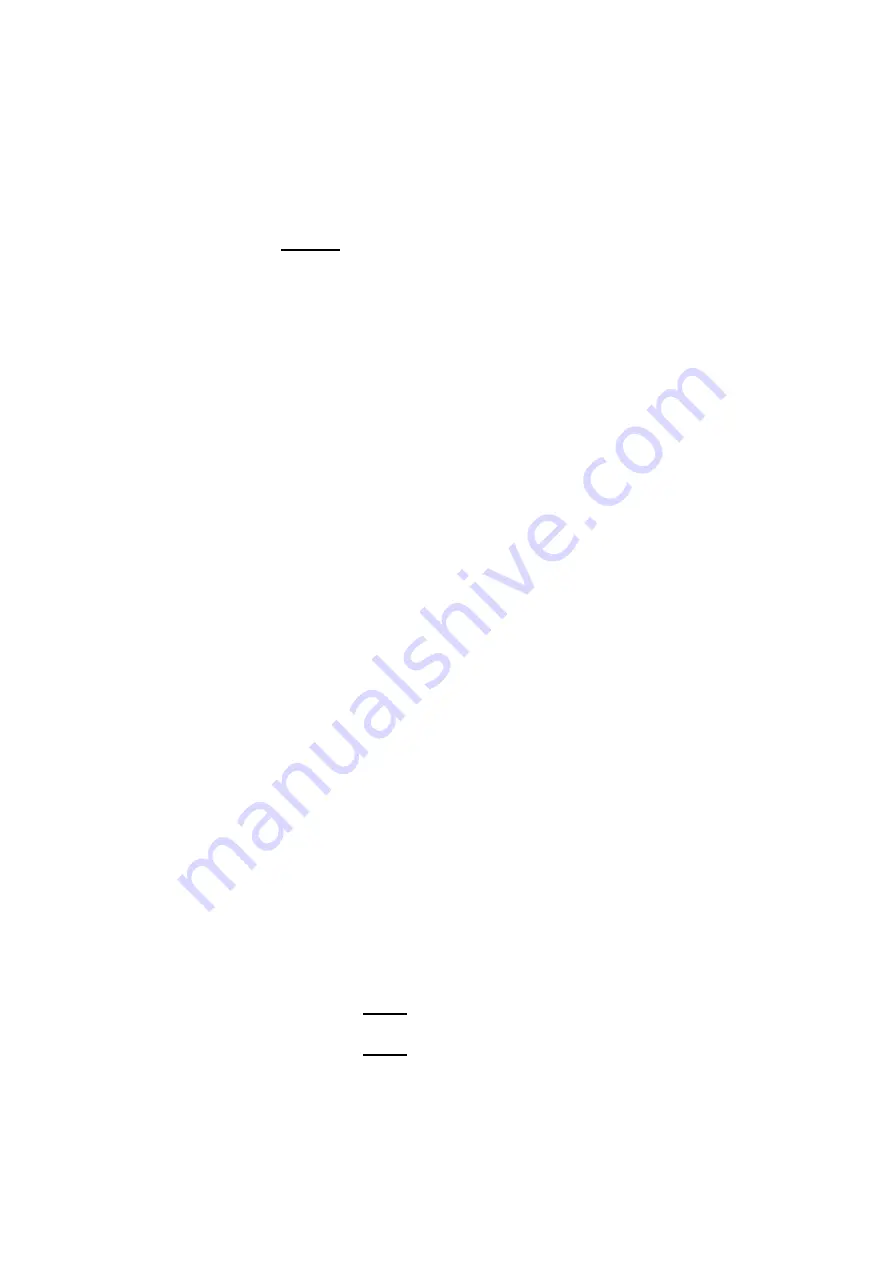
MAX POWER
It may be necessary to readjust the slide bar height so that the Bar engages
automatically or so that the bar is not loose when the thruster closes. This is done as
follows
Loosen the two bolts holding the locking slide guide (F on drawing N°4) and adjust its
height by using 19 mm bolt (G).
Correct adjustment has been obtained when Bar engages
automatically with a
sharp snap,
and you
cannot pass
a 0.1mm feeler gauge between the locking cam
and the locking bar. This adjustment must be achieved with the Up down unit set no
higher than 40 bars.
When correct adjustment has been obtained re-tighten the guide’s bolts (F).
RAISE / LOWER POWER PACK INSTALLATION
The raise/lower unit should be near the RETRACT unit. It should be installed in a
readily accessible and dry place.
It should be connected to the control box with 2 x 6 mm² cable for the motor power
and 3 x 1 mm² for the up down spool valves. The up / down unit motor is protected by
a 16ah fuse found in the control box.
The hydraulic ports (LA and LB) on the raise/lower pump unit and the raise/lower ram
(VA and VB) must be connected A to A and B to B.
The flexible hoses must be 3/16
″
or 1/4
″
with an operating pressure rating of at least
100 bars.
CAUTION: to prevent the risk of electrical earth leakage’s, the hydraulic hoses
connected directly to the RETRACT should be non-conductive (non-metal braided
hose) high-pressure thermoplastic hose.
Absolute internal cleanliness is
essential
. After pipes and hoses have been equipped with their fittings, they must be
blown out with compressed air, and then plugged until connected.
The pressure limiter on the unit is pre set and should need no adjustment!
If adjustment is needed always use the minimum pressure needed & do not exceed
75 bar.
Do not forget that the unit runs constantly when the thruster is thrusting. It is
therefore when thrusting (in particular to stbd) that the maximum pressure can be
read.
TRANSMISSION LUBE OIL TANK INSTALLATION
The transmission lube oil tank is no longer used on retract series units.
HYDRAULIC POWER SYSTEM INSTALLATION
Hydraulic power system general
A RETRACT R450/40 Can take
up to
110 LPM of hydraulic flow this will causes on a
normal installation approximately 210 bar pressure at the thrusters inlet ports.
A RETRACT R450/50 Can take
up to
170 LPM of hydraulic flow this will causes on a
normal installation approximately 170 bar pressure at the thrusters inlet ports.
The hydraulic power system should be designed in consequence.
The hydraulic power system must start the thruster gently (soft start) either by using
a ramping valve or by using a 2-stage slow/fast speed bypass system.
- 8 INSTALLATION MANUAL RETRACT R 450