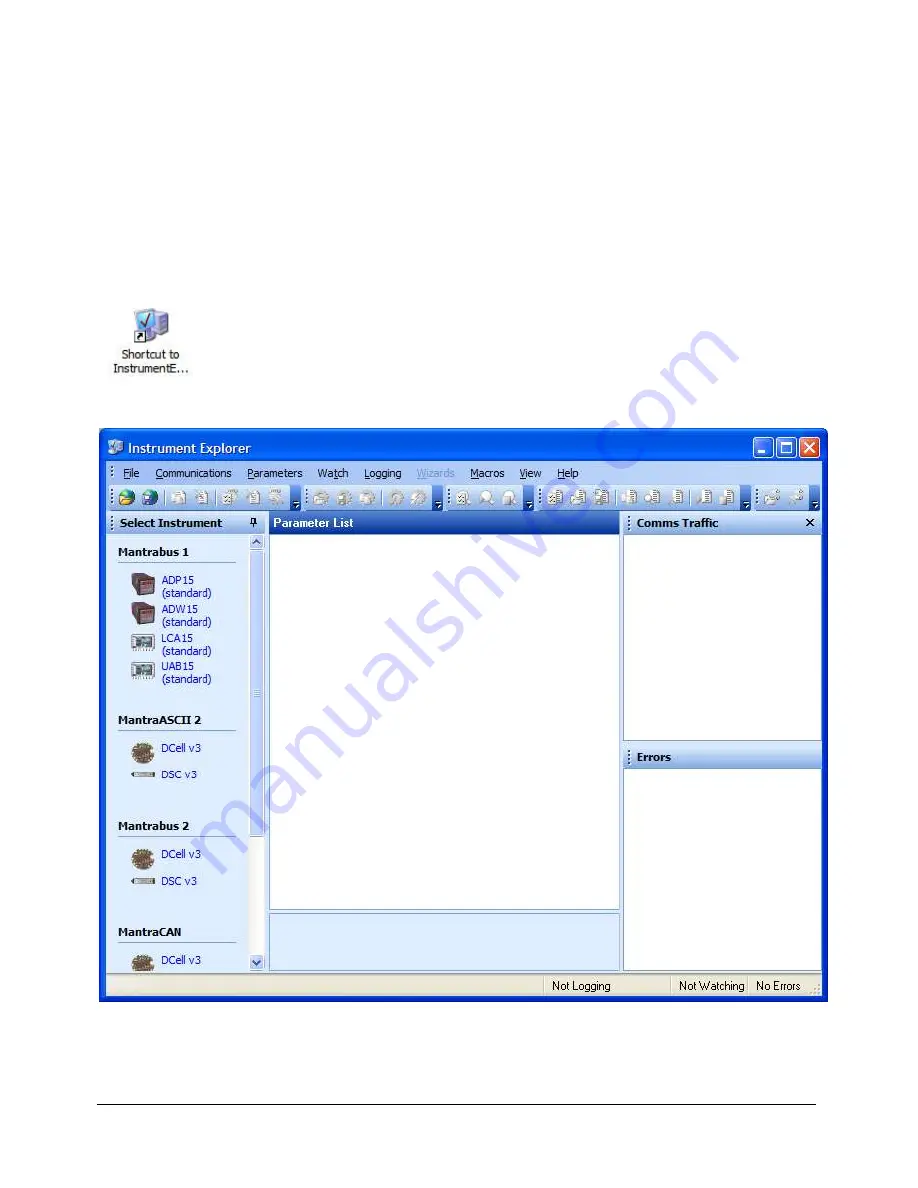
Mantracourt Electronics Limited
DCell & DSC MantraCAN User Manual
10
Shortcut icons can be created on your desktop and shortcut bar. After installation you may be asked to restart the
computer. This should be done before proceeding with communications.
When given the option to install IXXAT CAN drivers ensure these are selected, which is the default.
Running the Instrument Explorer Software
Having installed Instrument Explorer you can now run the application, which the rest of this chapter is based
around.
From the Windows ‘Start’ button, select
Programs
, then
Instrument Explorer
or click on the shortcut on your
desktop.
Instrument Explorer Icon
The application should open and look like the following screen shot. Instrument Explorer Window
The layout of Instrument Explorers Window and child windows allows the user full customisation to their
requirements. If the application show a different arrangement of child windows than the above screen shot then
using then load one of the default workspaces as follows: