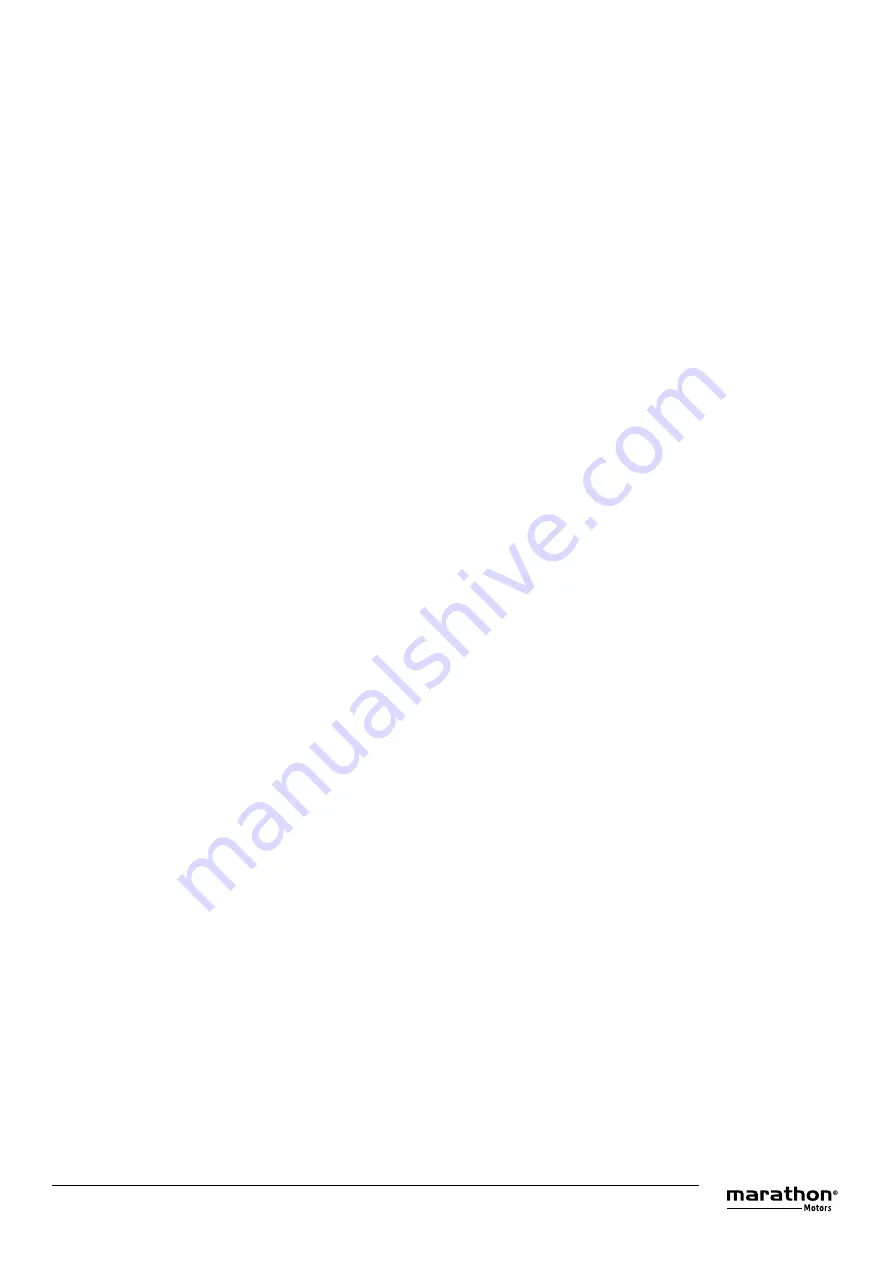
4
©2019, 2020 Regal Beloit Corporation, All Rights Reserved. MCIM2022E • Form# SB0250E
3.3 STORAGE
When the motor is not for immediate use, store as follows:
• Clean and dry location.
• Avoid locations with large temperature swings that will result
in condensation.
• Motors must be covered to eliminate airborne dust and dirt
build up on the motor.
• If the storage location exhibits high vibration, place isolation
pads under motor to minimize damage to motor bearings.
3.3.1 BEARING LUBRICATION:
Bearings are grease packed at
the factory; relubrication upon receipt of motor or while in storage
is not necessary. If stored more than one year, add grease per
Lubrication Instructions (see section 7.5) before start-up.
3.3.2 SHAFT ROTATION:
Rotate the motor shaft 5 - 10
rotations every three months to distribute the grease in the
bearings. This will reduce the chance for corrosion to form
on the bearing rolling elements and raceways.
NOTE:
Shaft seals and bearing seals may add drag.
3.3.3 DAMP OR HUMID STORAGE LOCATIONS:
Treat unpainted flanges, shafts, and fittings with a rust
inhibitor. Apply appropriate power to the motor’s space
heaters (if so equipped) or utilize a trickle heating system
to minimize condensation on motor windings.
3.3.4 MOTOR WINDING:
Stator winding should be insulation
resistance tested once every two-month period to ensure
that the integrity of the winding insulation has been
maintained. If winding resistance to ground is less than 1.5
Meg-ohms, consult the local authorized service shop before
energizing the motor.
4.0 INSTALLATION
The following items should be considered on installation to ensure
reliable operation of the motor.
4.1 SURROUNDINGS
• Ensure that the motor is properly protected against ingress of
oil, water or dust especially if construction work is in progress
around the motor. Motors should be installed in an area that
is protected from direct sunlight, corrosives, harmful gases
or liquids, dust, metallic particles, and vibration. A motor with
the proper enclosure for the expected operating condition
should be selected.
• Ensure air intake is not obstructed. Refer to dimension BL in
this document, free flow of air around the motor should not be
obstructed. Provide accessible clearance for cleaning, repair,
service, and inspections.
• When installing hazardous location motors, make sure that
the zone, group or division and class along with temperature
codes on nameplate are compiled with.
• Standard motor ambient temperature range: -20°C to +50°C.
Extended ambient temperature range: -40°C to +60°C (if
marked on nameplate). Fans, if utilized, for ambients below
-20°C require aluminum construction.
NOTICE:
INSULATION DEGRADATION
Insulation at high temperatures ages at an accelerated rate.
Each 10°C increase in temperature reduces the insulation
life by half.
4.2 MOUNTING
4.2.1 RIGID BASE (FOOT MOUNTED):
The motor must be
securely installed to a rigid foundation or a mounting surface to
minimize vibration and maintain alignment between the motor
shaft and the load’s shaft. The mounting surfaces of the four
mounting pads must be flat within 0.25mm for IEC 132 frame
and smaller; 0.38mm for IEC 160 frame and larger; 0.010 inches
for NEMA 210 frame & smaller; 0.015 inches for NEMA 250
frame & larger. This may be accomplished by shims under the
motor feet. The number of shims used should be kept as low
as possible, i.e. stack as few as possible. For special isolation
mounting, contact manufacturer for assistance.
4.2.2 VERTICAL MOUNTING:
When motors are being
mounted vertically, all the existing lifting eyes and hoisting
straps, if any, and/or belts should be used to stabilize the
position of the motor. Standard IEC
®
* 225 frame and above
(NEMA
®
* 360 & above) foot mounted (rigid base) motors are
not suitable for vertical shaft up/down application, special higher
grade (FG250) frame casting needed for such applications.
WARNING!
FALLING OBJECT HAZARD
The lifting provision on standard horizontal foot mounted (rigid
base) motors are not designed for lifting the motor in a vertical
shaft up or shaft down position. (see 3.2.1 lifting angles). Lifting
method / provisions for mounting a foot mounted (rigid base)
motor vertically is the responsibility of the installer.
Most standard horizontal motors IEC 80-315 frame and thru
NEMA 140-449 frame (excludes IEC 355 & above frames
and brake motors) can be mounted in a vertical shaft down
orientation. IEC 355 & above frames use angular contact
bearings. For vertical brake motors see section 4.7.1
When the motor is installed vertically with the shaft end
facing downwards, a protective cover for the fan cover is
recommended to prevent foreign objects from falling into
the motor.
When the motor is installed with the shaft end facing
upwards, the end user must prevent the ingress of fluid along
the shaft or contact manufacturer for assistance.
NOTICE:
BEARING FAILURE.
Unless approved by the motor
manufacturer do NOT direct couple a vertical shaft up or roller
bearing motor. Direct coupling a vertical shaft up motor or a
motor with a roller bearing may result in bearing damage.
4.3 APPLICATION ASSEMBLY TO THE MOTOR
4.3.1 PULLEYS AND COUPLINGS
• Pulleys or couplings should be independently balanced
with a half key as the motor rotor is balanced with a half
key during manufacture.
• In fitting pulleys or couplings to the motor shaft, care
must be taken to ensure that the roller/ball bearings are
not damaged. Both shaft and coupling bore should be
cleaned and lubricated. If the fit is still too tight, the pulley
or coupling should be pre-heated in air or oil to enable
easy assembly.
• Shock methods must not be used in fitting or removing
pulleys or couplings. Proper wheel or pulley removers
should be used to prevent shaft and bearing damage.
Tapped holes are provided in shaft extensions to assist in
the fitting of couplings and/or pulleys.
4.3.2 PULLEY AND BELTS
• If the motor is to be coupled to the load using pulleys and
belts it is important to ensure that the belt tension does
not exceed the safe working radial load of the motor.
NOTICE:
Excessive radial load will lead to reduced bearing
life with the potential of breaking the motor shaft. Because
of this, care must be taken to ensure the correct selection
of pulley size and type (toothed, vee or flat) and this is best
done in consultation with the power transmission supplier.
• The belt manufacturer’s recommendations for installation,
alignment and tensioning must be strictly adhered to when
fitting belt drives.
*The following trademarks or tradenames are not owned or under the control of Regal Beloit Corporation: NEMA is a trademark or tradename
of National Electrical Manufacturers Association; IEC is a trademark or tradename of International Electrotechnical Commission.