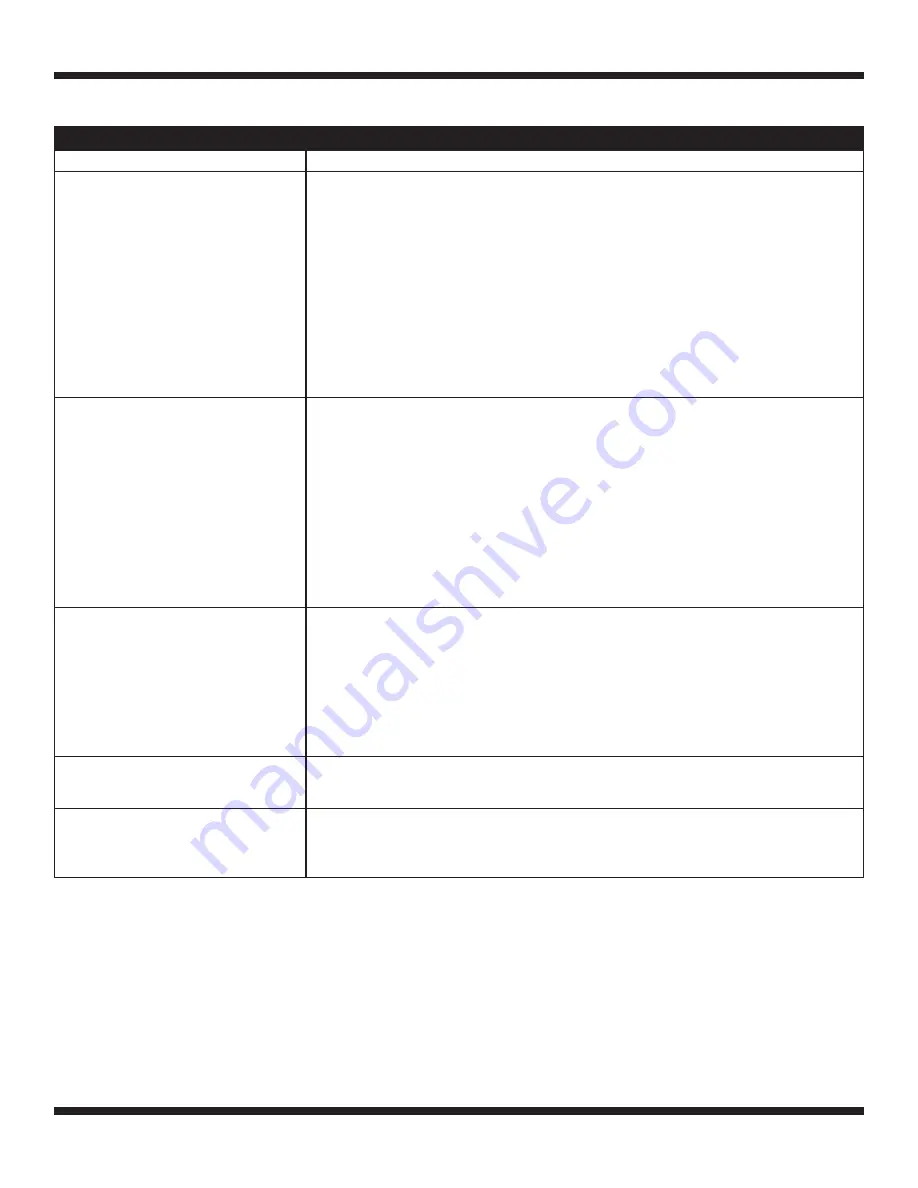
FOR SERVICE TECHNICIAN ONLY - DO NOT REMOVE OR DESTROY
PART NO. W10340707A
PAGE 16
03/11
PROBLEM
POSSIBLE CAUSE/TEST
NOTE:
Possible Cause/Tests must be performed in the sequence shown for each problem.
BLANK DISPLAY
Possible Causes
– UIC not powered or no power to the washer.
– Wrong communication between CCU and UIC.
Procedure for UIC not powered
1. Check that the washer is plugged into a working outlet.
2. Unplug washer or disconnect power.
3. Check continuity from the power cord to the line filter.
4. Check continuity from the line filter to the transformer.
5. Perform Ohm meter test to the transformer (page 14).
Procedure for wrong communication
1. Unplug the washer or disconnect power.
2. Wait for 2 minutes.
3. Reconnect power.
If the display fails to turn on, replace the UIC.
TOUCH-PADS DO NOT RESPOND
Possible Causes
WHEN PRESSED
– Keypad ribbon disconnected, damaged, or contaminated.
– Door switch disconnected, loose, or damaged.
Procedure if matrix key board is disconnected
In this error, the keypad does not respond in any mode (normal operation, set-up, etc.)
1. Unplug washer or disconnect power.
2. Check that the keypad ribbon is connected to the UIC.
3. Clean the matrix keypad of soap or other residues.
4. Verify the function of the keypad. If it fails to operate, replace it.
Procedure if door switch is disconnected
In this error, the keypad works normally in set-up mode, but will not start a user paid cycle.
1. Verify door switch operation by performing test for F26 error code (page 7), even if the F26 code is not displayed.
If the above procedures fail to solve the problem, replace the UIC.
WASHER VIBRATES
1. Verify that the washer is level.
2. Verify that the shipping system, including shipping bolts and spacers, is removed, and that the power cord
is not tangled in any components inside the rear of the washer.
3. Verify that the leveling legs are locked into place and firmly in contact with the floor.
4. Check for unbalanced loads, especially when washing very small loads.
5. Verify that dampeners are all connected in place and not damaged.
6. Correct any twists in the door bellows.
7. Verify proper drive belt placement on motor pulley.
8. Make sure that the washer is not installed on a wooden riser with a platform less than 3/4 inches thick.
DRUM WON’T ROTATE
1. Check for broken drive belt.
2. Check for drive motor failure error codes (F11, F25, F28).
3. Make sure that the door locks properly.
INCORRECT WATER TEMPERATURE
1. Make sure that the inlet hoses are connected properly.
2. Check the water temperature sensor for an abnormal condition (page 14).
3. Verify hot and cold water operation in Quick Overview Test in diagnostic mode.
4. Check for blocked filter screen in inlet valves.
TROUBLESHOOTING GUIDE