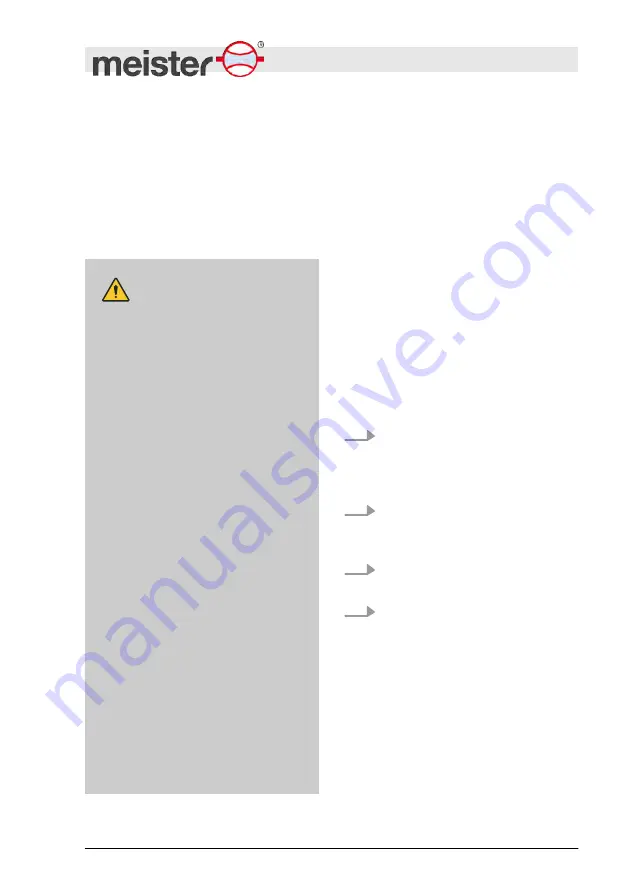
9
Disassembly and disposal
After its period of useful life, the device
must be disassembled and disposed of
in an environmentally safe manner.
9.1 Safety
WARNING!
Risk of injury if disassembled
incorrectly!
Media residue, sharp edged
components, pointed ends and
corners on and in the device or
on tools may cause injury.
–
Ensure that the site is suffi-
ciently cleared before com-
mencing work
–
Always wear protective
equipment when handling
hazardous media residue
–
Handle open, or sharp-
edged components care-
fully
–
Ensure that the workplace
is orderly and clean! Com-
ponents and tools that are
lying about or on top of
each other are potential
causes for accidents
–
Disassemble components
professionally
–
Secure components so that
they do not fall or overturn
–
If in doubt, contact the
manufacturer
9.2 Disassembly
Before disassembly:
n
Remove fluids and lubricants and
all other packaging material and
dispose of them in an environmen-
tally safe manner
Personnel:
n
Qualified personnel
Protective equipment:
n
Protective gloves
n
Goggles
1.
Remove the device from the
pipe system (
“Removal from the pipe system”
on page 56
)
2.
Disassemble the device
(
)
3.
Clean the components and
remove media residue
4.
Dispose in an environmentally
safe manner
Disassembly and disposal
Disassembly
03.09.2018
DWG Module BASICS Flow Monitor
73