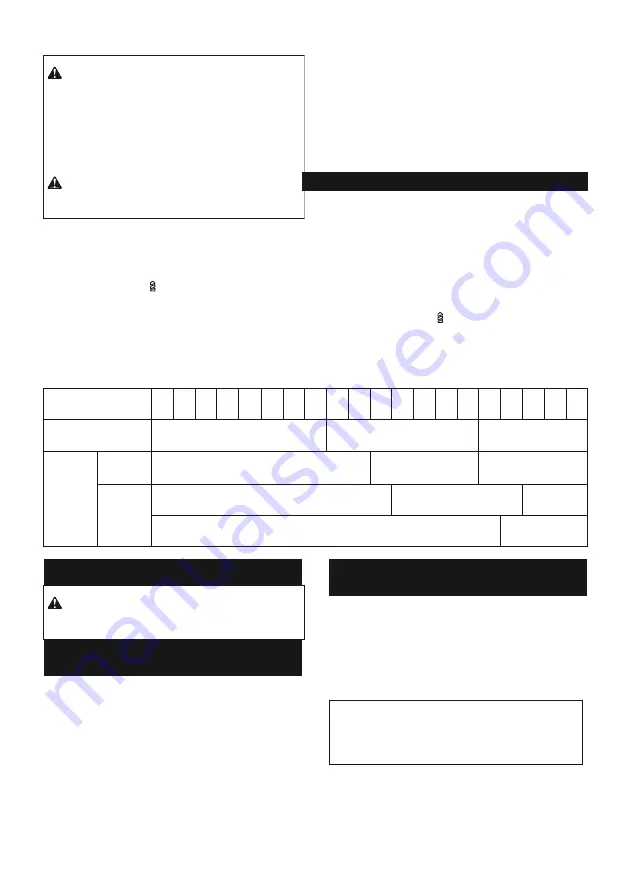
10 ENGLISH
To
change
the
speed,
switch
off
the
tool
first.
Select
the
"2"
side
for
high
speed
or
"1"
for
low
speed
but
high
ASSEMBLY
CAUTION:
Always be sure that the tool is
switched off and the battery cartridge is removed
before carrying out any work on the tool.
Installing or removing driver bit/
drill bit
For Model DF333D (optional accessory)
►
Fig.8:
1.
Sleeve
2.
Close
3.
Open
Turn the sleeve counterclockwise to open the chuck
jaws.
Place
the
driver
bit/drill
bit
in
the
chuck
as
far
as it will go. Turn the sleeve clockwise to
tighten the chuck.
To
remove
the
driver
bit/drill
bit,
turn
the
sleeve
counterclockwise.
Installing or removing driver bit/
socket bit
For Model DF033D (optional accessory)
►
Fig.9
Use
only
driver
bit/socket bit
that
has
inserting
portion
shown
in
the
figure.
Do
not
use
any
other
driver
bit/socket bit.
NOTE:
Both
shallower type
(A=12
mm,
B=9
mm)
and
deeper
type
(A=17
mm,
B=14
mm)
of
driver
bits
can
be
used.
To
install
the
driver
bit,
pull
the
sleeve
in
the
direction
of
the
arrow
and
insert
the
driver
bit
into
CAUTION:
Always set the speed change lever
fully to the correct position.
If
you
operate
the
tool
with
the
speed
change
lever
positioned halfway
between
the
"1"
side
and
"2"
side,
the
tool
may
be
damaged.
CAUTION:
Do not use the speed change lever
while the tool is running.
The
tool
may
be
damaged.
torque. Be sure that the speed change lever is set to the
correct
position
before
operation.
If the
tool
speed
is
coming
down
extremely during
the
operation
with "2", slide the lever to the "1" and restart the operation.
Adjusting the fastening torque
►
Fig.7:
1.
Adjusting ring
2.
Graduation
3.
Arrow
The
fastening torque
can
be
adjusted
in
21
levels
by
turning
the
adjusting ring.
Align
the
graduations
with
the
arrow
on
the
tool
body.
You
can
get
the
minimum fastening torque
at
1
and
maximum torque
at
marking. The
clutch
will
slip
at
various
torque
levels
when
set
at
the
number
1
to
20.
The
clutch
does
not
work
at
the marking.
Before
actual
operation, drive
a
trial
screw
into
your
material
or
a
piece
of
duplicate material
to
determine which
torque level is required for a particular application.
The
following
shows
the
rough
guide
of
the
relationship between
the
screw
size
and
graduation.
Graduation
1
2
3
4
5
6
7
8
9
10
11
12
13
14
15
16
17
18
19
20
Machine screw
M4
M5
M6
Wood
screw
Soft wood
(e.g. pine)
–
ɸ
3.5 x 22
ɸ
4.1 x 38
Hard wood
(e.g. lauan)
–
ɸ
3.5 x 22
–
–
ɸ
4.1 x 38
Содержание DF033D
Страница 2: ...2 1 2 Fig 1 Fig 2 3 ...
Страница 3: ...3 Fig 3 Fig 7 Fig 4 Fig 9 Fig 13 1 1 2 3 1 3 2 1 Fig 8 ...
Страница 4: ...4 Fig 12 Fig 16 1 2 Fig 17 ...
Страница 81: ...Anjo Aichi 446 8502 Japan www makita com CS U K R O D E 20180802 ...