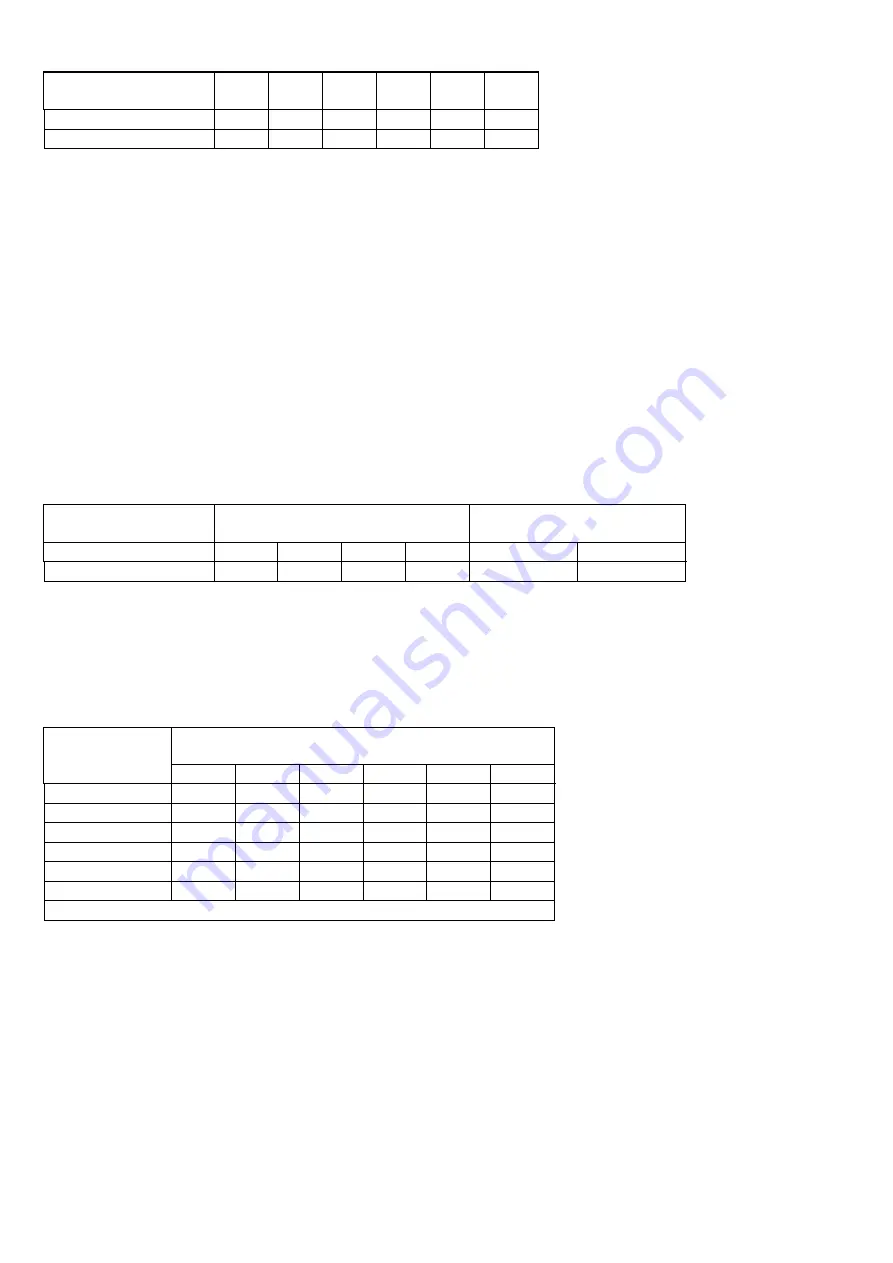
-5- 55008386-05
All dimensions are in millimetres.
Model
A
B
C
D
E
Weight
(kg)
MCU+ 180
1100
1215
675
211
95
118
MCU+ 200
1100
1215
675
211
95
173
APPLICATION - ALL CONDENSING UNITS
1. To maximise performance, pipe runs should be kept as short as possible, avoiding sharp bends. However, individual
pipe runs to a maximum of 45m, including 20m lift, are permissible provided good refrigeration practice is followed.
Published performance duties are based on 7.5m pipe runs. Correctly sized pipes for each installation, and fitting the
correct thermal expansion valve will result in no significant loss of capacity on extended pipe runs.
a) Pipe sizes are based on:-
Minimum of 3.8 m/s (750 fpm) suction gas velocity for horizontal or downflow.
Minimum of 7.6 m/s (1500 fpm) suction gas velocity for upflow.
Maximum of 15.2 m/s (3000 fpm) suction gas.
b) Where vertical risers exceed 3m, oil traps must be formed in the pipe. This will help ensure that oil returns to
the compressor. Typically fit an oil trap every 3m with a trap at the bottom of the riser.
2. The maximum pipe lengths to be used for each pipe size and outdoor unit are shown in the table opposite. Use of
these sizes and lengths is recommended in order to achieve optimum system performance
SUCTION LINE SIZE
LIQUID LINE SIZE
MCU+
0 - 6M
6 - 15M
15 - 21M
21 - 45M
0 - 21M
21 - 45M
180 - 200
7/8
1 - 1/8
1 - 1/8
1 - 3/8
1/2
5/8
3.
In calculating equivalent lengths of pipe runs, the effect of bends and fittings must be taken into account. Information
relating to the equivalent lengths of line fittings and bends etc is generally available to the design engineer. The table
below covers the fittings most likely to be encountered in this type of installation. The equivalent lengths of all the
fittings in a particular pipe run must be added together and the total added to the actual length of pipe in the run, in
order to calculate its total equivalent length.
FITTING
PIPE SIZE (OUTSIDE DIAMETER IN INCHES)
3/8
1/2
5/8
3/4
7/8
1 - 1/8
45° BEND
0.12
0.15
0.18
0.21
0.24
0.3
90° BEND R/D = 1
0.37
0.43
0.49
0.55
0.61
0.79
90° BEND R/D = 2
0.24
0.27
0.30
0.37
0.43
0.52
180° BEND C/D = 1
0.73
0.91
1.10
1.28
1.46
1.83
180° BEND C/D = 2
0.46
0.55
0.64
0.76
0.85
1.07
90° ELBOW
0.67
0.85
1.04
1.25
1.46
1.89
R = RADIUS OF BEND D = DIAMETER OF TUBE C = CENTRES OF BEND
4.
Use the shortest possible route, avoiding sharp bends.
5.
Fully insulate the suction line, (or suction and liquid line if run together).