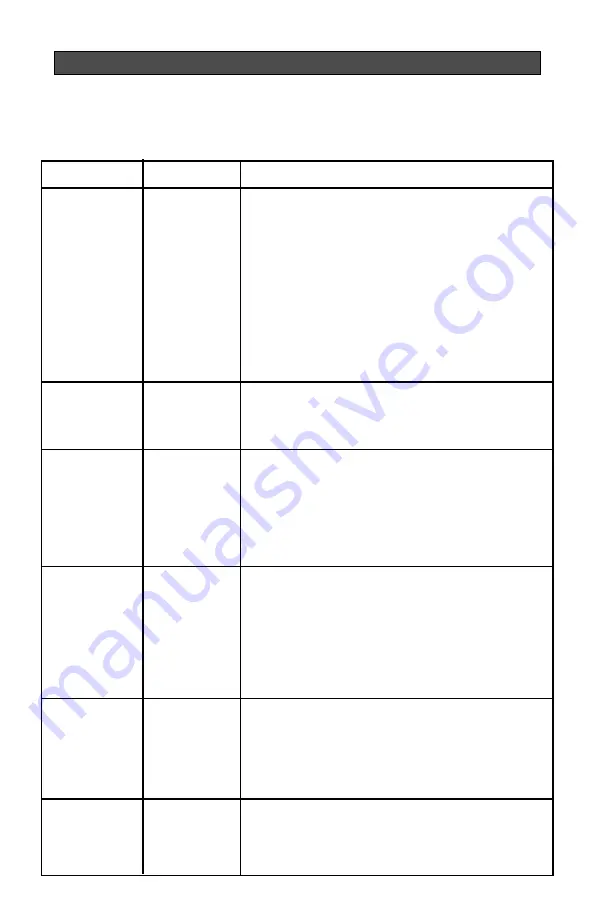
Page
14
TROUBLESHOOTING GUIDE
PERFORMING REPAIRS MAY EXPOSE VOLTAGE
SOURCES, MOVING PARTS OR COMPRESSED AIR
SOURCES. PERSONAL INJURY MAY OCCUR. PRIOR TO
ATTEMPTING ANY REPAIRS, UNPLUG THE COMPRESSOR
AND BLEED OFF TANK AIR PRESSURE.
CAUSE
Defective
pressure
switch.
Improper
wiring.
Fittings are
not tight
enough.
Defective or
dirty check
valve.
Defective
pressure
switch
unloader
valve, or
defective
check valve.
Defective air
tank.
Blown head
gasket.
CORRECTION
• Move the pressure switch lever to the
"OFF" position. If the unit doesn't shut
off, unplug. If the electrical contacts are
welded together, replace the pressure
switch.
• If the contacts are good, check to see if
the pin in the pressure release valve is
stuck. If it does not move freely, replace
the valve.
• Adjust or replace pressure switch.
Tighten fittings where air can be heard
escaping. Check fittings with a soap and
water solution. DO NOT OVER TIGHTEN.
A defective check valve results in a
constant air leak at the pressure release
valve where there is a pressure in the tank
and the compressor is shut off. Remove
and clean or replace check valve. DO
NOT OVER TIGHTEN.
Contact a trained service technician.
Air tank must be replaced. Do not repair
the leak. WARNING DO NOT DRILL
INTO, WELD OR OTHERWISE MODIFY
AIR TANK OR IT WILL WEAKEN. THE
TANK CAN RUPTURE OR EXPLODE.
Replace gasket or contact Authorized
Service Technician.
PROBLEM
Excessive
tank
pressure -
safety valve
pops off.
Air leaks at
fittings.
Air leaks at
or inside
check
valve.
Air leaks at
pressure
switch
unloader
valve.
Air leaks in
air tank or
at air tank
welds.
Air leaks
between
head and
valve plate.