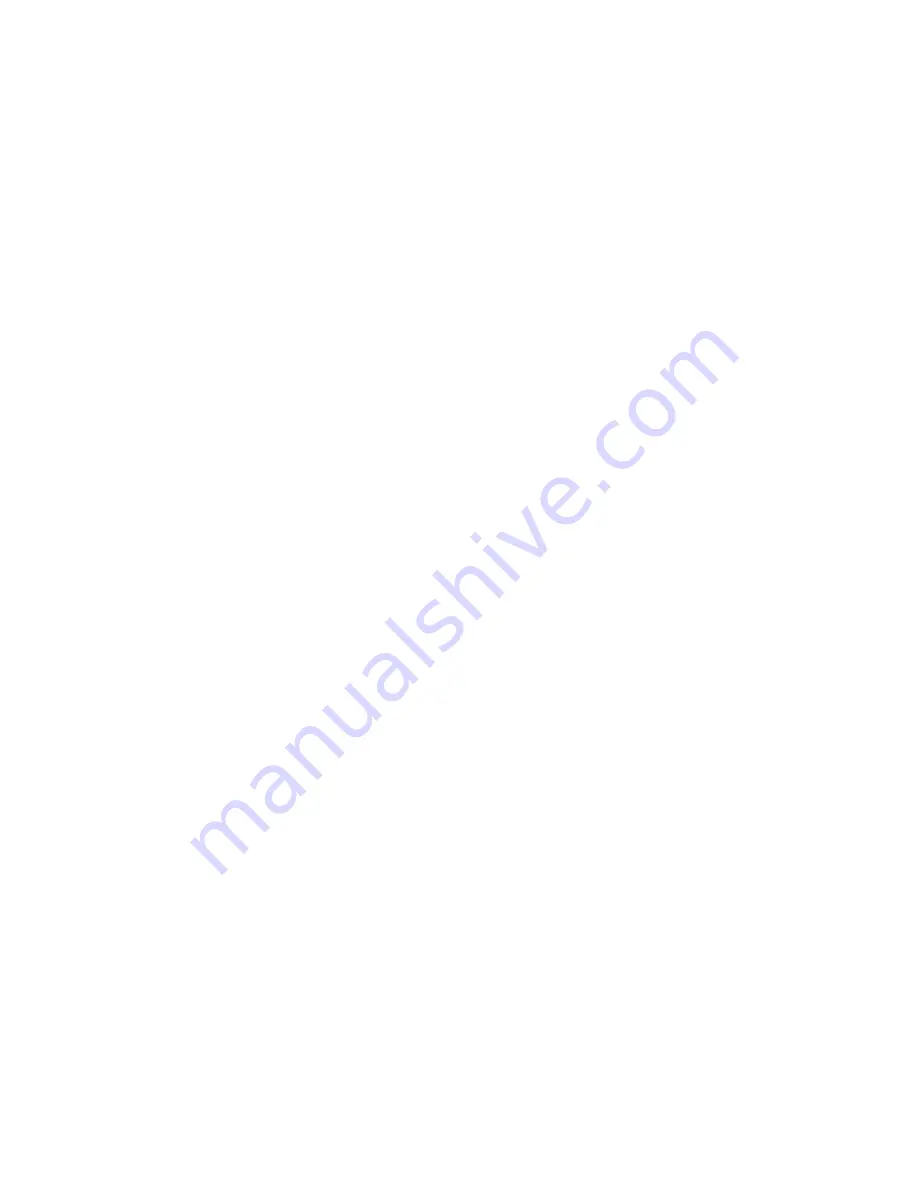
– 6 –
ASSEMBLY
Before assembling a new pinion gear in the pinion cage, check
match numbers on pinion gear and spiral bevel ring gear to be
certain that they are a matched set. Gears are lapped in
matched sets at the factory and should not be separated.
Numbers are etched on both the pinion and ring gear as
illustrated in Fig. 1, page 2.
All parts that are to be reused should be thoroughly cleaned
with Kerosene before being reinstalled. Do not remove new
bearings from carton until ready to use. Wash all bearings (new
or old) with Kerosene. Do not spin-dry bearings. Take each
bearing set and roll the cup on the cone to note any roughness.
Replace bearing if necessary. If bearings cannot be installed
immediately after washing, lubricate and cover them to protect
against dust, moisture, etc.
If a press is not available to install bearing cones, they can be
heated as long as the temperature does not exceed 275
°
-
300
°
F. If the bearings get hotter than this, they will begin to
draw and soften. Bearings can be heated with infrared lamps
or with oil baths. If an oil bath is used, the bearing should be
supported an inch or so above the pan to prevent local
overheating.
PINION CAGE SUB-ASSEMBLY
1.
Place oil slinger (Item 2.11) on pinion shaft (Item 2.9).
2.
Press head bearing cone (Item 2.12) on pinion shaft
making sure oil slinger and bearing are against gear.
3.
Press bearing cups (Items 2.13 and 2.14) into pinion cage
(Item 2.4).
4.
Lower pinion cage on pinion shaft, until head bearing cone
and cup mate.
5.
Press tail bearing cone (Item 2.10) on pinion shaft until it
mates with its bearing cup.
6.
Install locknuts (Item 2.7) and lockwasher (Item 2.8).
Tighten nuts on bearing cone until 5 to 15 inch pounds of
bearing preload is obtained. Bearing preload is the resis-
tance in the bearings to shaft rotation measured in in./lbs.
torque required to rotate the shaft at uniform velocity.
Preload is necessary to insure the stability of the gear
engagement. Crimp the lockwasher to hold the two nuts
in place.
7.
Install “O” ring (Item 2.6) in groove.
8.
Install oil retainer (Item 2.15) in pinion cage cap (Item 2.2).
This seal is to prevent oil leaking out of the Geareducer;
therefore, the sealing lip must point inward. Clean oil
retainer seat in cap and press retainer in place. Use a
short piece of pipe with outside diameter .010 to .020 in.
Iess than the retainer outside diameter. Do not apply
hammer blows or uneven pressure directly to seal sur-
face. Be careful not to tip retainer while installing it.
Provide a sleeve to protect the seal lip as it passes over
the shaft keyway. Shim stock .010 to .015 inch thick can
be used for this sleeve as long as the lapping edge is
smoothed off and the seal is turned with the lap in the
sleeve rather than against it. A small amount of light
grease can be used to lubricate the sealing lip.
9.
Position “O” ring (Item 2.5) and push cap (Item 2.2) (with
seal and sleeve) in place on shaft. Attach cap to pinion
cage and slide sleeve from cap.
10. Record the pinion setting distance that is etched on the
pinion gear.
INSTALLATION OF FAN SHAFT
1.
Press bottom bearing cup (Item 15) in case.
2.
Press bearing cones (Item 13 and 14) on fan shaft (Item
10).
3.
Lower fan shaft into case until bearing cone mates with
bearlng cup.
4.
Press top bearing cup (Item 11 ) into case.
5.
Install labyrinth ring (Item 8) and adjust cap screws (Item
16) until a bearing preload of 5 to 15 inch pounds is
obtained. Measure the gap between the labyrinth ring and
the case. Make a shim pack (Item 9) equal to the thickness
of this gap. Remove ring and install shim pack. Reinstall
labyrinth ring and check bearing preload. If necessary,
adjust shim gap to obtain the proper bearing preload .
INSTALLATION OF RING GEAR HUB
1.
Attach ring gear (Item 12) to hub (Item 6). (Use 30 to 35
foot pounds torque on place bolts.)
2.
Press ring gear hub on the fan shaft.
CAUTION: Block the end of the fan shaft while pressing
hub on shaft. Do not press against top bearing. The
tapped hole (5/8-11NC x 1.00 deep) in the end of the fan
shaft may be used to pull the hub on. (If the tapped hole
is used, check around the hole after the hub is on to be
sure there are no raised edges that would keep the shims
(Item 5.1 ) from seating properly against the shaft.) Stop
the bottom edge of the hub approximately .100 from the
end of the shaft.
INSTALLATION OF PINION CAGE
1.
The “X” marked pinion and gear teeth should be clearly
identified with chalk or other markings which can be seen
from the inspection opening or the bottom of the case.
2.
Find the difference between the pinion setting distance of
the old gear and the new pinion gear and adjust the old
shim pack (Item 2.3) or make a new shim pack to compen-
sate for the different setting distances.