER DATE 7D 10 COLLECTORS 90 823225 1 1096...
Страница 856: ...A 8 DRIVES VELVET DRIVE IN LINE TRANSMISSION...
Страница 869: ...B 8 DRIVES VELVET DRIVE V DRIVE AND WALTER V DRIVE TRANSMISSION...
Страница 882: ...C 8 25280 DRIVES HURTH DOWN ANGLE TRANSMISSION...
Страница 932: ...E 8 DRIVES DRIVE SHAFT PROPELLER SHAFT MODELS...
Страница 947: ...A 9 72951 POWER STEERING PUMP...