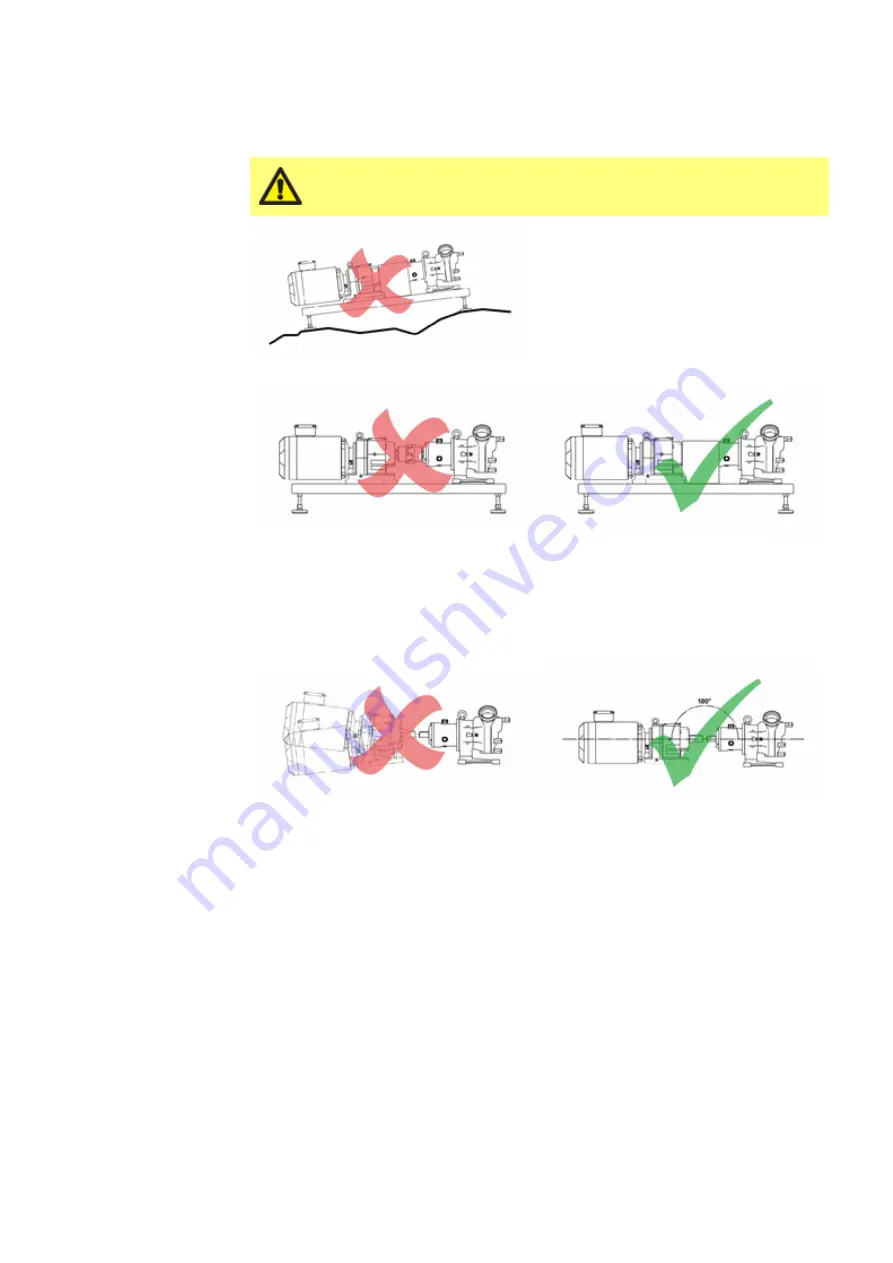
12
Good pump installation practice
The motor shaft and pump shaft connection must be guarded to protect the user
from contact, when in use.
l
Place the pump on a level surface
l
Do not start the pump without a coupling guard to protect the user from contact.
l
The mounting surface should be strong enough to support the pump.
l
There should be sufficient space for maintenance work around the pump.
l
The motor must receive an adequate air supply.
l
The unit must be protected against static charge.
l
Ensure the front housing is accessible for easy maintenance.
l
Align the pump shaft with the drive shaft.
;
12.1 Dos and don'ts
l
Do not build a pump into a tight location without adequate airflow around the pump.
l
Do not pump any chemical not compatible with the materials of the pumphead.
l
Do keep delivery and suction pipes as short and direct as possible - though ideally not shorter than
one metre - and follow the straightest route. Use bends of large radius: at least four times the pipe
diameter. Ensure that connecting pipework and fittings are suitably rated to handle the predicted
pipeline pressure. Avoid pipe reducers and lengths of smaller bore pipe than the pumphead section,
particularly in pipelines on the suction side. Any valves in the pipeline must not restrict the flow. Any
valves in the flow line must be open when the pump is running.
l
Do use suction and delivery pipes equal to or larger than the nozzle diameter bore.
l
Do site the pump at or just below the level of the fluid to be pumped if possible. This will ensure
flooded suction and maximum pumping efficiency.
l
Valves in the process flow must be opened before the pump operates. Users are advised to fit a
pressure relief device between the pump and any valve on the discharge side of the pump to protect
against damage caused by accidental operation with the discharge valve closed.
m-certa800-en-01
13
Содержание Certa 100
Страница 41: ...20 1 Pumps m certa800 en 01 41 ...