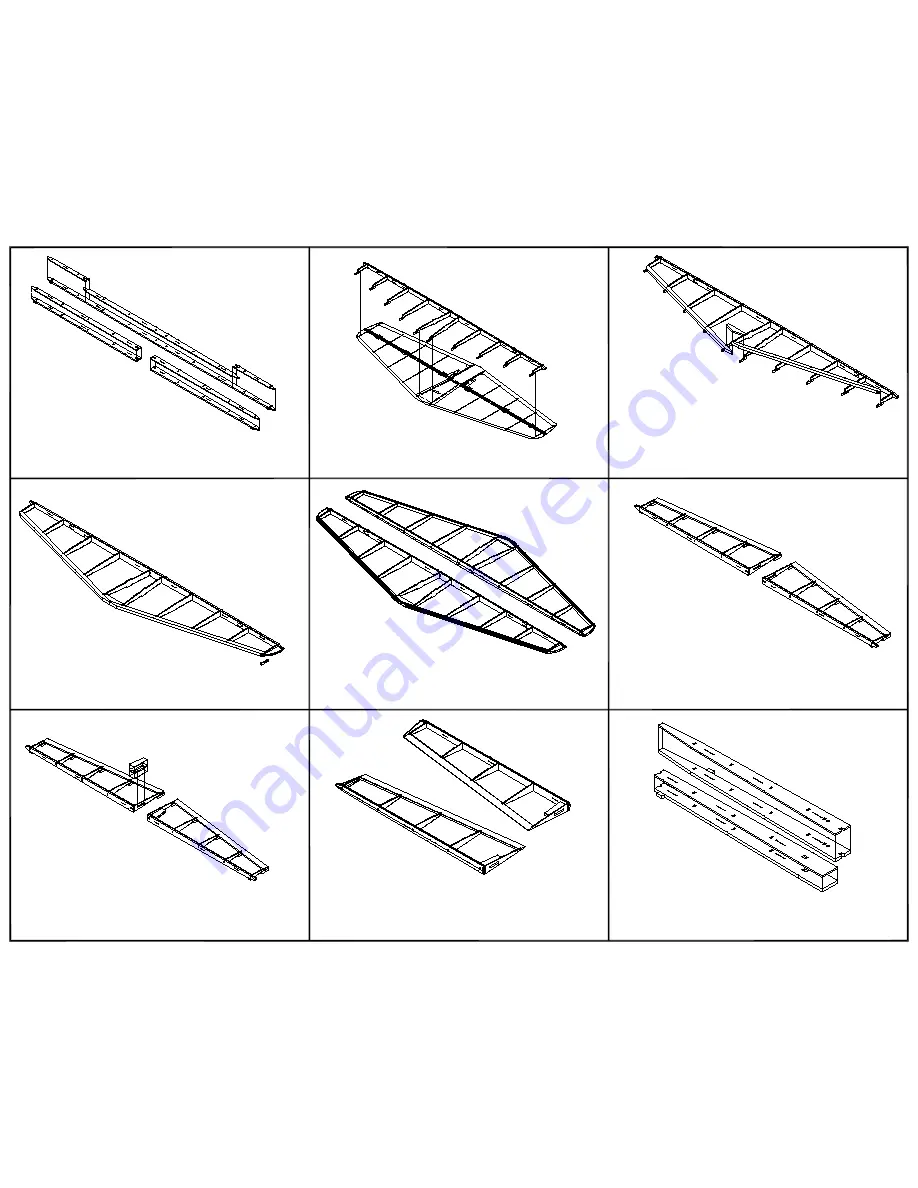
1.
Begin with the stab and elevators. Assembly begins by
laminating the spars. They are made up from a lamination of 1/8"
balsa and a lamination of 1/16" plywood.
Dry fit the stab ribs to the stab spar. Make sure the tabs on the
spar tips face down.The plywood laminations faces the r bs.
Place the assembly over the plan.
With the stab assembly lined up over the plan, dry fit the leading
edges to the r bs. They will lie flat on the rib tabs. The nose of
each rib fits in the leading edge notches. When everything is
properly aligned apply glue to all joints. Also glue the 1/8" balsa
joined to the center joint of the leading edge pieces.
2.
3.
4.
5.
6.
7.
8.
9.
Remove the stab assembly from the plan. The r b and spar tabs
can be removed at this time. The 1/16" balsa center section
sheeting will be installed during the final assembly steps.
Glue the stab tips to the assembly. The leading edge, tips, and the
back side of the spar can now be sanded to shape. Refer to the
plan cross section drawings for the shape of the spar back face.
The elevators are assembled using the same procedure as the
stab. Dry fit the r bs to the spars and then place on the plan. The
plywood side of the spars face the ribs. Add the trailing edge
pieces so the rear of each rib engages the notches. When
everything is lined up glue all of the joints.
Plywood boxes made from laminations of 1/32" plywood are used
to transfer the elevator control horn inputs to the elevator halves.
Glue the parts for each horn box and then install them in the
elevator halves. The tabs fit in elevator rib E1.
Remove the r b and spar tabs. Glue the elevator tips to the
assemblies. Sand the forward edge of each elevator half to the
profile shown on the plan cross section drawing. Sand the trailing
edge to a taper following the the rib top and bottom profile. Also
sand the elevator tips.
The fin and rudder assembly is very similar to the stab and
elevator halves. Begin by making up the fin and rudder spars.
They are laminated from 1/8" balsa and 1/16" plywood.
Содержание deHavilland DHC-1 Chipmunk
Страница 1: ...deHavilland DHC 1 Chipmunk Assembly Guide Manzano Laser Works ...
Страница 3: ......
Страница 4: ......
Страница 5: ......
Страница 6: ......
Страница 7: ......
Страница 8: ......
Страница 9: ......
Страница 10: ......
Страница 11: ...TAIL SURFACES ASSEMBLY ...
Страница 14: ...WING ASSEMBLY ...
Страница 19: ...FUSELAGE ASSEMBLY ...
Страница 24: ...FINAL STRUCTURAL ASSEMBLY ...