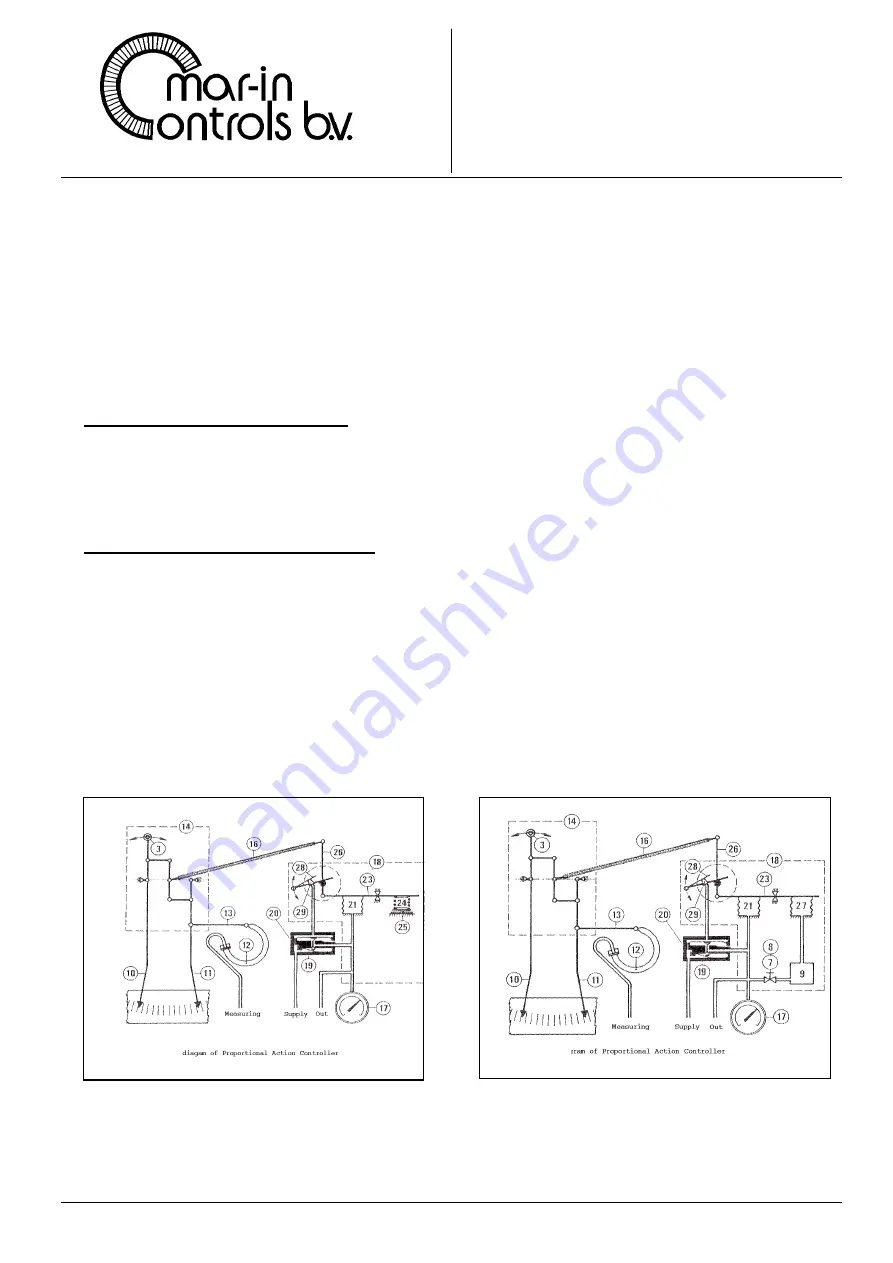
PNEUMATIC CONTROLLER
SERIES
SG6100
Page: 8
MAR-IN CONTROLS B.V. VAN UTRECHTWEG 8 –10 KRIMPEN A/D IJSSEL THE NETHERLANDS
Tel. + 31 (0)180 - 51 71 51 Fax +31 (0)180 - 51 89 14 [email protected] www.mar-in-controls.com
To reduce the temperature of the process fluid in the measuring instrument (when needed), use a
pipe coil and put pressure on the instrument slowly, taking care not to discharge the coil or on the
contrary, to avoid freezing or solidification of the process fluid.
Normally the operating pressure should never exceed 2/3 of its range. For allowed overpressures
we refer to the technical specification of the element.
Before putting into operation:
- Check the seal of fittings under pressure
- Vent and purge the line to remove moisture and solids
- Check the zeroing. If necessary adjust the zero for the presence of liquid head in the line.
PNEUMATIC SIGNAL RECEIVERS
For the linkage with the transmitter use, preferably, new and clean copper pipes, o.d. 6 mm, i.d. 4
mm. Mount the instrument with a block needle valve. It is important that the connection between
the instrument and transmitter is "leak"-free. To check for leaks apply a solution of soap water onto
the connections. Before connecting the instrument purge the airline to remove moisture and solids.
Description of operation (fig. 4&5)
Series SG 6100 controllers are motion balance type control units. The balance position is reached
and maintained by the composition of motions that are acting on a system of levers. The system
senses the difference of position on the scale between the Set pointer (10) and the measured
(process) index (11). This is transmitted through the lever (26) to the control unit (18). The unit
send the control signal to the pneumatic control valve and therefore provides (in a typical system)
to bring back:
- The measure index in
proximity
of Set pointer in controllers which have a Proportional Action
(manual reset)
- The measure index in
coincidence
of Set pointer in controllers which have a Proportional plus
Integral Action (automatic reset)
Fig. 4 - P action controller
Fig. 5- PI action controller