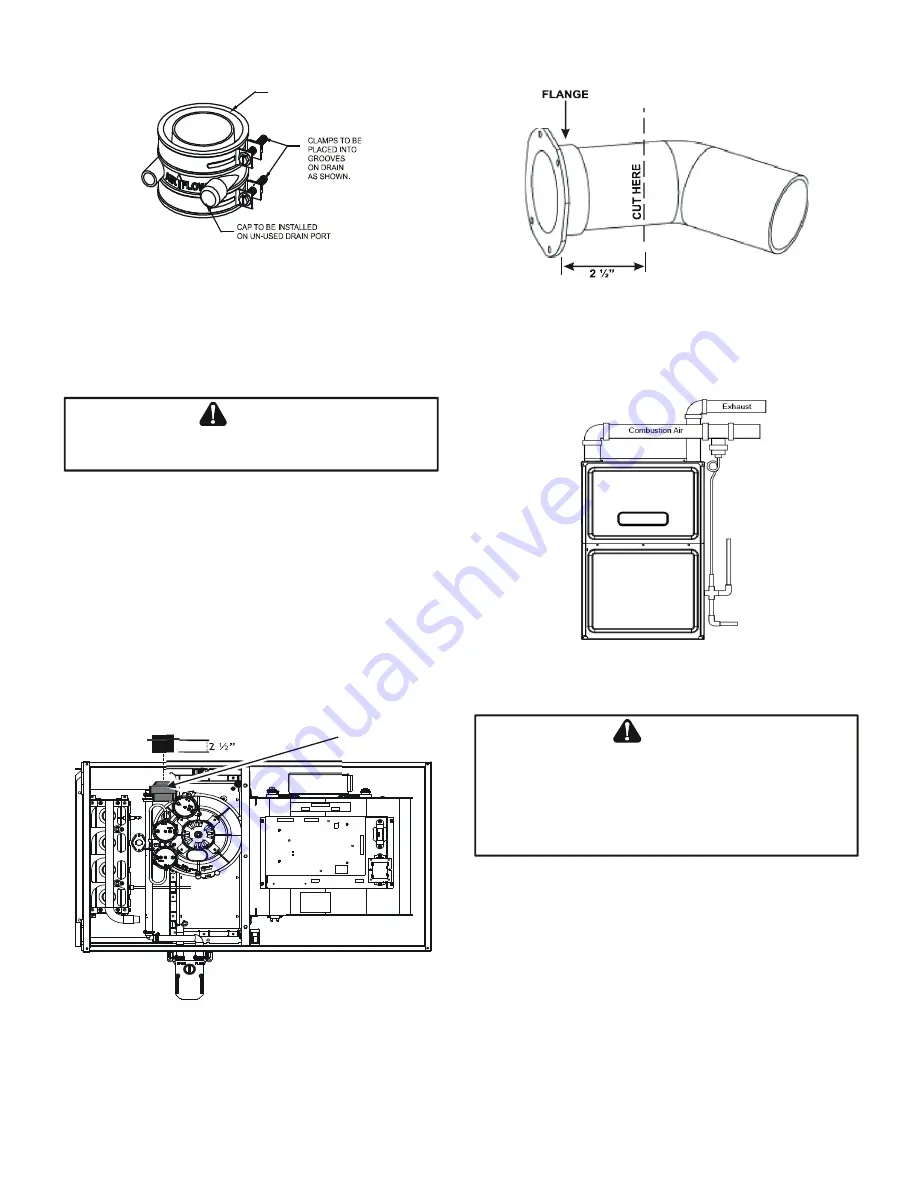
SYSTEM OPERATION
16
VENT-DRAIN
Figure 8
NOTE:
For
non-direct vent
installations, a minimum of one
90° elbow should be installed on the combustion air intake
coupling to guard against inadvertent blockage.
COMBUSTION AIR PIPE
Direct Vent Installations
E
DGES
OF
SHEET
METAL
HOLES
MAY
BE
SHARP
. U
SE
GLOVES
AS
A
PRECAUTION
WHEN
REMOVING
HOLE
PLUGS
.
WARNING
On
upflow
units secure the combustion air intake pipe to
the air intake coupling by using a take apart rubber coupling
supplied with the furnace or a plastic coupling. Also, the in
-
take coupling may be inverted to allow the intake pipe to be
glued directly to it. After inverting the coupling, secure it to
the furnace top with screws. On
counterflow
units secure the
combustion air intake pipe to the air intake coupling using the
rubber coupling and worm gear hose clamps provided with the
unit. The counterflow rubber coupling allows service removal
of air intake piping internal to the furnace blower compartment.
The combustion air intake pipe can also be secured directly
to the counterflow unit air intake pipe coupling.
Insert flange. Cut 2 ½” long.
Figure 9
RF000142
Figure 10
Figure 9B
T
HE
RUBBER
ELBOW
IS
NOT
DESIGNED
TO
SUPPORT
A
LOAD
. W
HEN
THE
RUBBER
ELBOW
IS
MOUNTED
EXTERNALLY
TO
THE
FURNACE
CABINET
,
EXTREME
CARE
MUST
BE
TAKEN
TO
ADEQUATELY
SUPPORT
FIELD
-
SUPPLIED
VENT
/
FLUE
PIPING
,
AS
DAMAGE
CAN
RESULT
IN
LEAKS
CAUSING
BODILY
INJURY
OR
DEATH
DUE
TO
EXPOSURE
TO
FLUE
GASES
,
INCLUDING
CARBON
MONOXIDE
WARNING
COMBUSTION AIR INTAKE OPTIONS:
The RF000142 cou
-
pling can be secured directly to the furnace intake coupling
if condensation is a concern. If the RF000142 is used on the
combustion air inlet, it must be installed with the arrow point
-
ing up. It should be noted, the combustion air will actually be
moving in a direction opposite of the arrow on the RF000142
coupling. It must have a field supplied, trapped drain tube
free-draining to proper condensate disposal location. A loop
in the drain tube can serve as a trap. The unused RF000142
drain fitting should be capped. A tee installed in the intake
pipe is also an acceptable method of catching condensation.
It must have a field supplied, trapped drain tube or pipe,
free-draining to proper condensate disposal location. A loop
in the drain tube can serve as a trap. (See Figure 9B)