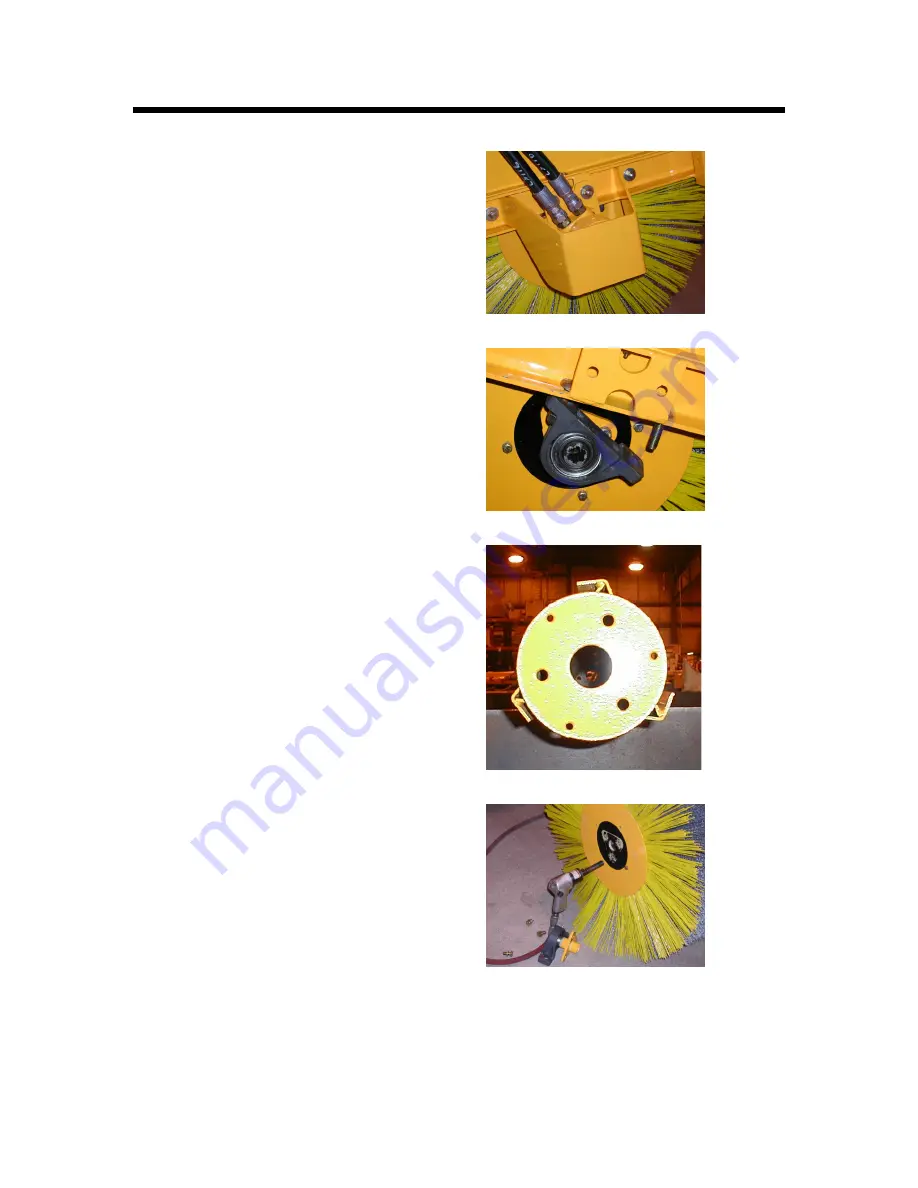
Copyright 2004 M-B Companies, Inc.
All Rights Reserved
11
Maintenance
FILLER REPLACEMENT
CORE REMOVAL
•
Lower broom until brush contacts the ground via
hydraulic lift cylinder or mechanical head anchor.
•
Remove bolts attaching motor guard to the brush
frame. Remove guard and set aside.
•
Remove (2) ½” bolts attaching motor mount plate to
the brush frame. Slide motor out of mating splined
hub. Let motor hang on hoses.
•
Remove hardware holding pillow block bearing to
bottom of brush frame. Complete steps 2 thru 4 on
both ends of core.
•
Slide core out the front of broom.
BRUSH REMOVAL
•
Remove (3) ½” bolts attaching splined hub to end of
core. Remove hub and set aside.
•
Remove (3) or (4) bolts attaching wafer retainer plate
(end disc) to end of core. Set retainer and hardware
aside.
•
Slide spent filler and spacers off core and discard.
BRUSH INSTALLATION
•
Stand core in upright position and begin filling the
core by sliding an individual segment and spacer
down the full length of the core starting with a poly
segment. Note the location of the drive pin on the
inside ring of each segment. Be sure to rotate each
segment so the position of the pin is on a different
side of the core with each segment being installed.
This will help to insure proper balance on the core.
•
Continue stacking the core in a segment-spacer,
segment-spacer configuration until it is full ending
with a segment. Always start and finish with a poly
segment.
•
The last segment should actually extend beyond the
end of the core (Minimum ½”) so when the end disc is
installed it compresses the filler onto the core when
the bolts are tightened.
•
Install end disc to the end of the core and secure with
original bolts.
•
Reinstall splined hub and bearing.
CORE INSTALLATION
•
Position refilled core in front of the broom head. Lift
the broom head high enough to place the filled core
back into its original position. Once in place, lower
broom head down onto the pillow block bearing at
each end of the core.
•
Reverse steps 2 – 4 from core removal section to
complete reinstallation. Note: Apply grease or anti-
seize to splines before installing hydraulic motors.
•
Before placing machine back into service, adjust and
test for proper amount of brush pattern. Excessive
pattern can cause brush failure or premature wear.