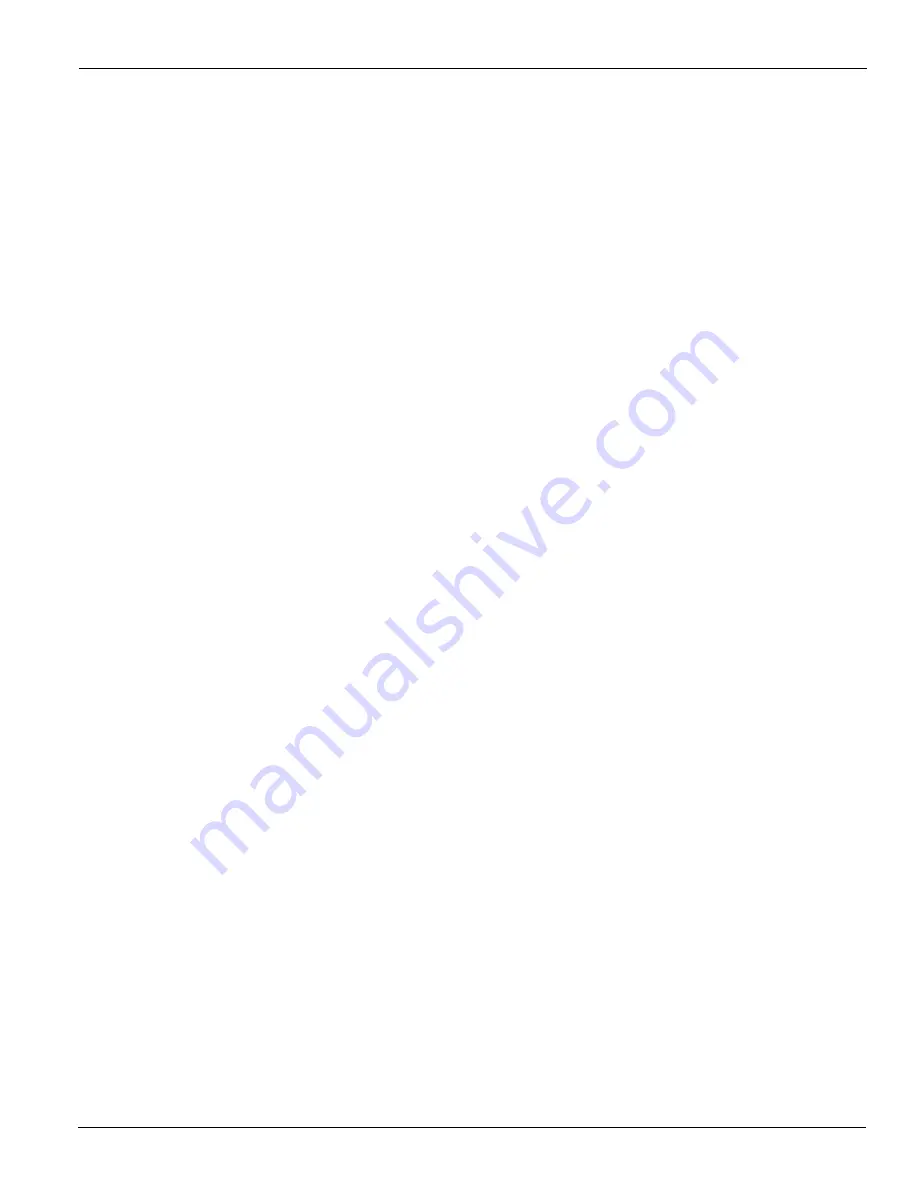
McQuay IM 777-4
11
Mechanical Installation
Steam Coils
Piping (see
Figure 19
)
•
Steam supply and steam return connections typically are
male NPT iron pipe and are labeled on the end panel of coil
section. Connections extend through the coil section end
panel.
•
When installing couplings, do not apply undue stress to the
connection extending through unit panel.
Use a backup
pipe wrench to avoid breaking the weld between coil
connection and header.
•
Support piping independently of coils and provide adequate
piping flexibility. Stresses resulting from expansion of
closely coupled piping can cause serious damage.
•
Do not reduce pipe size at the coil return connection. Carry
return connection size through the dirt pocket, making the
reduction at the branch leading to the trap.
Coils
•
Pitch all steam coils in units toward the return connection.
•
Do not drip supply mains through the coil.
•
Do not attempt to lift condensate when using modulating or
on/off control.
•
Install vacuum breakers on all applications to prevent
retaining condensate in the coil. Generally, connect the
vacuum breaker between the coil inlet and the return main.
The vacuum breaker should be open to the atmosphere and
the trap design should allow venting of large quantities of
air.
Traps
Note:
Do not place steam traps outdoors.
•
Size traps in accordance with the manufacturers’
recommendations. Make sure the required pressure
differential is always available.
Do not undersize.
•
Use float and thermostatic or bucket traps for low pressure
steam. On high pressure steam, use bucket traps. Use
thermostatic traps only for air venting.
•
Use bucket traps for on/off control only.
•
Locate traps at least 12 inches below the coil return
connection.
•
Multiple coil installation—individually trap each coil or
group of coils.
•
Coils in series—use separate traps for each coil, or a bank of
coils.
•
Coils in parallel—a single trap can be used, but an individual
trap for each coil is preferred.
•
Do not attempt to lift condensate when using modulating or
on/off control.
•
With coils arranged for series airflow, use a separate control
on each bank or coil in the direction of airflow.
Valves
•
Do not use modulating steam valves on high pressure
systems.
•
Properly size modulating valves.
Do not undersize
.
•
Avoid freezing conditions (entering air temperatures below
35°F).
•
McQuay strongly recommends 5JA, 8JA, 5RA and 8RA
coils.
•
Supply 5 psi steam to coils at all times.
•
Do not use modulating valves. Provide control by face and
bypass dampers.
•
Consider using two or three coils in series with two position
steam control valves on the coil or coils that handle 35°F or
colder air. Use a modulating valve on the downstream coil to
provide the desired degree of control.
•
Thoroughly mix fresh air and return air before it enters the
coil. Also, to obtain true air mixture temperatures, properly
locate temperature control elements.
•
As additional protection against freeze-up, install the trap
sufficiently below the coil to provide an adequate
hydrostatic head to remove condensate during an
interruption in the steam pressure. Estimate three feet for
each 1 psi of trap differential required.
•
On startup, admit steam to coil ten minutes before admitting
outdoor air.
•
Close fresh air dampers if steam supply pressure falls below
the minimum specified.