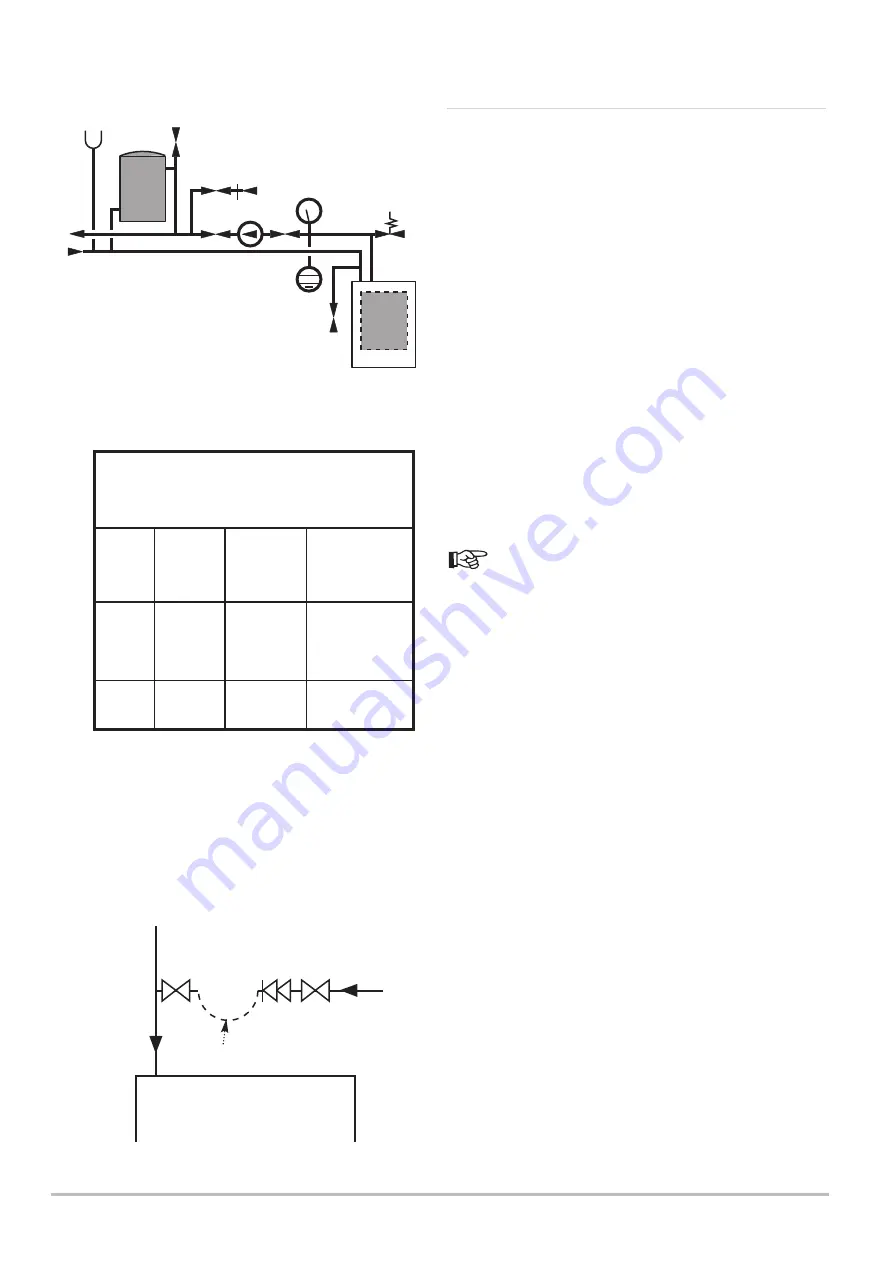
26
Eco Compact Heat
7726859-01 (1/19)
5
Before Installation
5.2.9 Sealed Systems Details
1.
SaFETY VaLVE
- A safety valve complying with the
requirements of BS EN ISO 4126-1 must be fitted close to the
boiler on the flow pipe by means of a horizontal or vertically
upward connection with no intervening valve or restrictions and
should be positioned to facilitate testing. The valve should be
pre-set and non-adjustable to operate at a pressure of 3 bar . It
must be arranged to discharge any water or steam through a
pipe to a safe outlet position.
2.
PRESSURE gaUgE
- A pressure gauge of minimum range
0-4 bar with a fill pressure indicator must be fitted to the
system, preferably at the same point as the expansion vessel in
an easily visible position.
3.
EXPanSiOn VESSEL
- An expansion vessel complying with
the requirements of BS EN 13831 must be fitted to the system
by means of a connection close to the inlet side of the
circulating pump in accordance with the manufacturers
instructions, the connecting pipe being unrestricted and not
less than 15mm nominal size. The volume of the vessel should
be suitable for the system water content and the nitrogen or air
charge pressure should not be less than the system static head
(See Table. 1a).
Further details of sealed system design can be
obtained from BS EN 12828, 12831 & 14336 and the British
Gas publication entitled 'Specifications for Domestic Wet
Central Heating Systems'.
4.
FiLLing POinT
- A filling point connection on the central
heating return pipework must be provided to facilitate initial
filling and pressurising and also any subsequent water loss
replacement / refilling. The sealed primary circuits may be filled
or replenished by means of a temporary connection between
the primary circuit and a supply pipe provided a ‘Listed’ double
check valve or some other no less effective backflow
prevention device is permanently connected at the inlet to the
circuit and the temporary connection is removed after use. The
filling method adopted must be in accordance with all relevant
water supply regulations and use approved equipment.
Your attention is drawn to, for GB: Guidance G24.2 and
recommendation R24.2 of the Water Regulations Guide. for IE:
the current edition of I.S. 813 “Domestic Gas Installations”.
5.
MaKE UP SYSTEM
- A method of replacing water lost from
the system should be provided either by means of a make up
vessel of not more than 3 litres capacity, mounted above the
highest point of the system, or by re-pressurisation of the
system.
6.
VEnTing
- A method of venting the system during filling and
commissioning is provided by an automatic air vent fitted inside
the boiler. The air vent is supplied in the open position.
7.
HOT WaTER STORagE
- The hot water storage vessel
must be of the indirect coil type. All components used in the
system must be suitable for operation at 110°C and at the
pressure allowed by the safety valve.
Safety
Valve
Pressure
Gauge
Pump
Filling
Point
Air
Vent
3 Litre Top Up Bottle
(if required)
Radiator
Circuit
Expansion
Vessel
System Drains
at Low Point
Max Boiler Flow
Temp = 82° C
Boiler
Fig. 7
Table. 1a
Vessel
Charge
Pressure
(Bar)
0.5
1.0
1.5
Initial
System
Pressure
(Bar)
0.5
1.0
1.5
2.0
1.0
1.5
2.0
1.5
2.0
Multiply Total
Water Content
Of System By
(Litres)
0.067
0.112
0.207
0.441
0.087
0.152
0.330
0.125
0.265
Method of determining minimum expansion
vessel volume for sealed systems
System Volume = 75 litres
Vessel Charge Pressure = 1.0 bar
Initial System Pressure = 1.5 bar
75 x 0.152 = 11.4 litres
Expansion Vessel Volume
Example :-
Then :-
nOTE
Where a vessel of the calculated size is not obtainable
then the next available larger size should be used.
Stop
Valve
Double
Check
Valve
Mains
Cold
Supply
CH
Return
Temporary
Hose
Stop
Valve
Fig. 8
Static
Head
( m)
<5
<10
<15
Содержание Eco Compact Heat 15
Страница 62: ...62 notes ...
Страница 63: ...63 notes ...