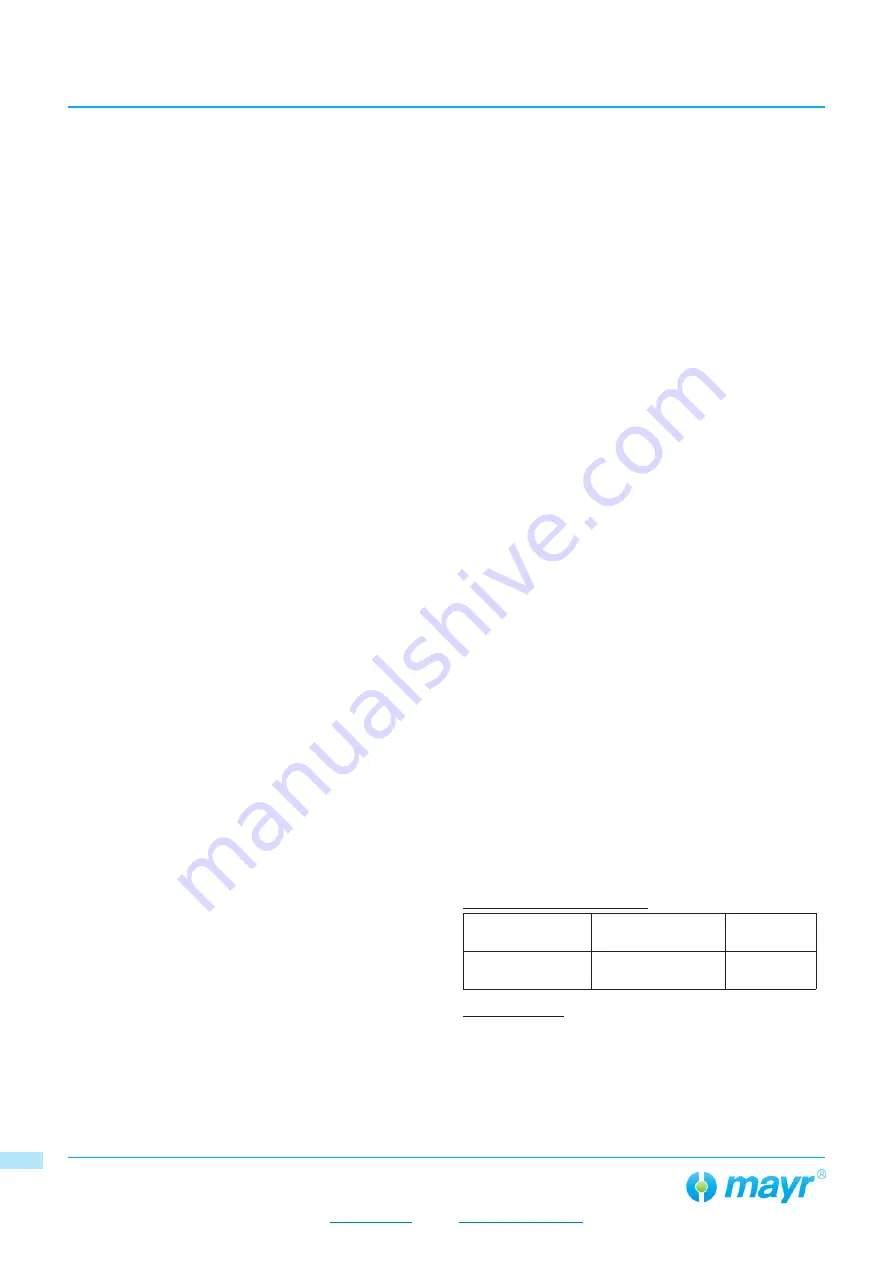
Installation and Operational Instructions for
ROBA
®
-brake-checker plus DC Type 028.700.2
(B.0287002.EN)
your reliable partner
25/02/2022 HH/GF
Page 8 of 11
Chr. Mayr GmbH + Co. KG
Eichenstraße 1, D-87665 Mauerstetten, Germany
Tel.: +49 8341 804-0, Fax: +49 8341 804-421
www.mayr.com
, E-Mail:
88
Voltage reduction mechanism
After a brake-specific overexcitation time period, the intel-
ligent voltage reduction mechanism mechanism mode ad-
justs to the pre-set holding voltage. Manual adjustment of
the overexcitation time is not necessary.
Continuous drop-out recognition
The continuous drop-out recognition can detect the follow-
ing situation and signal it via the outputs:
Brake is energised --> Undesired movement of the armature
disk for closing the brake (drop-out of the armature disk).
Changes of the output signals:
Control terminal
16:
OUT (0.99 × U
I
)
--> 0 VDC
Control terminal
15:
ERR (0.99 × U
I
)
--> 0 VDC
Possible Causes
• Excessive temperature
• Marginal dimensioning
• Mechanical influences
Release Monitoring
The release monitoring recognises the movement of the ar-
mature disk for opening the brake after switch-on as well
as the movement of the armature disk for closing the brake
after switch-off.
The release monitoring can be deactivated for certain appli-
cations in order to prevent errors.
Possible applications:
•
Parallel operation of several brakes
•
Damped brakes
•
Unspecific brakes
Switch-OFF
Fast switch-off
If short engagement times are desired, fast switching should
be used (FAST).
Here, the ROBA
®
-brake-checker monitoring module limits
the switch-off voltage to approx. 60 VDC.
DC-side disconnection is signalized by the red light-emitting
diode flashing at the moment of switch-off.
Optional (customer-side)
External fast switch off
A single-pole energy separation can be achieved by means
of an external switch contact (see wiring example) (tried and
tested principle according to ISO 13849-2). Depending on
the required PL and category, the control element may have
to be designed redundantly in accordance with ISO 13849-1.
Failure detection and corresponding diagnostic coverage
(ISO 13849-1) can be achieved by the following design of
the external switch:
• Feedback with positively driven contacts
• Mirror contacts
The monitoring functions are retained!
Series connection of the isolating contacts at a contact
opening of ≥3mm increases reliability and lifetime.
Slow switch-off
If longer engagement times or
quieter switching noises
are desired, slow switching should be used (SLOW) (factory
setting).
Switch-ON
Brake switch-on occurs with a connected supply voltage
(control
and power terminal) by closing start (Input) on the
signal side using the voltage 24 VDC
or a 24 VDC control
signal applied there. A green light-emitting diode emits a
signal when the device is switched on. After the changeover
from overexcitation voltage to holding voltage, the diode
continues to illuminate at reduced brightness.
Functional Guidelines
Start process
During each individual start process, all outputs (signal,
error, warning) are reset.
The outputs must be assessed for the plausibility of signal
conditions, signal changes and their correct temporal
sequence.
Inching Mode
During inching mode (fast sequence of switching on and
off), no reliable detection is possible.
After the end of inching mode, restart the monitoring
function:
• De-energise the brake
• Switch on (energise) the brake again
Repeated switch-on (energisation) before the brake is closed
generates a fault when the maximum current is reached.
88