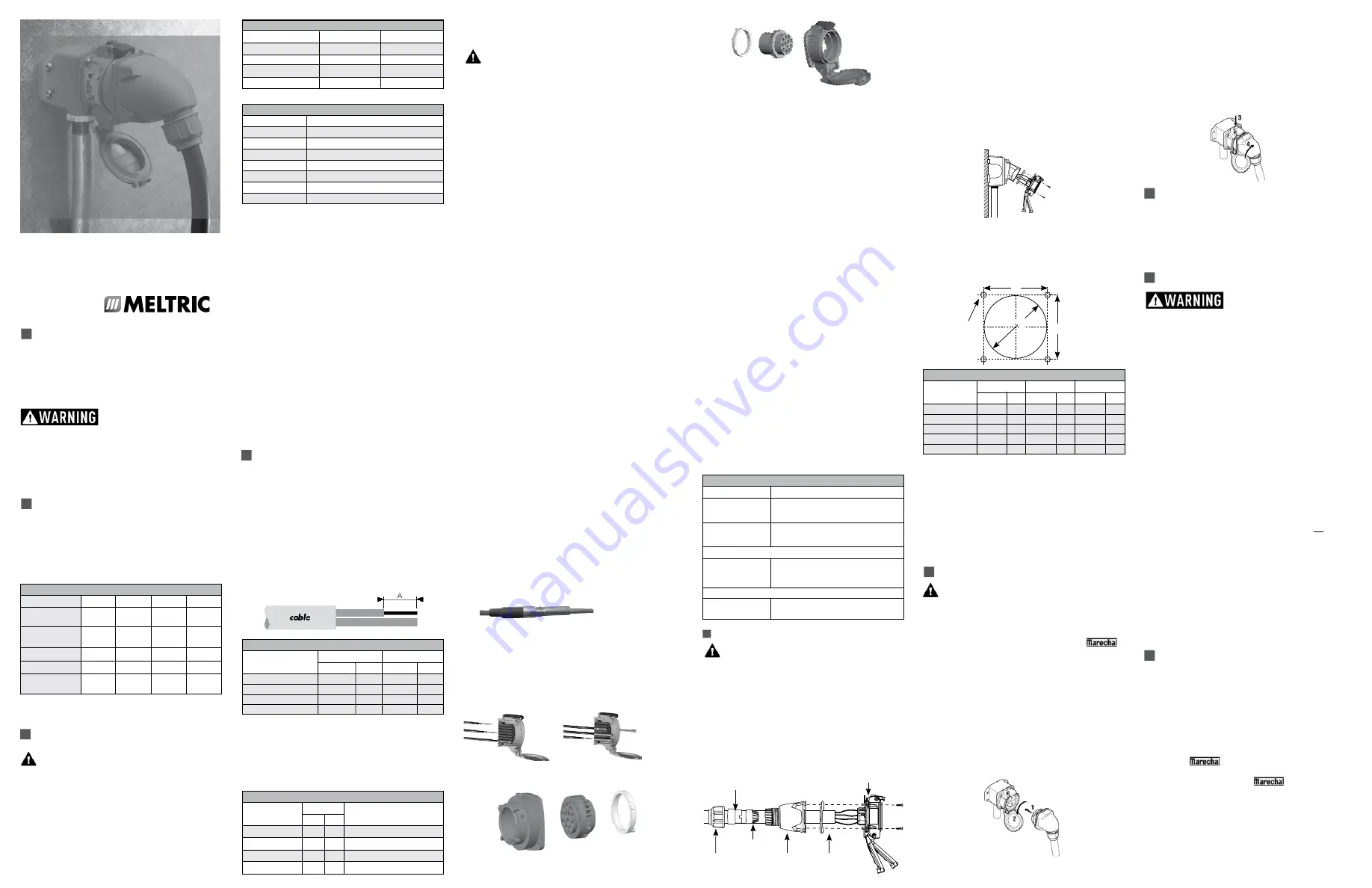
Orientation of Receptacle Assembly
1.
NOTICE:
Before insertion of a contact into an
insulator, please review the insulator’s contact
numbering scheme so the ground and each
contact (phase) is placed into the proper hole.
2. Push the wired contact into the insulating block
until it stops and snaps into place.
3. Ensure its correct mounting by slightly pulling on contact.
4. The male contacts are solid for their entire
length and are inserted with the contact tip first
into the rear of the inlet/plug.
5. The female contacts consist of a flexible braid
and spring and are inserted with the contact tip
first into the rear of the lidded receptacle/connector.
6. Insert the Provided Hole Plugs into the unused
holes in the front of each insulating block.
NOTICE:
If a new Receptacle or Inlet is to mate
with a previously installed device, pay particular
attention to the number of contacts and
numbered position in the Receptacle or Inlet.
Continuity will not be obtained unless the male
and female contacts are evenly mated.
Disassembly of PN12c Contacts
1. To remove the contact from the insulating block, the
provided Multi-Contact Removal Tool 9-LD12-37 must
be used. From the front side of the insulating block,
slide the contact removal tool over the contact.
2. Push until the contact pops out the back side of
the insulating block.
3.
NOTICE:
Each contact is designed to be
removed from the insulating block a maximum
of 3 times. New contacts should be used if
contacts are removed more than 3 times.
ASSEMBLY
Verify power has been disconnected prior to assembly.
For In-Line Connections
Insert the cable through the handle and gasket. Strip
the cable jacket to provide a workable wire length,
being mindful that the jacket must extend into the
handle to achieve a secure grip. Then strip the wires
to the lengths indicated in Table 4. When applicable
back out the terminal screws far enough (but not
completely) to allow the conductors to pass. Insert
the conductors fully into their respective terminals
and hand tighten to the torques indicated in Table 5.
For Mounted Receptacles/Inlets
Insert the cable through the wall box and cut to allow
adequate length. Strip the cable jacket to allow a
workable wire length. Strip the individual cables to
the lengths indicated on Table 4. When applicable
back out the terminal screws far enough (but not
completely) to allow the conductors to pass. Insert
the conductors fully into their respective terminals
and hand tighten to the torques indicated in Table 5.
Assemble the receptacle/inlet and the color gasket
to the box with the appropriate hardware.
Hole Pattern for Custom Mounting
In applications where custom mounting to a panel or box is
desired, the clearance and mounting holes should be drilled
as indicated in the following diagram and Table 7.
NOTICE:
In order to maintain the IP protection
provided by PN models in custom installations,
watertight seals should be used under the heads of
the four mounting bolts and they must be retained
by a lock washer and nut on the inside of the box or
panel. Alternatively, four blind holes may be drilled
and threaded to accommodate the mounting screws,
provided that the hole depth is sufficient to achieve
adequate gasket compression.
OPERATION
To ensure safe and reliable operation, Meltric
plugs and receptacles must be used in
accordance with their assigned ratings.
Meltric plugs & receptacles can only be used in conjunction
with mating receptacles or plugs manufactured by Meltric or
another licensed producer of products bearing the
TM
technology trademark.
Meltric plugs & receptacles are designed with different
keying arrangements, so that only plugs and receptacles
with compatible contact configurations and electrical
ratings will mate with each other.
Connection
To connect, open the protective plug cap, align the red dots
on the plug and receptacle bodies, insert plug into receptacle,
apply force and rotate the plug 20° counterclockwise(CCW).
The contacts will mate and the circuit will close.
Disconnection
To open the circuit and remove the plug, press the
pawl, apply inward force and rotate the plug 20°
clockwise (CW). The plug can be safely withdrawn
from the receptacle. The plug contacts remain
shrouded until after the circuit is disconnected.
Close protective plug cap to prevent contamination
by dirt, dust or other debris.
LOCKOUT PROVISIONS
The plug cap can be locked with a locking pawl
except PNHT or PN12cSS.
Screw: Plug inserted or cap closed, turn the 5/16"
screw with an Allen key until it reaches the bottom.
NOTICE:
Do not over tighten.
MAINTENANCE
Before inspecting, repairing, or
maintaining Meltric products,
disconnect electrical power to the receptacle to
eliminate the risk of electrical shock.
Meltric products require little on-going maintenance.
However, it is a good practice to periodically perform
the following general inspections:
• Check the mounting screws for tightness.
• Verify that the weight of the cable is supported
by the strain relief mechanism and not by the
terminal connections.
• Check the IP gaskets for wear and resiliency.
In wet/wash-down environments, the gaskets
should be inspected periodically (6 months) for
wear and hardness. Replace gaskets as needed.
• Verify the electrical continuity of the ground
circuit every 6 months.
• Check the contact surfaces for cleanliness and pitting.
Deposits of dust or debris can be rubbed off the
contacts with a clean cloth.
NOTICE:
Under no
circumstances should the contact surfaces be filed
since this will remove the silver-nickel, butt-contact
tip and degrade the contact consistency. Sprays
should not be used since they tend to collect dirt. If
any significant pitting of the contacts or other serious
damage is observed, the device should be replaced.
Receptacle contacts may be inspected by qualified
personnel. This should only be done with the
power disconnected. Any repair or service must be
performed with genuine Meltric parts only.
MANUFACTURER’S RESPONSIBILITY
Meltric’s responsibility is strictly limited to the repair or
replacement of any product that does not conform to
the warranty specified in the purchase contract. Meltric
shall not be liable for any penalties or consequential
damages associated with the loss of production, work,
profit or any financial loss incurred by the customer.
Meltric Corporation shall not be held liable when its
products are used in conjunction with products not
bearing the
TM
technology trademark. The use
of Meltric products in conjunction with mating devices
that are not marked with the
TM
technology
trademark shall void all warranties on the product.
GENERAL
PN Series Standard Duty plugs and receptacles
are designed to offer superior safety, durability and
consistent, electrical contact performance. Please
follow the instructions below to ensure the proper
installation, operation and maintenance of this product.
There are inherent dangers
associated with electrical
products. Failure to follow safety precautions can
result in serious injury or death. These instructions must
be followed to ensure the safe and proper installation,
operation and maintenance of the Meltric devices.
Before installation, disconnect all sources of power
to the circuit to eliminate the risk of electrical shock.
RATINGS
Meltric’s PN7, PN20 and PN30 plugs & receptacles
are listed in accordance with UL 1682, CSA 22.2
No. 182.1 and IEC 60309-1. The PN12c is listed
in accordance with IEC 60309-1. The amperage,
voltage and environmental ratings are indicated in
Table 1.
INSTALLATION
PN Series plugs and receptacles should be
installed by a qualified person in accordance
with all applicable local and national electrical
codes.
Before starting, verify that the power has been
disconnected, all product ratings are appropriate
for the application and the conductors meet code
requirements and are within the capacities of the
terminals noted in Table 2. NPT Guidelines are
detailed in Table 3.
General Notes & Precautions
1. This product must be installed by a certified
personnel.
2.
NOTICE:
Do not tin terminal wire ends.
3.
NOTICE:
Do not use moisture repellent sprays on
the contacts.
4. Do not back terminal screws fully out.
5. Self-tapping screws are provided for use with some
polymeric accessories. High torque may be
required to drive them in.
NOTICE:
Once they
are seated, care should be taken in order to avoid
over-tightening them against the plastic material.
6.
NOTICE:
Meltric threaded handles come with
tapered style threads. The use of fitting seal tape
is recommended to maintain watertightness of
all NPT fittings and joints.
7. Various handles and cord grip options may be
used. These instructions are based on handles
provided with integral multi-layer bushing cord grips.
8. If the plug and receptacle are stainless steel then
stainless steel accessories must be used.
ENVIRONMENTAL
Optimum operating conditions are achieved by installing
IP66/IP67 plugs and receptacles with the latch at the top.
NOTICE:
To prevent water ingress, non-watertight plugs/
receptacles must always face downwards when not mated.
Wire Strip Length
Wire strip lengths are indicated in Table 4. Strip
lengths for cable sheathing will depend on the
specific application. When used with handles, the
cable sheathing should extend into the handle to
ensure secure cord gripping.
Terminal Screw Tightening Torques
The wiring terminals are spring-assisted to prevent
loosening due to wire strand settlement, vibration and
thermal cycling.
NOTICE:
Avoid over-tightening. Appropriate
tools and tightening torques are indicated in Table 5.
Wiring the Terminal Connections
Verify that power has been disconnected prior to
wiring the conductors to the plug and receptacle.
Wiring must be made according to all applicable
local and national electrical codes. Check that
the rating is correct for the installation.
Follow the conductor-coding and terminal markings
detailed in Table 6.
WARNING:
This product must
be electrically grounded. A grounding terminal is
provided on all metal accessories, with a green screw
and a washer.
For Screw Type Terminals
Insert cable through handle and strip cable jacket to
adequate length. The cable jacket should extend at
least 1/2” into handle. Back out terminal screws only
far enough for conductor to clear. Strip each conductor
per Table 4. Twist the strands of each conductor
together and insert fully into the terminal. Tighten
terminal screws to torques indicated in Table 5.
PN12c Crimped/Soldered Terminal Wire Connections:
1. Strip each conductor to 25/64-inches (10-mm).
2A. For 18-16 AWG wires, insert Ferrule into contact.
2B. For 14 AWG Wires (max), the Ferrule is not required.
3. Insert stripped wire end into Ferrule or contact.
(Perform either step 4 or 5)
4A. 18-16 AWG Wires – For Crimping the Contacts,
use either North American Contact Crimping Tool
4CN30 (using crimping slot 12-10) or Crimp
contact with European Contact Crimping Tool
61-CA500 (using 4 MM slot).
4B. 14 AWG Wires – For Crimping the Contacts,
use either North American Contact Crimping Tool
4CN30 (using crimping slot 8) or Crimp contact
with European Contact Crimping Tool 61-CA500
(using 4 MM slot).
5.
NOTICE:
Soldering of the wire into the contact
must be performed with the contact out of the
Interior Insulator to prevent damage to the insulator.
• Using tin solder and a 50W soldering iron, heat
the terminal for approximately 30 seconds.
While heating, apply the soldering wire into the
hole at the bottom of the terminal and let it
penetrate by capillary action. Let it cool down
without any mechanical stress.
6. Slide the Heat Shrink Insulation Sleeve over the
contact until it butts up against the contact shoulder.
NOTE:
Sleeve must be applied.
7. With a Heat Gun that has a temperature range
of 600°F to 950°F, apply heat evenly 360°
around the sleeve until it shrinks around the
contact and wire.
Assembly of PN12c Contacts
Once wired, the contacts must be inserted into the
rear of their respective insulating block. The rear
side of the inlet/plug or receptacle/connector is
considered as the flat surface of the 4-bolt hole
mounting surface.
Assembly
Disassembly
Orientation of Inlet Assembly
Table 4 - Wire Strip Lengths – Dimension A
Receptacle Plug/Inlet
Device/Contact Inches mm Inches mm
PN20/30
3/8 10
3/8 10
PN20HT/30HT
3/8 10
3/8 10
PN7c
5/16
8
5/16 8
PN12c/PN12cSS 25/64
10
3/8 10
Table 5 - Terminal Screw Tightening Torques
Torque
Required Screwdriver
Device/Contact in-lbs N-m
or Allen Wrench
PN20/30
8 0.9 3 mm or 1/8” precision tip
PN20HT/30HT
8 0.9 3 mm or 1/8” precision tip
PN7c
8 0.9 3 mm or 1/8” precision tip
PN12c/PN12cSS - -
crimp/solder type terminals
Table 1 - General Ratings
PN12 PN7 PN20 PN30
5A 15A 20A 20A
7A 20A 30A 30A
Voltage
600VAC 600VAC 600VAC 600VAC
Frequency
50-400 Hz 50-400 Hz 50-400 Hz 50-400 Hz
Environmental
IP66+67 IP66+67 IP66/IP67 IP66/IP67
IP54/IP55 IP54/IP55
*PN20HT and PN30HT are current interrupting up to 480V only,
environmental rating is IP44.
Current
Interrupting
Non-Current
Interrupting
Table 3 - NPT Guidelines
NPT
Cable Range
.50"
.062 - 0.50
.75"
.187 - 0.75
1.00"
.437 - 1.10
1.25"
.750 - 1.375
1.50"*
.890 - 1.650
2.00"*
1.125 - 2.438
2.50"*
1.750 - 2.565
* PN12cSS only
PN20/PN30
PN20HT/PN30HT
PN7c/PN12c
OPERATING INSTRUCTIONS
A company of MARECHAL ELECTRIC GROUP
Meltric Corporation / 4765 W. Oakwood Park Drive Franklin, WI 53132
Tel. : 800 433 7642 / Fax : 414 433 2701 / e-mail : [email protected]
INSPN J
A manufacturer of products using Marechal technology
meltric
.com
INSPN J
C
A
B
B
Table 7 - Custom Mounting Dimensions
‘A’
‘B’
‘C’
Model
Inches mm Inches mm Inches mm
PN20/30
2.00
50
1.65
42
.19 5.0
PN20HT/30HT 2.00
50
1.65
42
.19 5.0
PN7c
2.00
50
1.65
42
.19 5.0
PN12c
2.00
50
1.65
42
.19 5.0
PN12cSS
2.00
50
1.65
42
.19 5.0
Table 6 - Conductor Coding and Terminal Markings
Terminal ID
Function
“G”, “E” or GND
“N”
PN20/PN30/PN20HT/PN30HT Models
“1” or “R1” (Black)
“2” or “S2” (Red)
“3” or “T3” (Blue)
PN7c/PN12c Models
“1” to “6” or
“1” or “11”
“Hot” conductors, no specific lettered ter-
minal applies to any specific colored conductor
“Hot” conductors, no specific lettered ter-
minal applies to any specific colored conductor
White or gray, system ground
(neutral conductor only “N”)
Green equipment grounding conductor
only (or green with yellow stripe).
Table 2 — Wiring Terminal Capacity* (in AWG)
Model
Wire Size Min Wire Size Max
PN/20/30
14 8
PN/20HT/30/HT 14
8
PN7c
18 10
PN12c/PN12cSS 18
14
*Capacity is based on THHN wire sizes.
Compression
Nut
Handle
Strain
Relief
Color-Coded
Gasket
Bushing
Receptacle (or Inlet)