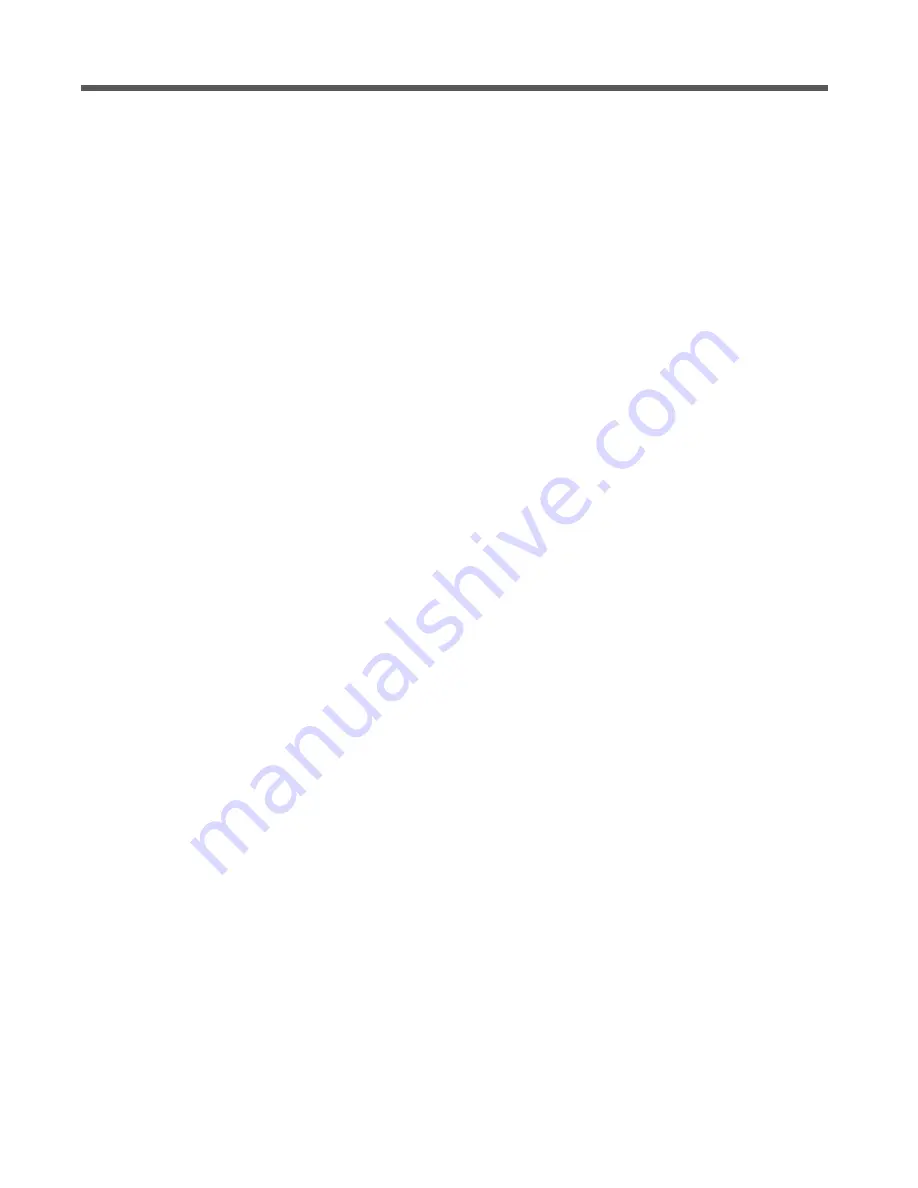
9
parts list
1
Complete Geareducer Assembly
100 Spiral Bevel Gear Set
101 Set of matched spiral bevel gears including
integral pinion shaft with key
Gear ratios as follows:
2.304 to 1
2.435 to 1
2.762 to 1
3.158 to 1
3.167 to 1
3.944 to 1
102 Oil slinger
103 Locknuts
104 Lockwasher
105 Pinion shaft key
106 Interstage shaft key
108 Ring gear spacer (2.304 and 2.435 gear
sets only)
200 Helical Gear Set
201 Set of matched helical gears including
interstage shaft and special key
Gear ratios as follows:
4.18 to 1
4.70 to 1
5.00 to 1
202 Top interstage bearing retainer disc
203 Bottom interstage bearing retainer disc
204 Place bolts and washers
205 Place bolts and washers
206 Place bolts and washers
300 Fan Shaft Assembly
301 Fan shaft
302 Key
303 Fan hub retainer
304 Cap screw
305 Locking plates
306 Retainer ring
307 Key
400 Pinion Shaft Bearing Set
401 Tail, tapered roller bearing
402 Head, tapered roller bearing
410 Interstage Bearing Set
411 Lower, double row, tapered roller bearing.
Matched assembly with cone spacer
412 Upper, double row, tapered roller bearing.
Matched assembly with cup spacer
420 Fan Shaft Bearing Set
421 Lower tapered roller bearing
422 Upper tapered roller bearing
500 Shim set
501-502-503 Pinion shaft shims
504-505-506 Interstage shaft shims
507-508-509 Fan shaft shims
600 Gasket Set
602 Inspection cover gasket
603 Oil trough gasket
700 O-Rings Set.
702 Pinion cage O-ring, 9
3
⁄
4
" ID x 10
"
OD x
1
⁄
8
"
703 Water slinger O-ring, 6
1
⁄
2
" ID x 6
3
⁄
4
" OD x
1
⁄
8
"
704 Interstage cap bolt O-rings,
1
⁄
2
" ID x
5
⁄
8
" OD x
1
⁄
16
"
701* Pinion shaft oil seal
705* Water slinger seal wear sleeve
706* Fan shaft seal
*Geareducers prior to 2013 utilize a lip type oil seal.
Current geareducer models utilize an Inpro/Seal
®
bearing isolator.
*Geareducers prior to 2013 do not utilize a water slinger
wear sleeve and fan shaft seal items (705) and (70
6).
Содержание Geareducer 3600
Страница 17: ...17 ...