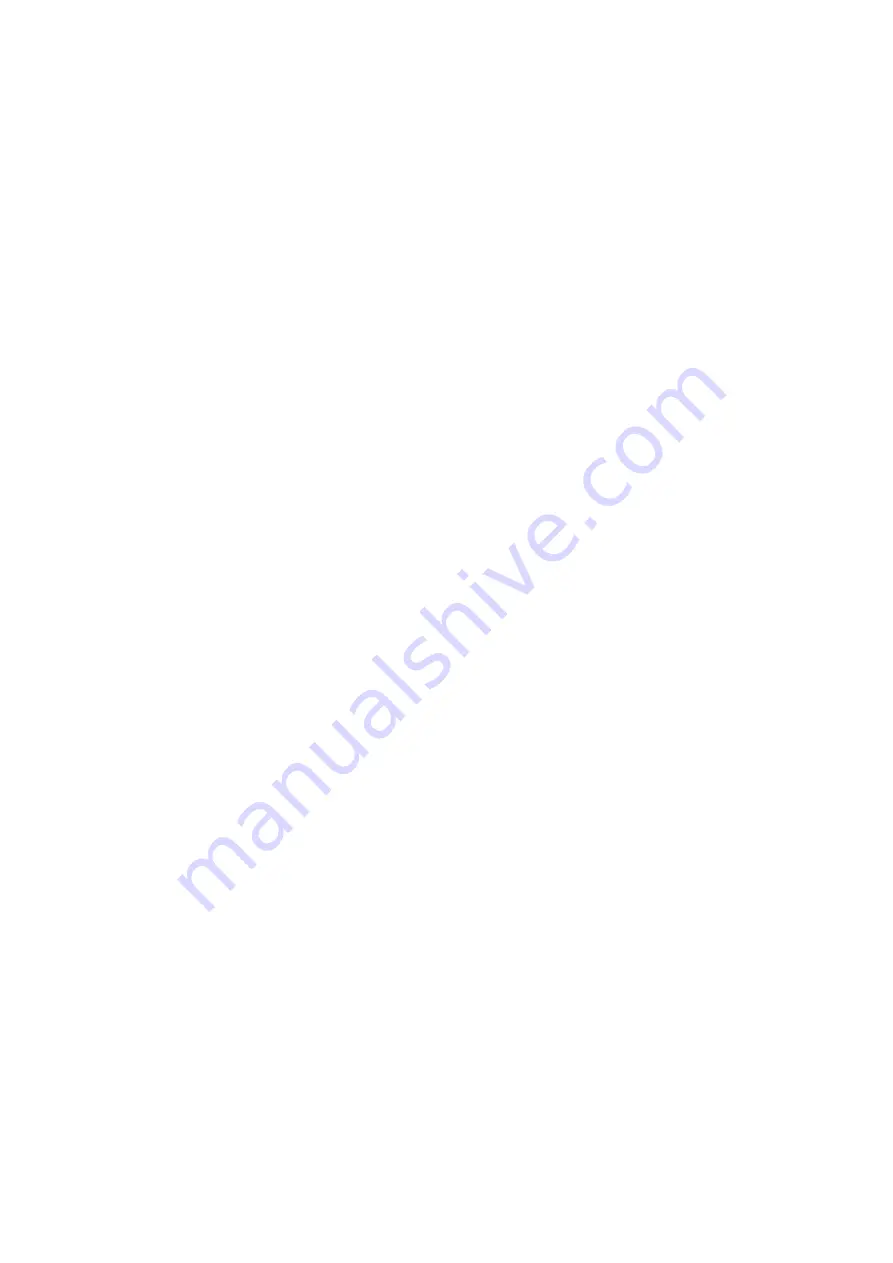
5.2
Replacement of servovalve sealings
Depressurise the pump and disconnect all tube connections from the pump.
Loosen the bolted union at the pipeline (Item 45).
Loosen the 8 hexagon bolts and disassemble the covers of the servovalve
(Item 30 and 40).
Draw out the servovalve (Item31) and disassemble the O-rings (Item 33,38
and 39).
Use a mandrel (PTFE or wood) to force out the servovalve runner (Item 35)
and remove the O-rings (Item 34).
Treat all sealing and guiding elements with a resin- and acid-free grease. Re-
assembly is performed in reverse order than disassembly.
5.3
Sealing replacement at the drive side
Depressurise the pump and disconnect all tube connections from the pump.
Disassemble the union nut (Item 18) and the pipe (Item 19).
Loosen and remove the 4 hexagon nuts (Item 28).
Disassemble the pipeline (Item 45) and the hexagon bolts (Item 29 and 46).
Disassemble the pipelines (Item 58 and 79) from the top and bottom caps.
Now the top cap (Item 26) and the air cylinder (Item 22) can be drawn off.
Treat all sealing and guiding elements with a resin- and acid-free grease. Re-
assembly is performed in reverse order than disassembly.